There is nothing to be gained from trying to reinvent the wheel, it’s often said. But that hasn’t stopped engineers at Protean Electric from attempting to refine it, at the very least.
The fruit of these labours is the development of an in-wheel electric direct-drive system for pure electric, hybrid and plug-in hybrid vehicles. The technology, comprising motor, power electronics, control and brake in a single package, fits neatly inside a conventional 18in wheel, making it applicable to a variety of vehicles, from family saloons to vans.
There are some obvious benefits to the in-wheel approach. The high-torque, low-speed motors feature integrated micro inverters, control electronics and software – so eliminating the need for a separate large, heavy and costly inverter. Part count, complexity and cost are reduced, as there is no need to integrate traditional drivetrain components such as external gearing, transmissions, driveshafts, axles and differentials. The fully integrated technology therefore promises some key advantages, including improved fuel economy and increased power.
The idea of having an individual in-wheel motor driving each wheel of a vehicle is not new – indeed, in 1900 Ferdinand Porsche debuted such a concept at the World’s Fair in Paris. But it has never been refined and adopted by a big carmaker.
“We are not claiming it’s new, but what is different with our system is that we started with a clean sheet of paper,” says Andrew Vallance, business development manager at Surrey-based Protean Electric, which employs 80 staff, two-thirds of whom are engineers.
“The mistake a lot of people have made was to take a conventional electric motor and try to fit it inside the wheel of a car. That means they ended up with lots of complex engineering: trying to get a speed-reduction gearbox in the wheel meant problems with packaging of the brakes, requirements for custom-made alloy wheels, alterations to the suspension architecture of the vehicle, or some other compromise.
“The blank-sheet-of-paper approach means we have been able to design something specifically for mounting in the wheel of a vehicle. It offers high-torque, low-speed performance with multiple levels of redundancy. It is also robust.”
Each motor is packaged in the unused space behind a conventional 18in- to-24in wheel and can use a conventional automotive wheel bearing. The motors require no gearboxes, driveshafts or differentials, bringing the potential for far greater flexibility for designers. Reduced drivetrain losses mean less energy is wasted during acceleration and regenerative braking. This means that more of the energy from the battery pack is available to propel the vehicle.
Protean says that each in-wheel motor can be controlled entirely independently, providing far greater control, and better performance and vehicle dynamics, than any other drive system. In addition, traction control, launch control and torque vectoring are all easily implemented through the use of in-wheel motors.
“It’s a flexible technology,” says Vallance. “By fitting into a standard 18in wheel, it allows us to target small- to medium-sized saloons, SUVs, pick-up trucks and commercial vehicles. It could be used on a two- or four-wheel drive vehicle, pure electric, or as torque assist for a hybrid. One product can be used in many ways.”
The technology also allows for through-the-road hybrid configuration. That’s the concept of taking an existing vehicle, making no changes to the drivetrain, and simply adding an electric drivetrain to it. “For example, if you have a front-wheel drive vehicle, you could put these motors on the rear wheels, have a small battery pack, with no need to have another gearbox or power electronics, and now you can drive all-electric mode, engine-only, or a hybrid four-wheel drive combination of the two. That’s not something you can do with a conventional system. It would be too large, too heavy and take up too much space.”
The performance characteristics are impressive. Peak output per motor is 81kW, with continuous output power of 64kW. Peak torque is 800Nm, with continuous output torque of 500Nm. The nominal input voltage range is 200-400V DC.
That kind of performance has seen the technology tested in a variety of demonstration vehicles. Protean motors were fitted in the rear wheels of a Brabus hybrid based on the Mercedes-Benz E-Class with a diesel engine. The installation enabled reuse of the powered rear axle, while requiring no tear-up of the base powertrain. There were also minimal body-in-white changes.
Combined electric motor and diesel engine acceleration on the demonstrator was recorded as 0-100km/h (0-62mph) in 7.4 seconds. Acceleration from 60 to 120km/h (37-75mph) took 5.6 seconds. “That was a much better performance than the original vehicle,” says Vallance. “The battery was fitted under the boot floor. It would not have been possible to package a conventional system with additional gearboxes and large power electronics in the vehicle.”
