Somewhere within Jaguar Land Rover’s principal technical centre at Gaydon in Warwickshire is a small team of engineers whose primary responsibility is to use computational fluid dynamics to simulate airflow over windscreen wipers.
This seemingly minor aspect of new model design and development actually has a rather big impact. The work undertaken helps JLR to reduce the noise contribution at frequencies most sensitive to the human ear, making for a much more pleasant passenger experience. And the accurate representation of acoustic performance enables the company to reduce the cost and weight of glazing thickness and sealing, making a small but valuable contribution to the overall vehicle efficiency.
This sort of simulation activity is repeated many times across almost every part of the car. Indeed, JLR says it carries out an astonishing 30,000 assessments to ensure that it has met around 9,000 requirements before a new model is signed off. And increasingly, it is virtual testing, rather than physical, that leads to the ultimate goal: a car that fully meets customer expectations.
Mark Stanton, vehicle engineering director, product development, at JLR is the company’s champion of virtual engineering activities. He says that as JLR’s business expands, and it looks to introduce cars into new sectors and markets, the pressure is on to come up with more “right first time” designs. That means creating many more digital models before clay models and prototypes.
“The emphasis is changing within the business,” he says. “We are not eliminating physical testing, but there is more and more virtual testing. We need to be able to analyse data and make quicker decisions. And that’s what the virtual world delivers. It helps to give us more robust, right-first-time designs.”
There are many other examples where virtual simulation has fed into new car development. A computer-aided engineering (CAE) method has been created to predict thermal cabin behaviour in terms of de-misting and de-frosting performance. Not too long ago, JLR engineers would have gone to Scandinavia, left a car outside overnight, and then gone along in the morning to carry out tests. “Then on-site climatic tunnels were used. Now much of this sort of work is done in the virtual world,” says Stanton.
The use of active damping on the new Range Rover was also tuned using virtual tools, enabling JLR to substantially improve the performance of that vehicle. Stanton says the company has been carrying out ride activities such as this for several years, but that virtual activity has allowed it to more accurately tune the control software within the active suspension system, thus further improving performance.
In body crash analysis, virtual simulation has enabled the company to optimise structures to deliver five-star EuroNCAP ratings. “We spend a lot of time and money building prototypes, and it saddens me to see many of them smashed into a wall,” he says. “We still have to do that for legal requirements. But we try to do much more in the virtual world, so that when we finally crash it we are more confident of the results.”
Additionally, within powertrain development, JLR has used virtual simulation to enhance water jacket coolant flow and optimise fuel injection, allowing it to improve efficiency results.
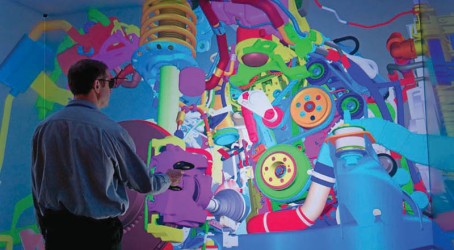
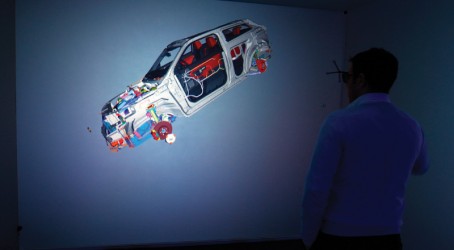
The growth in JLR’s use of virtual engineering systems and techniques means that it has to keep continually abreast of technological development, working out how it might feed into future application. The company wants to engage with tier-one companies to develop CAE use at a subsystem level, spreading value down the supply chain. But that brings complications in terms of systems compatibility.
Meanwhile, within the company’s own facilities, the implications of simulation and virtual engineering activities on the requirement for computer hardware have been huge. JLR has seen a fourfold increase in installed CPUs between 2010 and 2013. It now has 12,000 CPUs with 1 petabyte of storage space, so effective data extraction is vital.
Training is an issue, too. The number of JLR staff using CAE has risen from 200 in 2010 to 500 in 2013, plus 1,000 engineers using systems simulation. This expansion all requires management and the development of standards.
To cope with all these factors, and to give it a better idea of how simulation might feed into future activities, JLR is to play a leading role in a £10 million virtual engineering research programme, in conjunction with the Engineering and Physical Sciences Research Council (EPSRC) and four leading universities. The aim of the work is to put both JLR, and UK plc, at the forefront of virtual simulation tools and processes.
More specifically, the research is intended to improve the quality and capabilities of its simulation activities, from finite element analysis of individual component and subsystem design, through to whole-car visualisation.
The work will be split into two phases run over five years. JLR is providing £4 million of funding, which is matched by EPSRC, with a further £2 million from the partner universities. The five projects announced so far form the first phase and will make up 80% of the programme. These include: analysis of the vehicle as a complex system (Loughborough, Leeds); multi-physics and multi-functional simulation (Loughborough); driving simulation (Leeds); high-performance computing and simulation knowledge mining and abstraction (Cambridge); and visualisation and virtual experience (Warwick).
Dr Mark Claydon-Smith, the EPSRC point of contact for the project, says the combination of JLR and academics will deliver benefits. “From JLR’s point of view, it wants to produce better cars and bring them to market in a shorter timeframe. But as models become more complex, there is a limit to what can be achieved from physical testing. So these projects will build on JLR’s existing knowledge, improving its capability in the medium term.
“From the academic side, the research will focus on systems engineering and new design methods and tools. It’s the sort of work that is hard to do in a laboratory. JLR has been generous in opening up its practices to provide real-world problems and information.”
But where might it all lead?
Claydon-Smith says that one enticing area of advancement will be human-computer interaction. JLR already has impressive visualisation suites at Gaydon, whereby engineers can flip life-sized models upside down with the flick of a wrist or delve into the interior of the structure. The Leeds and Warwick research, in particular, could well lead to the development of even more realistic simulators for both engineers and end-users, says Claydon-Smith. “Virtual reality, and the way people interact with cars, is an exciting area,” he says. “We could expect to see advances here.”
That potential intrigues Bob Joyce, engineering director at JLR. He says that while the company already uses a wide range of tools and processes to design, engineer and test new vehicles, he can see a future where the technology will improve simulation. “We are keen to enhance the capability of virtual simulation and tailor it for driver and passenger experience,” he says.