For 16-year-old Jordan Newman, it was a “no brainer”. During a two-week work experience placement at Troup Bywaters + Anders (TB+A), a building services engineering partnership, he had become “really interested” in engineering. Back then, five years ago, when TB+A offered him an apprenticeship, he jumped at it, because it allowed him “to study for relevant qualifications, gain first-hand knowledge and get paid”.
For Newman, the choice was arguably easy, because his family had always encouraged him to join an apprenticeship scheme. In the eyes of his friends, he took “a brave move” by skipping full-time education and missing out on the university lifestyle. Today, though, his mates agree that “it was the right thing to do, and wish they had taken a similar path,” says Newman.
If the government has its way, many more will follow in his footsteps. That’s why it decided to bring in the apprenticeship levy. First slated in summer 2015, the levy finally comes into force this month. The move is supposed to bring the UK on a par with Germany or at least the US, where companies realised long ago that – in the words of Chancellor Philip Hammond – “to compete in the fast-moving global economy, you have to link skills to jobs”.
The levy will hit any companies that spend more than £3 million a year on wages. They will have to bear a 0.5% levy on their annual pay bill, which will be taken at source each month through PAYE. Any company for which 0.5% of the wage bill amounts to £15,000 or less will not have to pay the levy.
Those companies that are exempt from the levy will receive funding for 90% of their apprenticeship training costs. For small companies with fewer than 50 staff, the government will pay training costs in full for apprentices aged 16-18.
The final fund will translate into “vouchers” sitting in a digital account that companies can use to invest in apprentice training and assessment. The government will also apply a 10% top-up, paid monthly. Employers will have 24 months to use or lose the funds on their apprentices.
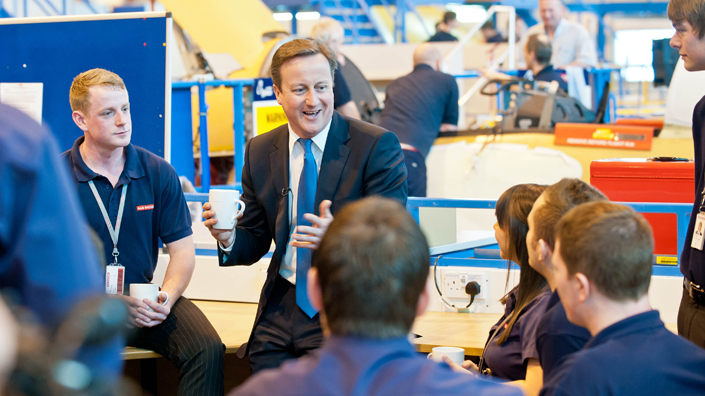
Positive outlook
The government’s vision is to create three million apprenticeships by 2020. And there’s certainly a lot to be said for apprenticeships. According to the Centre for Economics and Business Research, they contribute £34 billion a year to the economy, and reduce youth unemployment. In 2014 alone, the system gave work to 99,000 extra people.
“Apprenticeships are also key to filling the skills gap within the UK,” says Anne Wilson, one of the directors of the Engineering Industries Association (EIA). Indeed, 186,000 people with engineering skills are needed each year until 2024.
Of course, the levy is ultimately designed to benefit young people by defining a vocational career path. Apprenticeships are a first step into employment, provide valuable practical experience on the job, and help young people to work their way up – potentially all the way to degree-level qualifications and professional chartered status. Given the soaring costs of university education, apprentices can map out a long-term career and gain relevant qualifications without going into heavy debt to get a student loan.
For Jordan Newman at TB+A, it has certainly worked out. He’s now studying for his BEng in building services engineering at London South Bank University. The apprenticeship scheme works, he says, because it helps young engineers like himself and supports the company’s business model.
“I didn’t realise how engaging and supportive my colleagues would be towards young engineers,” he says. “As apprentices, we get fully involved in the projects, but also with wider business initiatives and mentoring new apprentices.”