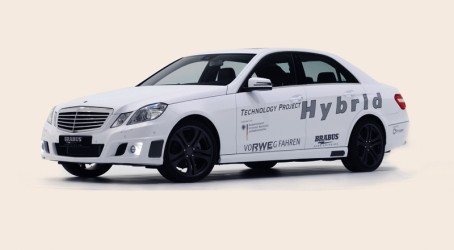
The technology has also been demonstrated using four Protean motors on a Brabus fully electric Mercedes-Benz E-Class, achieving peak combined power of 320kW and 3,200Nm torque.
A slightly more unconventional vehicle, a Ford F-150 pure electric pick-up truck, was fitted with four Protean in-wheel motors. The 3,200kg gross weight F-150 recorded a 100-mile range, with 100mph top speed. “That is competitive with most smaller electric vehicles but in the most unlikely, unsubtle pick-up truck,” says Vallance. “The direct-drive system took up no space inside the vehicle. The batteries were mounted underneath the cabin floor between the chassis rails.”
The Protean technology has been in development for five years. The company has built more than 150 motors in total and has carried out extensive durability testing, including more than 100 hours of operation on the pave-block pavement surface at the Millbrook automotive testing ground in Bedfordshire. Protean’s Surrey facility has two dynamometers, using National Instruments test software for interpretation of results.
Vallance says that Protean’s evolutionary approach to design will deliver an extremely reliable product. “From each iteration we have learned things we can do better,” he says. “We have made the technology cheaper, more power-dense, easier to fit and more robust.
“There is not one magic bullet – it’s a process of improvement. Durability testing is ongoing – but once in full production the motors will be lifetime components.”
The plan is to start manufacturing the motors in high volumes next year. While Protean’s Farnham facility will continue to handle technology demonstration and prototype build, volume production will be carried out at a plant being built in China. “Initially we will sell the in-wheel system ourselves, but eventually we want to license it to tier-one suppliers and OEMs. Discussions are ongoing and we hope to make announcements soon,” says Vallance.
Unsprung mass considerations
A common challenge to the packaging advantages of in-wheel motors is the trade-off required by moving the drivetrain mass from the sprung to unsprung. A commonly cited rule of thumb suggests that an increase in the unsprung mass/sprung mass ratio would result in vehicles with poorer ride quality.
Protean’s Andrew Vallance says that perceived problems with unsprung mass are blown out of proportion. He says research by Lotus Engineering suggests that top-of-the-segment performance can be achieved with simple techniques, such as changes to bushings and top mounts. “The Lotus work used objective, subjective and numerical analyses to investigate the effects of increased unsprung mass on a vehicle,” he says.
The Lotus report says that “the understanding gained from this study has led Lotus to believe that the small performance deficit could be largely recovered through design changes to the suspension compliance bushes, top mounts, power-assisted steering characteristics and damping, all part of a typical new vehicle tuning programme.”
These conclusions are supported by a number of other papers.
In-wheel motor history
The concept of individual in-wheel motors driving each wheel of a vehicle was first considered many years ago. In 1900 at the World’s Fair in Paris, Ferdinand Porsche debuted the System Lohner-Porsche, featuring an electric vehicle driven by two in-wheel motors. This vehicle was capable of reaching more than 35mph and went on to set several speed records.
Later Porsche used internal combustion engines from Daimler and Panhard, connecting them to generators to provide power for the in-wheel motors. This effectively represented the world’s first series hybrid vehicle, the System Mixt.
Vehicles driven by Porsche’s in-wheel motors (in electric and series hybrid variations) continued to claim more speed records in two- and four-wheel drive configurations, resulting in Porsche winning the 1905 Poetting Prize as Austria’s outstanding automotive designer. By 1906, more than 300 Lohner-Porsche vehicles had been built using in-wheel motors – ranging from cars to trucks and fire engines.