Please introduce your university and team!
Kieran Shopland, Project Manager: Originating from the University of Bath, we are still a relatively new team to the competition. Having participated in the competition for the first time in 2016, we are now building our fourth generation electric vehicle. The past four years have seen the team improve rapidly, while maintaining the title of top UK electric team, something we are immensely proud of. Throughout these years of improvement, we have stuck with the electric powertrain, more specifically the EMRAX 228 for 3 of the 4 cars. The electric powertrain has the obvious advantage of the instant torque, but the disadvantage of the large battery needed to power the motor. This is something we have focussed on consistently and now believe we are getting to a good place with the design. The progression the team has shown is largely due to the significant increase in numbers the team has seen, from an originating team of no more than 10 members, the team now has upwards of 60 members. This is in part due to the fantastic support from the University, giving us our fantastic build room and academic support but also in allowing us to put some of our degree towards the project.
2019 brings a whole host of changes to the cars, whilst maintaining the single motor rear wheel drive powertrain. This year brings the first major implementation of composites on the car, with a front end carbon fibre monocoque chassis and a composite accumulator box. We are also upgrading all of our suspension systems and taking our first ever look at aerodynamics. All whilst maintaining the reliability of our electrical systems.
How did you get on at the competition last year?
Afkar Ansar, Business Manager: We were extremely pleased with our performance last year. We came 17th overall in Class 1, an improvement of over 20 positions but more importantly we were the able to compete in all the dynamic events which was one of our main goals last year.
Our cohort (Class 2) were happy with our experience as well! We had come to the Class 2 competition knowing TBRe had placed 2nd in the previous year. We felt the pressure to do well but we also had the guidance from the year above which we felt was crucial in winning the Class 2 competition.
The pressure is on us again now as TBRe Class 1, which we welcome, to continue the upward trajectory in performance the team has seen in the past 4 years. We want to build on the great success the previous TBRe teams have achieved and look to compete with the best teams at the competition!
What’s your reaction as one of the top EV teams in the UK and the only team that represented the UK in China last year?
Kieran: We are incredibly proud to be the top UK electric team, we have enjoyed a few years of success however we are all well aware that we need to keep pushing as more and more teams look to shift to electric Powertrains. We have worked to make sure that we thoroughly understand every part of the electrical systems on board, not just the high voltage powertrain systems, but also all of our low voltage systems that ensure the car is safe to operate.
It was insightful to take the 2018 car to the competition in China and we are extremely grateful to the University and SAIC Motor UK Technical Centre for making this happen. This competition was eye opening, both in the alternate way that their designs came together but also in the home teams’ positive views on our designs. We learnt a lot form the competition and now want to branch out to other international completions, particularly in Europe.
We saw your team at Learn to Win in November, how did you get on?
Kieran: Learn to Win was a fantastic event, the opportunity presented to have all of the teams and judges present in the same area at the same time really helped us to finalise our thoughts on some of our designs and ensure that our designs were feasible. It was also great to be chosen to demonstrate our accumulator at the event. This prompted a lot of great conversations with other teams, not just about the design but also different team’s thoughts and ambitions for the coming season.
Equally it was interesting to hear more about the AI part of the competition. With our own hopes to create an autonomous car for the competition, it was great to hear others thoughts on this and see how we can help each other.
What are your objectives for the 2019 competition?
Afkar: The last few years our philosophy has revolved around reliability, meaning we ensure our designs will produce what is expected. We are now confident we have the knowledge base to shift our philosophy. We are focussing more on performance and innovation, by creating designs that are less conventional but result in greater performance benefits.
The change in design philosophy has brought about more ambitious goals for the year, some of which are listed below:
- Finish within the Top 10 in Class 1
- Acceleration time below 4.4 s
- Reduce overall mass by 40 kg (TBRe 2018 – 254 kg)
- Retain top UK electric EV
We have three key areas of improvement for TBRe2019. Firstly, a transition from spaceframe to a carbon fibre hybrid monocoque. Secondly, to optimise the vehicle dynamics by utilising the increased number of mechanical engineers within the team, and finally to optimise the accumulator to remove roughly 25 kg of mass. All three mentioned above are in progress and we are excited to deliver on our targets.
