Articles
The Fly-Bag features multiple layers of novel fabrics, composites and coatings. It is designed to be filled with passenger luggage and then placed in the hold of a plane. If a bomb in the luggage exploded during the flight, the bag's complex fabric structure is designed to absorb the blast, preventing damage to the plane.
Fundamental to the design of the bag is the internal elastomeric coating and impregnation of fabric with Shear Thickening Fluids (STFs). Elastomers are very low-stiffness, high-failure strain materials, often used as adhesives, sealants or in structures where high strains are expected. An elastomer was developed to provide a gas seal in the bag at very high strain rates and very high deformations, while resisting flame and heat.
STFs work by increasing in viscosity in response to impact. A simple STF can be made from mixing cornflour with water. Providing quantities are correct, it would be possible to roll this simple STF into a ball that will bounce on hard surfaces but return to a fluid once it is left alone.
Under normal circumstances, the particles in STFs repel each other slightly. However, following sudden impact, the extra energy in the system proves stronger than the repulsive forces, causing the particles to clump together in structures called hydroclusters. These hydroclusters bump into each other, consequently thickening the fluid.
This unusual behaviour of STFs has already generated significant commercial interest. They are being considered to improve body armour designed to protect the wearer from weapons such as knives and bullets.
In the case of the Fly-Bag, the STF is coated onto the yarn of the fabric. As the fabric comes under strain, shearing forces between the yarns cause the STF to thicken, temporarily increasing the stiffness of the fabric, reducing the total deformation.
Team member Dr Jim Warren, from the University of Sheffield’s department of civil and structural engineering, said: “The use of explosives on aircraft has had a renaissance in recent years, with recent attempted attacks coming not just from passengers, but also as loaded freight.
“Since weight and operational flexibility is key for aircraft operators, this low-weight, removable solution would seem to be a paradigm shift in the hardening of aircraft structures.”
The University of Sheffield is working with spin-out company Blastech to commercialise the Fly-Bag. It is expected to be on the market within two years.
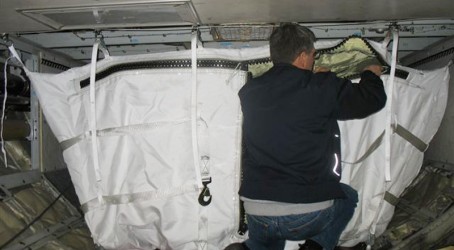