This year is shaping up as the one when hydrogen fuel cell cars become a fixed prospect on the horizon. Five of the big global car makers have so far announced plans for mass market versions of this type of car. In January, BMW and Toyota announced a partnership to develop a fuel cell system by 2020. This was quickly followed by the signing of an unusual three-way collaboration, between Daimler, Ford and Renault-Nissan, to develop a similar “common fuel cell system” for mass-market vehicles by 2017.
Those five car companies join the ranks of Honda and Hyundai, which already both produce hydrogen fuel cell cars in small numbers. Honda’s first Clarity FCX rolled out in 2008, and Hyundai began manufacturing a fuel cell version of its ix35 sport utility vehicle in Korea last month. Both cars are available on lease as part of pilot programmes designed to gather data for the ramping up to mass market production from 2015.
Despite the usual fanfare of zero emissions and exhausts dripping water, the long remaining development times revealed in these recent announcements show that mainstream use of hydrogen fuel cell cars is still some way off. The research and development partnerships in particular are indicative of the biggest barrier to the introduction of hydrogen fuel cell electric vehicles – cost.
Ever since the first fuel cell vehicle was built almost 50 years ago (see “Fifty years in the making”, overleaf), the expense of the rare metals and exotic materials used in fuel cell stacks has restricted their mass market potential. The cost of materials has been a “significant point of focus” for fuel cell developers, according to Dennis Hayter, vice president of business development for Intelligent Energy, which develops low-carbon fuel cell systems.
“There are those who have been looking at how to reduce the quantities of precious metals, such as the platinum and exotic metals used in the PEM [proton exchange membrane]. And there are those who have come up with arrangements that are entirely exotic material- and precious metal-free,” he says. “Whichever way you go, it’s a problem everybody’s been looking at, and the supply chain has become more complicated as a consequence.”
According to Hayter, this R&D focus has resulted in a halving of the quantity of platinum in most modern PEM fuel cells, the type of fuel cell stack that Intelligent Energy started developing 12 years ago and the most commonly used in transport applications. During this period, Intelligent Energy has produced several fuel cell technology demonstrators, including a black cab, a motorbike, even a aircraft. However, as with most companies in the sector, it has yet to penetrate the transport mass market.
“Hydrogen fuel cells have always been at least 10 years away,” he says. “But there has been an incredible amount of activity in the background. We have to make sure the technology does what it’s meant to do, which is difficult in the context of unknown codes and standards. We’ve spent a lot of time extending the technology’s capabilities, making sure it can deal with extremes of heat and cold and that it performs in particular environments, such as in the air.
“Then you have practical limitations to consider – what it actually takes to put a fuel cell vehicle on the road. You have to transition from low-volume builds to production-level builds. Then when you do have the large quantities, what does it take to provide the refuelling infrastructure?”
The need to create a refuelling network is another obstacle to the adoption of hydrogen fuel cell vehicles. Some experts argue that hydrogen fuel cell technology is
now mature enough for the government to disrupt the chicken-and-egg scenario it has been trapped in with the refuelling infrastructure for the past decade, by providing incentives.
A report published this month by industry group UKH2Mobility contains analysis and modelling about the infrastructure required to make driving a hydrogen vehicle viable. The report suggests that “65 stations across the UK could provide sufficient initial coverage to start the market”, but admits that the early stations will not be able to deliver satisfactory returns on investment. “Some support for seeding the market may be required,” it concludes. The next phase of the report will put together more detailed business cases for the initial hydrogen refuelling network and the support it will require.
UKH2Mobility members include government representatives, several interested commercial partners and fuel cell developers including ITM Power, which produces stationary fuel cells and modular, self-contained hydrogen refuelling stations. Dr Graham Cooley, ITM’s chief executive, says that the development of fuel cell vehicles and hydrogen infrastructure is now happening “far faster” than in the past, because of the backing of the major car companies.
“The hydrogen car has been designed by the car companies so the user doesn’t have to change their behaviour,” he says. “They can refuel in three minutes and go 400 miles. The world’s been designed like that – that’s the system between major cities. Plus, you’re still rolling out an electric drivetrain. The difference is that it has a fuel cell instead of a battery and a tank to store the energy as fuel - it’s ‘refuel’ rather than ‘recharge’.”
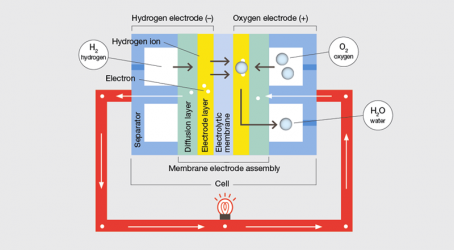
The presence of a fuel cell and tank may seem a trite point of difference to highlight, but it does reinforce that much of a fuel cell car is the same as an electric car. The engineering of electric drivetrains, components and systems is now in full swing for EVs and hybrids at car firms around the world. What was a leap to hydrogen is now scaled down to a jump.