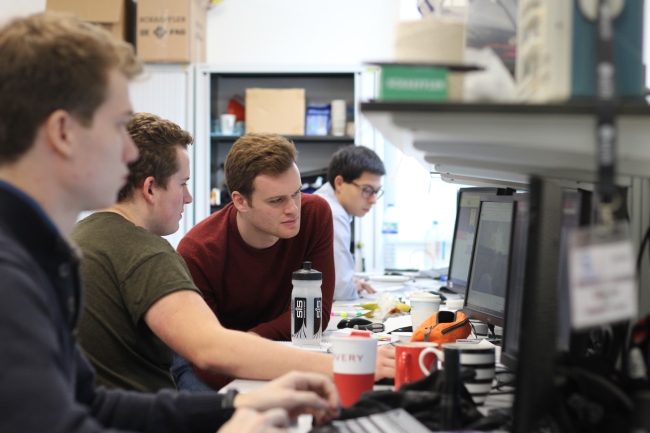
How does your team organise your workload?
Kieran: In line with the structure of the team, the work is divided up into the six different sub teams (Accumulator, Chassis, Vehicle Dynamics, Aerodynamics, Powertrain and Low Voltage Systems). The scopes of work for each of these has been clearly defined and each know the dependencies on each other which helps with the organisation of the workload.
We started off the year with an overall goal for the team, that’s was to ensure we had the car running under its own power prior to our launch at the end of May. We are roughly on track to meet this, and are currently operating on a Short Term Plan mechanism to ensure we are completing the work we need to. This is so far proving to be effective by having shorter term goals to focus on each week and is something we plan to continue up to launch.
On top of this, we are keen to make sure the team has the right environment to work in to make work more enjoyable and thus more efficient. This involves having a happy, friendly culture in the lab where everyone knows the importance of the part they play. This is aided by our use of Microsoft Teams as a way to communicate amongst the team and helps us keep things in one place. But more than anything else, we achieve our goals each year through the incredible hard work of each of the team members.
What is new and exciting for your team this year?
Afkar and Kieran: A lot has changed with the team this year, not only with the design but in all other aspects of the team. For example, we have reached out to other departments such as Business and Computer Science to gain their input on the car. These disciplines have helped us with our newsletter, cost work and our initial endeavours into the autonomous part of the competition.
We have also seen a growth in our sponsor network this year with a variety of new partnerships including, but not limited to, Solvay for our composite materials, Newbury innovation for our PCB manufacture and Creat3D for our printed Sub pack housing. This is in addition to the continued support from most of our valued sponsorships.
Looking more at the design of the car, the 2019 vehicle brings a host of advances in design. Firstly, we are now well into the manufacturing stage of our front carbon fibre monocoque, with the outer skin having recently come out of the autoclave. In the next couple of weeks, assembly of our optimised 3D printed sub packs will also begin, with the enviable task of hand welding over 700 cells to make our 6 packs. This is not the only change in the accumulator though, with the manufacture of the composite box also soon to start. All of our electrical systems are well into manufacture with more PSB’s being sent off for manufacture every week. All of this is heading towards the real start of assembly in mid to late April ready for a completed car in mid May. Although there is a lot of work still to do, we are confident we will meet our goal.
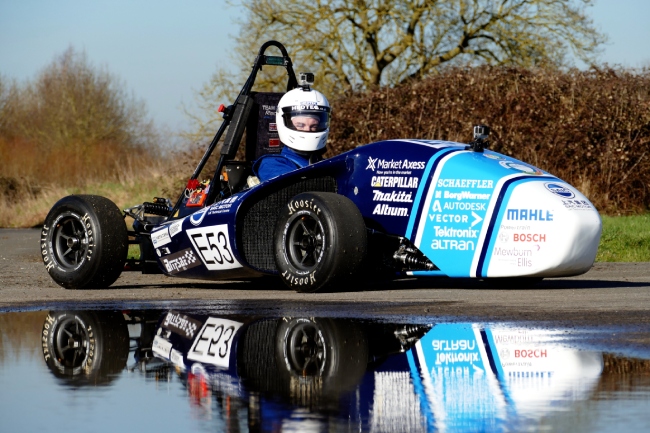
What have been your biggest challenges so far how have you overcome them?
