The idea of an electric car successfully travelling the whole length of an entire continent was once probably thought impossible. Mainly designed to just travel around towns and cities, an electric vehicle wouldn’t have the range, battery power and general capability to survive such a challenge.
But a flagship project at London’s Imperial College, called Racing Green Endurance (RGE), last month saw the SRZero electric sports car cross the finishing line on the world’s longest road, the Pan-American Highway. It’s no exaggeration to say that such an achievement could change how we view electric cars forever.
Starting at Chena Hot Springs in Alaska, the roofless supercar began its 26,000km journey along the highway on 3 July. It then travelled through 14 countries, crossing Canada, the US, Mexico and South America, before finally reaching the finishing line in Tierra del Fuego, Argentina, on 16 November.
A six-man engineering team from Imperial took it in turns to drive the car each day, with two travelling in the vehicle at a time. The rest of the team, accompanied by a camera crew, were seated in a support vehicle that followed behind. This vehicle also held the equipment and spare parts needed to fix the supercar and replace its components, if and when it ran into problems.
Travelling such an epic distance in an electric vehicle is mightily impressive, but the project wasn’t just set up to give Imperial’s engineers an ego boost and have some once-in-a-lifetime fun behind the steering wheel. The aim was to push the boundaries of the technology and show the public what electric cars are really capable of. The project was also intended to encourage school children to take up engineering at college and university and think about it as a future career.
Nikolaus Sauer, chief mechanical engineer of RGE, had previously worked at Imperial College, engineering other electric vehicles. He says he wanted to go one step further in showing people that electric cars are an alternative for future transport, are “cool” and are not “boring and slow”. So what better way to prove that than with the ultimate test-drive along the world’s longest road?
“We wanted to prove that you can do something amazing with an electric car and excite people about it,” he says.
Since August last year, the RGE team had been working closely with Peterborough firm Radical Sportscars to produce the SRZero. Team RGE custom designed it, then Radical portscars built the car.
The vehicle, which works in a similar way to an automatic car, includes technology that is used in race cars. The chassis, including the frame, body and suspension, is similar to that of a race car. But small, low-energy consumption tyres are used, rather than the large types often used on race cars.
Weighing 1,100kg, the supercar has a top speed of 200km/h and can accelerate from 0 to 100km/h in seven seconds. Unlike electric city cars, which have a range of around 160 kilometres, the SRZero has a maximum range of 500km. It takes eight hours to fully charge. The style of the vehicle wasn’t just chosen to help with its performance. The designers wanted to make it stand out during the journey.
Sauer says: “If you push technology in terms of the powertrain, but not in terms of looks, then people won’t notice you. They won’t even realise that it is a non-petrol car when you drive past, whereas with this car people are so amazed they have to look.”
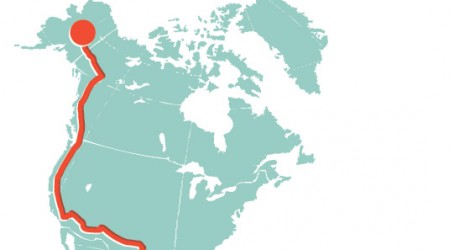
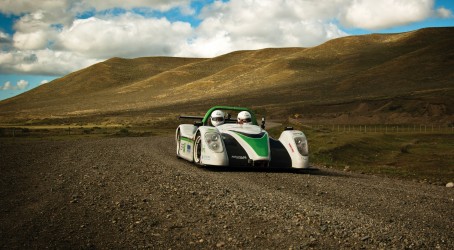
The supercar has two Evoelectric motors in the rear. Using two motors eliminates the need for a mechanical differential while doubling the amount of power available. The vehicle also contains two US-manufactured electric motor controllers. These are very high density small motor controllers, which usually need to be three times the size. Sauer says there are only two of these controllers in the world, both of which are in the SRZero. The controllers change the DC output provided by the batteries into an AC current needed to drive the motors. They not only facilitate the driving of the motors, but also regenerative braking of the vehicle, which allows kinetic energy to be recovered whenever the driver brakes.
A CompactRio controller, which National Instruments has supplied for the car, manages all of the components in the powertrain. It also controls a battery management system, which prevents overcharging, if one battery is more charged than another, and over-discharging. The system also manages the motor controllers, driver interface and safety systems.
“You will end up overcharging if you don’t have this system,” says Sauer. “Likewise, when you discharge, and one battery is emptier than all the others, you can over-discharge it and damage it.
