The International Energy Agency says that 100 billion cubic metres of unwanted gas is burnt off from oilfields globally every year – enough to satisfy the entire annual gas needs of Germany and France combined.
Even without considering the waste of resources, the effect on the environment and human health of so much flaring gas should be enough to spur action. The huge volumes of toxic SOx and NOx, partially combusted materials, CO and CO2 that pour into the atmosphere are linked to high mortality rates, according to medical studies. In places where burning off gas occurs in a relatively concentrated area, such as the Niger Delta, the average life expectancy is 43 years. The infant mortality rate in the delta is the highest in Nigeria – 12% of babies die during their first year.
Burning off the unwanted “associated” gases that are brought to the surface when oil is extracted is illegal in most countries. But it still plagues parts of the under-developed world and has even become economically exploited by some communities. According to Brian Songhurst, chairman of the oil and natural gas subject group at the IChemE, the ground flares in the Niger Delta have become so accepted that local communities use the waste heat from them to dry their crops. When engineers turned up to stop the flares, the locals protested.
At a conference organised by the oil and natural gas subject group at the IChemE, Songhurst said: “The challenge is that the quantities of gas are quite small, around 10-30 million cubic metres, and the flares are dispersed over a large area, not one large quantity of gas in one place. The infrastructure to bring that together is expensive and difficult. There is also a declining production flow for associated gas, which impacts on the return on investment.”
The economics of processing and transporting associated gas is the largest barrier to introducing technologies to deal with it. Plant needs to be installed to clean and contain the gas, and infrastructure has to be put in place to transport it. Oilfields are often in remote places, making plant and infrastructure commercially unviable. There is also a problem in selling the gas as customers tend not to see the value in something that is freely burnt.
There are a number of options available to end flaring once and for all, and even put the unwanted gas to good use. The most common, particularly in offshore oilfields, is to use the gas on site. Associated gas can be used to generate power and drive plant and equipment and can also be reinjected into the oil reservoir.
Reinjection requires extra plant and uses a lot of energy. A riser brings the associated gas to the surface for processing, which includes dehydration. Pressure lost when the gas is brought up is then reintroduced so it can be reinjected into the reservoir.
Reinjection has been used to good effect to enhance oil recovery in the Brent fields in the North Sea. The first stage of oil recovery uses water but using oil to push out oil from reservoirs can increase recovery rates substantially. Engineers have to be careful to maintain the correct pressure in the reservoir and to ensure that the gas does not break through the production wells, which can halt production.
Greg Birrel, reservoir engineer at Tullow Oil, says that incorporating reinjection to avoiding flaring in offshore projects can increase their capital expenditure by between 10 and 15%. “We look at reinjection as a cost of doing business. It’s not an economic decision at the moment – it’s an environmental consideration.”
Another option for gas flaring is to turn it into electricity using gas or steam turbines. Surplus electrical power can be exported to an electricity grid to provide income for the well owners. According to Ian Amos, SGT product strategy manager for Siemens Industrial Turbomachinery, between 60 and 70% of customers for the firm’s range of turbines up to 50MW are in the oil and gas sector. Siemens has installed turbines to convert associated gases at plants in Nigeria and West Siberia.
About 20 million cubic feet per day can produce around 200MW of thermal energy and provide mechanical power. One of the big advantages of a gas turbine is that it is not that fussy about the exact nature of the fuel going into it, although some impurities will cause problems. Liquids and solids will cause overheating and damage, and hydrogen sulphide can form on hot areas of a turbine and cause corrosion.
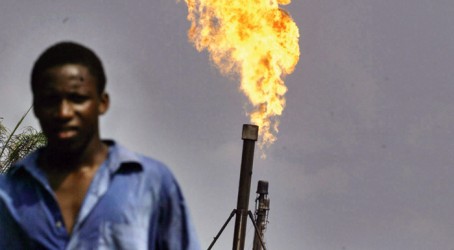
But most gases will go straight through a gas turbine without causing damage. “The interesting part is the cost of fuel,” says Amos. “Is associated gas really free? Industrial sites in the UK buy millions of dollars of gas per year but because gas is so cheap industry doesn’t want to invest in the infrastructure.”
Avoiding that cost, whether for wire or pipeline, is something that Nick Harbord, managing director of Global CNG Solutions, promises with his “virtual pipeline”. If you are not turning associated gas into electricity or using it all on site, then it must be transported elsewhere for use, he says. There are a few technologies that can achieve this. A natural gas pipeline is the most desirable,but its commercial viability depends on geography such as the distance to the customer. Gas can be transported in two other forms, as compressed or liquefied (CNG or LNG).
The most suitable technology depends on the distance to the end user, the amount of associated gas available and its value on the market. “There is no single solution. It is about what fits a particular project at a particular time,” says Harbord. “Sometimes it’s a combination of more than one. Our CNG solution is a transitional solution that allows you to eventually go to pipeline.”
Global CNG Solutions specifies and installs the process equipment necessary to set up a “virtual pipeline”. First the gas is cleaned to at least “pipeline quality” and compressed to 250bar at the production site. It is then transported by road, rail or sea to a pressure reduction station, then distributed and used. The firm has worked on one flare gas project and several projects involving extracting and transporting biomethane from rubbish dumps in the UK. It has also worked in Tanzania, Kazakhstan and Nigeria.
CNG is most suitable when the amount of associated gas is small. Above 5 million standard cubic feet a day it may make more sense to liquefy the gas. LNG is a well proven technology, and although transported mostly by ship, it can also be moved by rail and road. LNG is not used offshore but the technology is being looked at.
Luisa Shelenko, of GL Noble Denton, says using LNG is more difficult than CNG. “It’s larger plant and if your gas composition varies and your flow rates differ, you are going to have problems,” she says. “For small-scale operations, CNG is the better option, but as the flow rates increase LNG takes over because it makes more sense economically.”
The final option for transporting and distributing associated gas is to change it to a liquid, to make it more portable. Methanol or a Fischer-Tropsch (FT)-based hydrocarbon are the choices. There are a few recent examples of this process such as the Shell Pearl GTL plant in Qatar and Methanol Holdings plant in Trinidad which, at 5000 tonnes per day, is the largest producer of methanol in the world.
The process has been proven suitable for associated gas by Davy Process Technology, which built a demonstrator FT plant in Nikiski, Alaska. The firm commissioned the plant in 2003 and shut it down last year after successfully demonstrating the process as suitable for small-scale standalone units using its compact steam reformer. However, the technology remains complex, a possible drawback when considering locations where it would be used for associated gas. Tim Gamblin, of Davy Process Technology, says: “We’ve proved it works and started talks for licensing the technology. It’s for onshore only at the moment but we are working on offshore.”
Engineers have responded to the wastefulness and destructiveness of gas flaring with several technical solutions but it remains up to the politicians and global oil corporations to carry through these technologies. There is movement – Shell, Total and Eni announced in May that they would commit $2 billion to reducing flaring by piping it rather than burning it. But the proof, as ever, is in action rather than easy press release commitments.