Kieran: The steepest learning curve for the team this year has been in the implementation of the carbon fibre monocoque. This has not only been in terms of the associated manufacturing process, but also in terms of the impact to each of our subsystems and how they integrate into the chassis. There has been a real onus on communication to ensure we are all clear on packaging requirements and insert locations before laying the final part.
The second challenge is one we have continually faced, and that is of electrical integration in the car. This is something we have worked hard on over the past few years. We have tried to mitigate any further issues this year with a comprehensive electrical architecture devised earlier in the year and consideration of the potential electrical issues involved with each design decision. A great example is in the application of composites into the accumulator, we have had to ensure that this is both electrically isolated as well as being grounded. Something we now believe we have a solution to.
What made you join Formula Student?
Afkar: Participating in Team Bath Racing Electric is an option within our degrees in our third year. This opportunity usually forms the basis of the Class 2 team. I initially joined TBRe as I geth the opportunity get to work with high calibre and motivated students. As I got more engrained within the team, I realised the extent of the opportunity Formula Student provided.
One of the main reasons why I continued Formula Student into Class 1 is to experience the start-up business and team culture exhibited by our team. We are only four years old, and the way we run this project is comparable to start up business. The challenges in managing people, finding funding and delivering on deadlines are all similar to a start-up and the experience is invaluable. All the challenges are real yet there is a safety net knowing it is at the end of the day a student project. Being able to manage TBRe duties on top of our studies will only better prepare us for the evolving and ever challenging job market.
What’s your proudest moment at Formula Student?
Afkar: Our proudest moment was at the end of the competition going up to collect our trophy as the overall winners of the Class 2 competition. Leading up to the competition, we had all put in many hours of work and to achieve this target. However, as we have no precedence to lean on, we did not know if our efforts were an effective use of our time.
Although we came first last year, the top three teams were separated by a handful of points. We have fond memories of keeping count on our cumulative score as each score came in, to know where we stood. Finally, the sense of relief as the business scores came in and we found out we had won by a few points is comparable to none.
What advice would you give for fellow teams?
Kieran: As more and more teams look at how to venture into the design of an electric vehicle, we have received many questions on how to go about achieving a good design. We are extremely proud to be viewed so highly in the competition and are happy to help any teams where we can. The key points we would raise are around the low voltage systems and the accumulator. In short, make sure they get the attention they deserve. These systems take a significant time to design, and an even greater time to get working correctly, be sure to build in significant testing time for these parts. Secondly, in the design phase, start simple, we find it hard enough to debug the car without making the circuits unduly complex. We tend to find that although all of these components work on test benches and may even work well when integrated on a bench, there will almost certainly be issues when they are packaged into the car in close proximity. To aid with this, pay special attention to the packaging of the electrical systems in the car, especially with the separate AC and DC circuits, should you be using any AC components.
How can we keep up to date with you?
Afkar: There are several avenues that can be used to keep up with our team and our endeavours!
Starting with our website, where we feature monthly newsletters with updates of Sponsors, team members and the development on the car.
We are also very active on social media, give us a follow on the following:
Facebook: @teambathracingelectric
Instagram: @teambathracingelectric
Twitter: @TeamBathRacingE
LinkedIn: @TeamBathRacingElectric
Finally, no rivals to call out however we would like to say good luck to some of the other teams that have messaged us with questions, we are more than happy to help where possible. We want to build a collaborative culture amongst EV teams to ensure the best possible electric cars attend the competition as we believe great competition results in greater innovation.
Thanks so much to Kieran, Afkar and the team for their detailed interview and we look forward to watching them out on track this Summer!