“You can have a much safer driving experience,” he adds.
The batteries themselves use Thunder Sky lithium iron phosphate cells that have a total capacity of 54kWh. Peak power from the battery pack can exceed 400hp. The pack consists of a little over 160 cells, while some other batteries for electric cars have around 6,000. Because of the chemistry of the batteries, in the event of a crash they won’t explode, which can be a problem with lithium polymer battery types.
To prepare for the 26,000km journey, the team did research to find out about the type of roads they would be travelling on. But, having only tested the car in Britain on “normal roads”, Sauer says they were never really sure how it would perform on the Pan-American Highway. The team also had to drive in the most extreme weather. “Literally any kind of climate you could imagine we had, from snow to desert to mountains to tropical rain,” he says.
One of the more dangerous experiences for Sauer and his team was when they drove through Guatemala. They had to navigate their way around numerous potholes, all the while getting drenched in extreme heavy rain.
Such conditions caused the car to suffer a few problems. The rear shock absorbers snapped as the team approached the Mexican border. The shock absorbers had to be taken to a workshop to be fixed, allowing the team to drive another 1,000 miles before the components were finally replaced in Mexico City. The car also had a few very minor electrical difficulties due to days of continuous heavy rain, which caused problems with the control system. Altogether such problems delayed the journey to the finish by a month. But, despite everything, Sauer says the team never had any doubt that they would get there.
“Every problem has a solution. If anything goes wrong, we built the car; we know every bolt of it.”
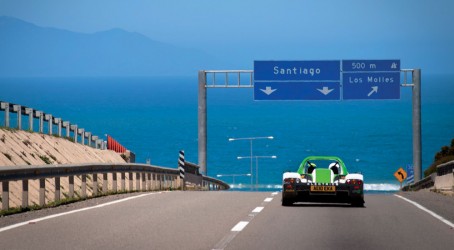
The team had a lot of support throughout the journey. Numerous hotels allowed them to charge the vehicle overnight, and a university provided them with space to service the car. “You do have to do quite a bit of servicing,” says Sauer. “This is a prototype so there is no other car like this. All the components are pretty much unique in the world.”
Charging the supercar also had to be planned in advance, especially in Mexico, where the electricity supply was low. Sauer says it was important to never let the car be in a situation where the battery could run out. The team solved this problem by evaluating car performance and predicting how much energy it used during different drive cycles.
“We did get worried sometimes thinking we are going to run out,” he says. “But, having driven the car in different terrain, we could very precisely predict how much energy we were going to use. It takes a bit of experience, but then it is quite easy to judge where you are going to charge and how far you can get in a certain condition.”
Overall, Sauer says the car performed “outstandingly” well and much better than expected. He says: “We had horror visions of having to replace entire body work somewhere. But for the kind of roads we’ve driven, and the conditions, it’s done extremely well.”
The team collected a large amount of data about the car’s performance. An onboard computer logged data on temperatures, motor controllers, the batteries, speed and acceleration, and on how well the car performed in different climates.
“We learnt a lot about our design, our systems, and the powertrain arrangement we put in,” says Sauer. “We know about the range better, we know what difference it makes to go in a hot environment or in a cold environment and how the batteries perform. Really it’s getting to know the car, and judging all of the parts of it, knowing their strengths and limits.”
As for the project’s aim of showing the public the full capability of electric vehicles, it was a job well done, as far as Sauer is concerned. “We have proved what we wanted to prove,” he says.
Volcanoes, snow caps and valleys
On a more personal note, the journey created some fantastic memories for the RGE team. From driving over San Francisco’s Golden Gate Bridge and speeding through the Mojave Desert, to racing over the Andes mountains and charging the car by the banks of the Panama Canal, they saw some of the world’s most spectacular scenery. So it’s not surprising that Nikolaus Sauer, chief mechanical engineer of RGE, can’t decide what his favourite part of the journey was.
“It’s really hard to say because of the amount of landscapes you see,” says Sauer. “Every day you get filled with a whole set of experiences that you have never had before. Every day is different.”
But he does say that seeing Colombia and Ecuador was a particular highlight. “The tropical rainforests and mountains – it was really impressive,” he says. “The stunning views, with volcanoes in the distance with snow caps and huge valleys, that really takes your breath.”
Even now, Sauer’s whole experience of travelling the full length of the Pan-American Highway is hard to take in, and he still can’t believe he completed the 26,000km journey in an electric supercar.
“It is amazing, really amazing to have finished it and that the car is still in one piece,” he says.