Articles
The waterjet-powered navy vessel has us outmanoeuvred as we cruise on the sailing ship on Lake Vänern, the largest lake in Sweden, on a fine summer’s evening.
As our ship leisurely makes its way towards land with a contingent of Rolls-Royce customers and crew on board, we are treated to a demonstration by the navy craft of the power of waterjet technology: rapid acceleration and deceleration, the ability to turn on a sixpence, attributes that make it a choice for high-speed operation among ferry operators as well as the military.
We are in the Swedish town of Kristinehamn to celebrate 40 years of research at Rolls-Royce’s Hydrodynamic Research Centre and to observe production of propellers and waterjets at the nearby Gustavsvik site. Both are key elements of Rolls’ marine division, which employs 9,000 people globally.
The origins of the research centre and factory lie in the Swedish company Kamewa, which became part of the Vickers Ulstein Marine Group in 1999, and was subsequently acquired by Rolls-Royce. Kamewa was producing propellers as early as 1937 and had inaugurated a test laboratory in the early 1940s. The lab now known as the Rolls-Royce Hydrodynamic Research Centre was created in 1970.
The lab is moving with the times. The key trend affecting operations is the desire for improved environmental performance among Rolls-Royce’s customers. Göran Grunditz, its manager, says: “Since I started 11 years ago, we have seen an increased requirement for fuel efficiency and the request for more environmentally-friendly designs.
“And that comes back to us in hydrodynamics, because it’s us that can deliver better propulsive efficiency.”
Testing of propeller designs at Kristinehamn involves physical testing and computer modelling. The key phenomenon that engineers observe is the process of cavitation, or the formation of empty cavities in a liquid by high forces and the immediate implosion of them – a liquid is a continuum and repairs itself if it is torn apart. Cavitation occurs when a liquid is subjected to rapid changes of pressure, causing the formation of cavities in the lower-pressure regions of the liquid.
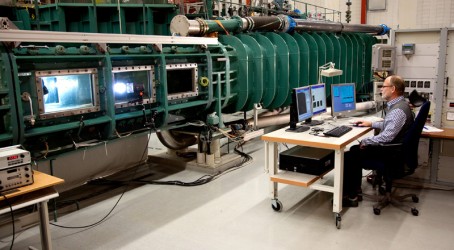
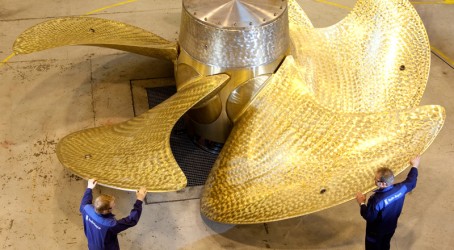
Cavitation can be a significant cause of wear – when entering high-pressure areas these bubbles collapse on a metal surface continuously, causing cyclic stressing of the metal. In ships, cavitation can cause erosion of components, unacceptable noise and vibration, and a breakdown of torque and thrust. The aim of the engineers at the research centre is to ensure that propeller designs do not create these problems. As well as physical testing, simulation of propeller designs in operation in water is also carried out through computational fluid dynamics (CFD).
Cavitation on propellers was first observed in the late 19th century and the first cavitation test tunnel – think of a wind tunnel for marine components – was opened in 1897 in the UK. Kamewa built its first cavitation tunnel in 1942. The Hydrodynamic Research Centre was designed to feature two cavitation tunnels, where water is circulated to assess the performance of a ship’s propulsion system. It was decided that the new lab should comprise a conventional cavitation tunnel with a volume of 117m³ and another with a free water surface containing 400m³. At the time, only two other free-surface tunnels existed, in Washington DC and Berlin. A free surface was required for testing surface-piercing propellers, which it was thought were likely to become more widely used for fast vessels.
The tunnels simulate a wide range of sea conditions, reflecting temperature, water flow and salt levels. Since 1971 the computer-controlled tunnels have evaluated more than 1,000 propeller blade designs and carried out tests on more than 300 complete propeller models. Engineers create scale models of propellers, which are tested in the tunnels. Profiles are altered and refined. The work that engineers do in the lab feeds into the manufacturing of propellers, waterjets and other systems. During cavitation tests, high-speed videos and photos are taken to observe the process. Observation with strobe lights is also typically carried out to allow engineers to see what is happening even when a propeller is moving at high speed. Propellers and waterjets are mature technologies, having been under development for many years.
Jan-Eric Carlson of the lab says: “All conceivable propeller and waterjet types have been tested.” The focus at the lab is on incremental improvements to propeller design and better understanding of the interaction between propeller, waterjet and hull to reduce fuel consumption. Grunditz says: “The propeller is a rather mature product, so to gain something you need to see beyond the propeller and consider the complete propulsion system – that’s why we have developed systems that integrate the rudder and propeller: the Rolls-Royce Promas system.”
Cavitation will remain a key area of focus in terms of improving propeller and propulsion system design, but reducing it is not straightforward as smaller propellers – necessary for greater efficiency – are not as good in terms of cavitation performance as big blades with a large surface area. Grunditz says: “When we need to gain efficiency we need to work with a smaller blade. On the other hand, if you wish to avoid cavitation you have a big blade area to distribute the force over a large area, but that costs in terms of efficiency. So we need to continue to focus on reducing cavitation.”
It will be some time before the physical testing that the research centre makes possible is replaced by simulation, if ever. So the cavitation tunnels will continue to play an important role in the next 40 years of the lab’s history. Grunditz says: “There is still a long way to go before we use CFD for cavitation simulations in the day-to-day work. Designing high-performance propellers requires physical models.
“But it’s both a short- and long-term aim to bring more CFD into the design process.”