Graphene is the thinnest, strongest and most conductive material ever known. Its properties have excited scientists into a frenzy over its possibilities, from lightning-resistant aircraft to electronic devices that you can roll up and keep in your pocket.
A lattice of carbon bonded in a structure that resembles chicken wire, graphene was discovered in 2004 when two physicists, Professors Andre Geim and Konstantin Novoselov, used sticky tape to peel away layers of the natural mineral graphite. After repeatedly sticking the tape to a wafer of graphite and peeling it off, they were left with a sheet of the substance just one atom thick – graphene.
Although scientists had theorised about this form of carbon for decades, many thought it could not exist in nature. For their discovery, Geim and Novoselov won the Nobel Prize for Physics in 2010.
Even the government is now betting on graphene’s potential. On a visit to the prize-winning scientists at Manchester University last month, Chancellor George Osborne announced a £50 million investment to establish a global graphene research and technology hub in the UK to help the country capitalise on the breakthrough, creating jobs and cementing Britain’s position as a leader in the field.
One focus of the hub will be to develop the technology to manufacture graphene on a commercial scale – taking the material “from the British laboratory to the British factory floor . . . to get Britain making again”, says Osborne. The location of the hub has yet to be decided by the Engineering and Physical Sciences Research Council but may be spread over a number of sites. They could include existing centres of graphene research such as Cambridge, Exeter and Manchester.
Professor Dame Nancy Rothwell, president and vice-chancellor of the University of Manchester, is pleased by the government commitment. “Graphene is one of the most important scientific advancements in recent times,” she says. “It is extremely important that the government recognises the importance of investment in science as an economic driver.”
It all sounds pretty neat but graphene is not the first “new” form of carbon to be touted as revolutionary; it is the third allotrope of carbon to have emerged over the past 30 years. The first, called buckminsterfullerene, came to light in 1985 and also won its discoverers the Nobel Prize for Physics. Carbon nanotubes, which are essentially sheets of graphene rolled into a tube, took the limelight in the 1990s. But so far there has been limited commercialisation of these innovations.
So what makes graphene different? Simon Bending, of the Graphene Science Group at Bath and Exeter universities, says that the structure of the material makes it much more promising than the other forms of carbon that have been discovered. Engineers, scientists and researchers are scrambling to explore its potential uses in the energy, aerospace, electronics and medical sectors.
“Graphene is sheet-like and ‘two dimensional’, making it much easier to work with because you can make structures with a large area,” says Bending. “With nanotubes you can only make long, thin structures, and fullerenes are even harder to work with because they are very small in all directions.”
Peter Blake, a post-doctoral researcher at the University of Manchester, adds that chemical modification is more straightforward for graphene than for carbon nanotubes. This is because graphene is a sheet, so both surfaces of the material are accessible. With a nanotube, only the outer surface is available for chemical tinkering.
Blake adds that the hype about carbon nanotubes came too early but still believes there is scope for nanotube applications. One thing holding back the tiny tubes from commercial success is that they have been classified as a biohazard. Research has suggested that once airborne and inhaled, carbon nanotubes behave like asbestos fibres in the lungs of mice. Other findings have suggested that nanotubes may damage cells and because of these results there are now restrictions on how scientists can use them.
The same restrictions do not apply to those working with graphene although research in this area has been limited and many questions remain. Bending explains that graphene tends to stick to things in sheets and does not become airborne as carbon nanotubes can.
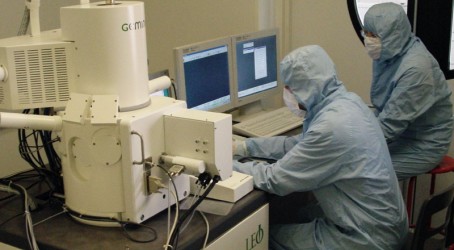
Several applications using graphene have already been realised. A US company is producing a graphene-based ink to print electricity-conducting circuitry. Another company is making ultra capacitors using graphene. The thinness of the material means that more energy can be stored in a smaller space although Bending says there are big challenges to overcome in this field.
He is also sure that the new wonder material will play a part in making solar power more applicable as it offers an affordable alternative to indium tin oxide, which is used in the transparent and conducting components of solar cells.
Graphene’s properties in this area have caught the imagination of several electronics industry giants, which are interested in graphene-based touch screens and flexible electronics. “Anywhere you want a transparent conductive coating, graphene can potentially help out,” says Blake.
But graphene’s conductivity can hinder as well as help when it comes to electronics applications. Its high conductivity means that electrons can always move around the material and transfer energy. Materials that are less conductive have something called a bandgap and exist in a state where the electrons cannot move around. Components such as transistors are difficult to make from material that has no bandgap.
The aerospace industry has also taken a shine to graphene. Its strength and the fact that it bonds well with polymers makes it a good material for composites. Graphene’s conductivity adds an advantage to composites because it can be used to ‘shield’ an aircraft that is struck by lightning by conducting the discharged electricity through the wings without damaging the aircraft. Graphene composites are at the prototype stage and Bending believes there is a lot of potential there.
Medical engineering has designs on graphene too. Early research at the University of Manchester has shown that it is a good chemical sensor. When a single molecule of gas is adsorbed on to the surface of the material the electrical resistance can change dramatically. The material could be tuned to sense a specific protein by attaching DNA strands that complement an antibody or antigen, according to Bending. Blake adds that graphene could also be used in medical imaging one day.
With all these potential applications the race is on to find ways to manufacture the material. Nanoplatelets of graphene are being produced on an industrial scale using an acid step and rapid heating. The process creates vast arrays of small pieces of graphene or thin graphite, which are used to make composites or ultra capacitors, explains Blake.
IBM and Samsung are also producing graphene. “Samsung is looking at transparent conductive coatings,” says Blake. In order to use graphene in coatings, the material needs to be manufactured into wafers, which is achieved by growing graphene on copper or nickel substrates.
This is done by chemical vapour deposition – a form of epitaxial growth where the atomic structure of the copper or nickel substrate acts as an anchor for the production of graphene.
To create graphene in this way, the metal substrate is heated up and exposed to methane and hydrogen gases. These gases decompose on the metal’s surface, with the hydrogen carried away to leave behind a layer of pure carbon. Bending says: “If you get the conditions right you are left with a single layer of graphene on the surface.”
But before anything electronic can be made with graphene produced in this way, the carbon layer needs to be floated off the metallic substrate and put on to something else, otherwise the device will short-circuit.
Non-electronic applications may be less fussy, explains Bending. “For many applications you probably don’t need to be sophisticated,” he says. “You can probably just take graphite and smash it up and break it into individual sheets.” This method may be perfectly good for the graphene used in photovoltaic cells or composites, he adds.
For now there is much work to do in fine-tuning manufacture and for the science to catch up with the imagination of researchers. But it will be a material to watch in the coming years.