However, the use of hydrogen as a fuel, and its storage in a vehicle, still presents its own set of safety problems. Specifically, these are distributing and containing a highly pressurised explosive gas in a consumer-friendly way. These concerns have been addressed, though, says Cooley: “The tanks are wound with carbon fibre, so they can only dent and pierce. If there’s a breach, it’s difficult for the gas to find an ignition source. It goes up and is gone in seconds.”
Dr Steven Voller, chief executive of Cella Energy, which works on safe, low-cost hydrogen storage technology, disagrees. He cites safety concerns about hydrogen, alongside cost, as the biggest factors holding hydrogen fuel cell cars back. “Even research scientists who are used to handling these sorts of gases send the tanks away for refilling,” he says. “We’re talking about putting into cars something that is two to three times the pressure of those cylinders and letting people refill them themselves. Can you imagine getting an insurance quote? Then you have to persuade people to put their kids on top of these tanks and drive around.
“But the biggest barrier is cost. You need an 850-bar (85 million Pa) hydrogen pump to fill one of these tanks. Each costs about $2 million to put in. That’s not going to happen at every forecourt in the country.”
Perhaps global car companies’ commitment, combined with government support, will help hydrogen fuel cell vehicles on their way. But that the exact time of their arrival remains fuzzy is not a surprise. This perennially “just round the corner” technology may have been moving towards us faster, but it still has many challenges stacked against it.
Concept proved by pioneer van – but stalled by prohibitive cost
General Motors developed the world’s first fuel cell vehicle in 1966. The Electrovan experimental vehicle – a converted GMC Handivan – took a team of 250 people two years to build. The van showed electric propulsion with fuel cells was feasible. It had a top speed of 70mph (113kph), could accelerate from 0-60mph (0-97kph) in 30 seconds and had a range of around 150 miles (241km).
The Electrovan’s fuel cell supplied about 32kW with a peak output of 160kW and comprised 32 thin-electrode fuel cell modules connected in series. The motor and control system were mounted between and under the two front seats. Also beneath the floor were the fuel cell modules interconnected by around 550ft (168m) of plastic piping. Cryogenic hydrogen and oxygen tanks, and an electrolyte reservoir, were mounted behind the middle bench seat. Around 45 gallons (205 litres) of potassium hydroxide was used as the electrolyte. This filled the modules, piping and the reservoir and weighed around 550lb (249kg) on its own. The van’s total weight was 7,100lb (3,220kg).
After the Electrovan was built, tested and shown off to journalists in 1966, the project was scrapped, largely because its cost was prohibitive. According to GM, the cost of the platinum used in the fuel cell was enough to “buy a whole fleet of vans”, and at the time there was no supporting hydrogen infrastructure in place.
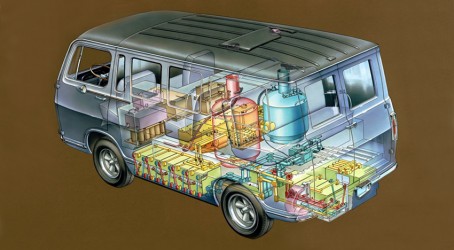
Electric power from hydrogen: how the fuel cell works
Fuel cells produce electricity through a silent electrochemical reaction. They are usually categorised by their electrolyte, which determines the chemistry within the cell, the catalysts for the chemical reaction, the fuel, the cell’s operational temperature range, and the applications for which the cell is suitable.
Five main types are commercially available. Most transport applications, including the Honda and Hyundai hydrogen fuel cell cars, use the proton exchange membrane (PEM) type. Another type, phosphoric acid, is sometimes used to power larger vehicles such as buses.
PEMs are used in automotive applications because they have a fast start-up time and low sensitivity to orientation, combined with a favourable power-to-weight ratio and a relatively low operating temperature of around 80°C. However, PEMs are not an ideal solution, and come with disadvantages, such as the expensive catalysts required, the high sensitivity to fuel impurities, and the requirement for a pure hydrogen feed.
Most fuel cell systems consist of four basic components: the fuel cell stack, the fuel processor, current inverters and conditioners, and a heat recovery system. The stack, the heart of the system, comprises fuel cells stacked to produce meaningful amounts of electricity. Other components and subsystems control variables such as humidity, temperature, gas pressure and wastewater.
In a PEM fuel cell stack, the PEM is sandwiched between the anode and cathode, which are in turn sandwiched between bipolar plates. The hydrogen fuel flows between the plate and the anode, where it diffuses with the catalyst – usually platinum – into positive hydrogen ions and negative hydrogen electrons. The membrane allows only hydrogen ions through, enabling the electrons to be separated out as electricity in a circuit. At the cathode, oxygen reacts with the electrons and the hydrogen ions that have traveled from the anode through the electrolyte to form water.