His employer is happy too: “Through our apprenticeship scheme, Jordan has been provided with opportunities to progress both professionally and academically whilst being fully funded by us,” says Claire Oliver, HR manager at the firm. Last year, TB+A won the Medium Employer of the Year Award at the National Apprenticeship Awards.
The benefits of this route into employment and qualifications for young people like Newman are clear, but Oliver points out that, while the changes will “probably mean more opportunities” for young people, many apprentices “won’t necessarily see the changes for themselves, and often won’t have even heard of the levy”.
The business opportunity
So, what’s the reality of the new apprenticeship regulations for employers?
The levy has been a hot topic for firms since it was first announced in the 2015 summer budget. After an initially cool reception, the latest research from EEF, the manufacturers’ organisation, shows that firms may now be warming to some of the benefits. Just over a quarter of manufacturers – 26% – believe that the levy will increase the quality of apprenticeships, with the same percentage thinking it could attract more young people into the industry.
Companies are “keen to get skills and training that will help them to meet their productivity and growth targets,” says Verity O’Keefe, senior employment and skills policy adviser at the EEF, and hope that the levy will help them to run apprenticeship schemes that meet their needs.
Newman’s employer, TB+A, has prepared well for the changes. “To date, most of our apprenticeships have been geared around our core business,” says managing partner Neil Weller. “With the levy coming in, we are now looking to see whether there is a possibility to extend the scheme into our support roles as well. Our recruitment exercise for this year’s intake also started earlier, as we perceived there would be greater competition for candidates.”
The company hopes that the levy will have a positive effect by encouraging more firms to invest in training and development. “We believe that in the construction sector there is a growing skills gap that does need addressing,” says Weller. “With course fees at the level they are at, especially in our field of engineering, fewer young people are following the full-time study route at university, and apprenticeships are a great way to encourage youngsters to enter our particular field. It is also helping us address the gender gap that has been a cause for concern for a number of years now.”
However, many companies still have serious reservations about the levy’s viability and long-term sustainability, with 34% of those surveyed saying that they don’t see any benefits to the scheme at all. Many more are convinced that the levy is simply another tax on business. The EEF says that 75% of manufacturers are worried that, when it comes to value for money, they won’t get back what they put in. Others are concerned about cost (61%), timescale for implementation (50%) and uncertainty about future rule and rate changes (44%).
The complexity of the connected companies rule will see many more firms forced to pay the levy, yet not all will be eligible for the £15,000 allowance. At the same time, firms operating across the UK with employees in Scotland, Wales or Northern Ireland will also lose out on funding because of an incompatibility between the levy and the UK’s devolved skills policy. In other words, they will only get back the “English fraction” of what they’ve paid in.
The EEF has drawn up a range of recommendations to the government to help ensure that the policy is sustainable and fit for purpose. Requests include an independent, employer-led review of the implementation and roll-out of the levy by the end of 2018. “The apprenticeship levy remains a work-in-progress and must be treated as such,” says O’Keefe. “It requires further refining and we continue to urge the government to continue to engage with business to make some much-needed improvements.”
The EIA is highly critical of the levy, and is concerned that the new regulations will hit small and growing firms hardest. “The barrier to the levy being a huge success is that once again there is a clunky, ill-thought-out process, hastily railroaded in, appealing to potentially only 8% of the engineering companies,” says Wilson. “Published figures show that 92% of business is conducted through small and medium-sized employers.”
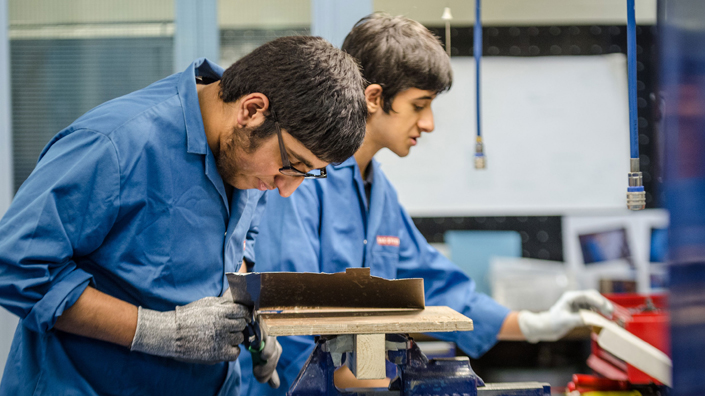
Challenges for small firms
According to the government’s Get In Go Far campaign – aiming to inspire 14- to 24-year-olds to consider apprenticeships, traineeships and work experience as a career route – small firms can reap rewards from hiring apprentices. Nearly all those surveyed (96%) reported at least one business benefit.
