Articles
Do you think the downstream side of BP’s business is neglected?
No. Downstream is a real jewel in the crown of BP. It’s a valued business, and when we meet colleagues from across BP on training courses, having gained an understanding of what they do, my preference is still to work in lubricants and downstream.
BP manufactures and distributes a range of lubricants – everything from engine oils and brake fluids for cars, motorcycles and lawnmowers to heavy-duty lubricants for trucks, earthmovers and diggers, as well as for marine and other industrial applications. So it’s an exciting area of the business to be in and at the end of the day mechanical engineering underpins what we do.
What are the key challenges in developing lubricants?
Government regulations are increasing the limits on CO2 emissions from vehicles. That’s driving a lot of research and development. Now one of the most cost-effective ways of reducing CO2 from engines is in fuel-efficient lubricants. So we undertake a lot of work with OEMs to develop new fuel-efficient oils.
Products have to be thinner but still provide durability protection like their older, thicker predecessors. And that has to be achieved in smaller engines.
One way of approaching that challenge is to really understand the tribological contacts and the journey the oil makes through its lifetime. Simulation can help us to understand that, and then we work with our chemists to develop additives for those particular conditions.
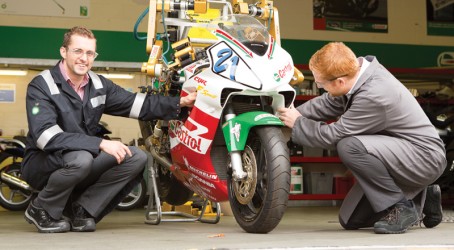
What’s day-to-day life like at BP?
My work day starts with a nine-mile offroad ride through the Berkshire countryside to the BP global HQ for formulated products technology in Pangbourne, a tiny village. Our offices are in 36 acres of woodland. This site is one of the jewels of the automotive industry.
I’m really trying to understand what the experience of oil is as it travels through an engine, as part of a major project. Through engineering analysis, it’s possible to enhance my understanding of engineering design. As the oil goes through the engine, it’s heated to very high temperatures and experiences high pressures. There are various things that combine with the oil that you have to deal with.
Where did you study engineering?
I studied at Bath University and took a masters in mechanical engineering with a specialisation in automotive. The principal reason I chose Bath was its Formula Student activity. I was a Formula Student competitor, and Bath had a good team.
In terms of work, I wasn’t sure where I wanted to go initially. But I decided to do a placement year at BP and I knew that I wanted to do engine design and development, because that’s what I find really interesting. During the placement I worked on engine testing of lubricants, which feeds into the job I have now: it touches the breadth of components in the engine. It touches different aspects of the engine system.
You’ve also worked with Formula One teams...
One of the highlights of my career is developing oil formulations for six cars on the Formula One grid. I can’t reveal the teams. I’ve also been to Le Mans and worked with the Audi team to develop an engine oil. Because of how long and important the race was, I was able to provide trackside support for Audi.
Improved engine oil can mean improved performance; more power, or more durability. There’s a lot of freedom in Formula One in terms of influencing formulation and the ability to test novel ideas.
I joined up the mathematical analysis of the components with the types of chemistries available to us. I faced a very real challenge to develop an oil that would increase performance without sacrificing durability.
Engines are changing. They are getting smaller, and manufacturers are turbocharging them to make them perform like much bigger engines. The challenge is to maintain driving performance while downsizing to reduce emissions of CO2 and other pollutants. BP is doing a lot of work to understand how turbocharging and downsizing affect the bearings in the engine. It’s developing very specific anti-wear lubricants for these kinds of engines. I work with manufacturers like Ford, developing fuel-efficient oils for engines of the future.