It’s fair to say that there has been a certain level of scepticism about additive layer manufacturing (ALM). The idea of “printing” products by joining materials together, layer upon layer, rather than making them in more traditional subtractive manners such as milling, sounds such a radical and fantastical technology that it’s natural to harbour doubts.
But new figures show that the technology is being taken seriously by some significant players, especially in sectors such as aerospace, automotive and energy. The annual growth rate of ALM was 29.4% in 2011, with the industry expected to continue strong double-digit increases over the next several years.
The research, by independent consultancy Wohlers Associates, says that by 2015 the sales of ALM products and services will reach $3.7 billion worldwide, and by 2019 surpass $6.5 billion. Wohlers points out the extraordinary growth in the market for personal 3D printers – machines priced between $1,000 and $5,000.
These figures have made politicians in the US sit up and take notice. Last month, the Obama administration identified ALM as one of a handful of key technologies that could help to revitalise the stagnant US industrial base. So five agencies – the Departments of Defense, Energy and Commerce and the National Science Foundation and Nasa – have jointly committed to invest $45 million in a pilot research institute. The National Additive Manufacturing Innovation Institute, in Ohio, will look to centralise US expertise in 3D printing and attract investment from other countries.
Tom Kurfess, assistant director of advanced manufacturing at the White House Office of Science and Technology Policy, is a believer, saying that ALM is a technology whose time has finally come. Speaking last month in front of an audience of almost 4,000 scientists and engineers at National Instruments’ annual get-together in Austin, Texas, Kurfess said: “People have been thinking about ALM for many years. But now the technology is coming to fruition and we are getting all sorts of new materials. It is allowing us to move forward in interesting ways. This really is coming.”
So how does ALM work and where exactly is it being used? The technology uses thin, horizontal cross-sections from computer-aided design models and 3D-scanning systems to build up parts that can be difficult or impossible to produce any other way. It is primarily used to make physical models, prototypes, patterns, tooling components and production parts in plastic, metal and composite materials.
Wohlers Associates says that the technology has the potential to change the way organisations design and manufacture products. When used correctly, it can save impressive amounts of time and money. Some companies maintain that it has helped trim months off of design, prototyping and manufacturing schedules, while avoiding costly errors and enhancing product quality.
Kurfess, a mechanical engineer who graduated from the Massachusetts Institute of Technology and who has significant experience in high-precision manufacturing and metrology systems, thinks ALM will even enable the making of parts that would prove impossible with current production techniques. “We can start at the bottom of a part with steel and then functionally grade the material into aluminium at the top,” he says. “None of our existing computer-aided design systems allows us to functionally grade material. Yes, we can stack aluminium on top of steel, but we cannot do functional grading.”
Kurfess also believes that ALM will enable engineers to engage with CAD tools more effectively, particularly in the area of topological optimisation. “We can let mathematics decide where to locate material,” he says. “We can let the CAD system do the optimisation. The problem at the moment is, if you let the CAD optimise for weight, you may not actually be able to make the component. But with layered manufacturing, you can do it.”
Kurfess thinks the US is uniquely placed to exploit the potential of ALM, because it is home to the vast majority of existing machines – around 72% of all ALM machines are there.
He thinks that engineers will embrace ALM because it can make parts far more quickly than traditional prototyping technologies. “Pretty soon, we could even be using this sort of technology to make hard tooling,” he says.
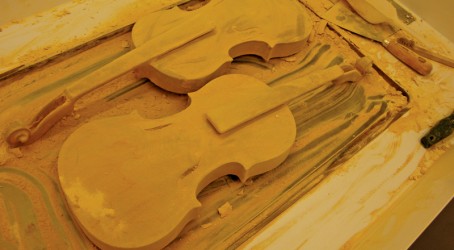
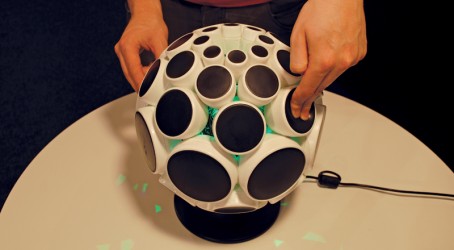
There are other reasons why the US is investing so heavily in the technology. The inherent nature of the ALM process – where it is possible to see metal and plastic products slowly coming to life – means it can be used to wow young people, who often view the sector in a negative light. Indeed, many schools and colleges have already invested in 3D printing machines to enthuse students.
Kurfess thinks this educational aspect is an important bonus. “There’s something special about hardware – about designing and making it. We want to see kids excited about making things. We see a lot of high schools, community colleges and universities moving into this. It’s already engaging their students,” he says.
Looking to the future, Kurfess says one of the most exciting aspects of ALM is that no one knows what the shape of the market for the technology might look like. If 3D printing machines continue to come down in price, then it’s possible that most homes could have one. Otherwise, a whole industry catering for the production of printed parts might emerge.
He says: “Maybe you might send off the CAD file to a local hardware store. It’s like photos – you can produce your own pictures, but often you take them to a local store to have them printed out.
“Life is changing, and technology is changing. Economic models are changing, too. We need to keep up with things.”
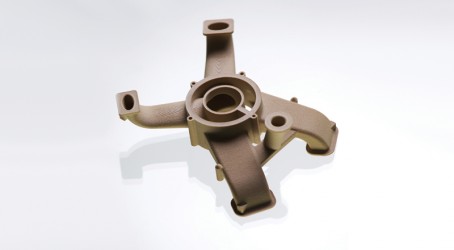
Exeter University and EADS team up on high-flying applications
Academics at the Centre for Additive Layer Manufacturing at Exeter University are working with engineers from EADS to find aerospace and defence applications for ALM technology.
The collaboration is expected to lead to the creation of parts for future aircraft programmes. Sara Flint, manager of the centre, says: “This isn’t pie-in-the-sky research. What we are doing is application-driven engineering that is going to be used in aeroplanes.”
EADS thinks the real advantage of the technology is its potential to make products that cannot be manufactured in any other way. Alongside that, it means parts can be built quickly without lots of tools, so products can get to market faster. In aerospace, it allows the redesign of products to use less material, to take weight out, and therefore use less fuel.
Jon Meyer, research team leader in metallic technologies for EADS’ Innovation Works, says: “The beauty of the process is that we can build incredibly complex parts that you couldn’t build from a conventional subtractive process, such as machining. At the Centre for Additive Layer Manufacturing, we are working with high-temperature polymer material, where the conventional processing would be injection moulding. That had limitations in terms of the geometry we could build. There are opportunities here to realise new products through the development of ALM technology.”
Meyer says he is certain the technology will be widely adopted in the aerospace sector. “It gives great capability in terms of geometric freedom. There is a potential to reduce waste – that’s of particular interest on high-value metallic parts, where today a large proportion of the cost is in material that is subsequently removed by machining.”
He also thinks the technology has great potential for customisation. “You can make multiple parts in the same build chamber that all have subtle differences. That has potential for cabin customisation, for example, meeting specific customer requirements. It gives us the ability to meet those requirements in a much more flexible manner than we can today with conventional tooling approaches.”
However, there are limitations, particularly in the area of parts size, he says. “This is partly linked to the maturity of the technology but also to the viability from a production point of view, specifically the rate of production. I think in the future we will see ALM becoming a higher-rate production technology with larger-size platforms. That’s a key research topic: enabling scale-up of the technology.”