But research by XpertHR suggests that these firms may be less well prepared for the impact of the levy than large employers. Sheila Attwood, pay and benefits editor at XpertHR, says that some firms that must pay the levy, particularly smaller businesses, haven’t properly thought through the implications.
Smaller enterprises may struggle without dedicated legal and human resources teams to review and act on the complex government documentation. As a result, the big winners may be the training providers, which will be able to help small firms develop apprenticeship strategies – for a fee. Small firms could also now have substantial sums to invest in training, and so may need to suddenly boost the uptake of apprentices to make full use of the cash.
Yet, as a medium-sized company, TB+A is confident it has created a scheme that will transfer “fairly seamlessly” to fit the structure of the levy. “Our main challenge will be to look more closely at the timings of how our apprentices progress, say from a level 3 to a level 6 apprenticeship,” says Weller. However, the firm is aware of similar businesses that are not ready for the introduction of the new system.
Industry may need to pull together to make the best of the situation and demand an apprenticeship levy that works for everyone. TB+A’s role in a Trailblazer group – employers that work together to design new apprenticeship standards within their sectors – will place it in a position where it can help others. “We feel sure that, as the Trailblazers develop and some issues become apparent, we will be able to deal with the new Institute of Apprenticeships,” says Weller.
IMechE STRATEGY FOR TACKLING SKILLS SHORTAGE
The IMechE’s new publication, Apprenticeships in the Education and Skills Landscape of England, published this month, outlines key ways to tackle the skills shortage, which is particularly acute for skilled technical roles. The IMechE’s recommendations are for:
1. The engineering institutions to adapt to provide guidance on need, and ensure maintenance of personal competence standards, as apprenticeship volumes increase. Standards need to be developed for all vocational qualification levels as well as those that naturally fit the EngTech, IEng and CEng grades.
2. The government’s apprenticeship levy to fund engagement as well as provide quality delivery. Perceptions are as great a barrier as affordability for both the apprentice and the employer, especially for the small firms sector.
3. The government’s industrial strategy team to develop strong sectoral and regional plans. Solving issues one by one, such as advanced manufacturing skills, will have more impact than general incentives. More work such as the Department for Transport skills strategy should be encouraged.
4. Schools to be part of a modern, well-resourced careers strategy that will bring about changes in perceptions. The T-level qualifications will fail if they are not accompanied by a change in attitudes to technical education. Teachers and young people are guided by the regulatory framework placed on schools.
5. Government to reassess its approach to teachers’ continuing professional development. Investment in teaching as a career attracts more into the profession, with a consequent increase in subject awareness and interest from their students.
ACHIEVING DIVERSITY
Engineering apprenticeship starts are at their highest for 10 years, but girls still only make up 7% of the total. The government’s vision is for 20% of new entrants to engineering and technical apprenticeships to be women, and for a 20% increase in the proportion of apprentices started by young people from black, Asian and minority ethnic backgrounds by 2020.
Proponents of the levy argue that measures built into it can help create an increasingly diverse workforce. For example, additional payments will be given to providers training apprentices from deprived areas, and to those training apprentices who need intensive learning support, such as those with dyslexia, learning difficulties or physical disabilities.
The EEF argues that firms must step up their game to increase engagement with talent from minority groups. “The roots lie in encouraging greater numbers of young people to take Stem subjects,” says the EEF’s Verity O’Keefe. “It’s about making sure that parents and teachers are aware of what modern engineering and manufacturing are about and see the great career opportunities.”
“To truly increase diversity, small firms need to be involved in engagement,” says Anne Wilson of the Engineering Industries Association.