Paul Newsome MIMechE has been promoted to the position of Chief Technical Officer (CTO) for Williams Advanced Engineering: the division of Williams that adapts Formula One based technologies for a range of commercial applications.
The Chartered Engineer has previously worked at the BMW Group as Platform Director, Jaguar Land Rover where he was Group Chief Engineer for advanced product creation and research, and Lotus where he was Director of Engineering. He joined Williams in January 2011 as Head of High Performance Vehicles, where he was responsible for the team that designed and built in conjunction with Jaguar Land Rover the C-X75 hybrid supercar – a vehicle which uniquely brought together the collective engineering expertise of several Institution Members and Fellows from various companies.
Paul oversees a team of 80 specialist engineers and technicians. The company is currently building a brand new facility at Williams’ headquarters at Grove in Oxfordshire which, after the major recruitment campaign which is just about to be launched, will house a highly skilled workforce of 150 engineering professionals, and an increased manufacturing capability. In his role as CTO, he has overall technical, operational and delivery responsibility for all projects within Williams Advanced Engineering. This includes the design and manufacture of high performance road and race vehicles in addition to the company’s development of flywheel and battery based energy storage systems.
In this exclusive interview for the Institution, Paul gave an insight into the key areas of technological adaptation from Formula One, what inspires him in his daily working life, and why professional registration is increasingly important for his engineers and technicians.
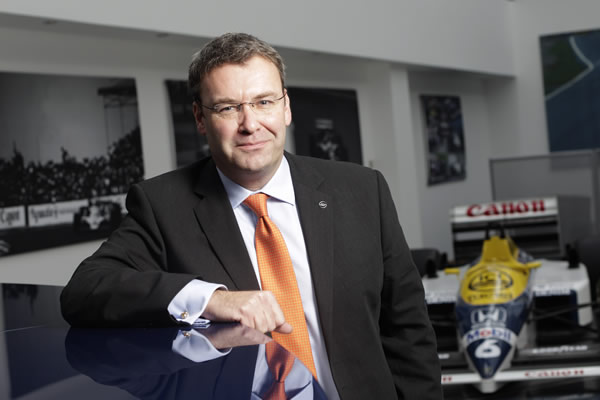
Williams Advanced Engineering’s technological expertise
Williams Advanced Engineering has only been in existence for three full years, but in that time, it has garnered an enviable track record in taking technology developed for Formula One and successfully adapting it or making it accessible to other business areas – some immediately complementary to motorsport, others which have perhaps required more of a leap of imagination.
Paul described the five key areas of technological adaptation: “The first is hybrid propulsion systems which are an important part of Formula One since the introduction of KERS (Kinetic Energy Recovery System) in 2009. Williams has developed specialist expertise in the design and manufacture of motors, invertors, and energy storage systems, and we’ve done it at the highest level of power output relative to the mass of the system to achieve the sort of results you’re looking for in the harsh environment of Formula One. We’ve delivered that in Formula One and the technology does have a significant application in other areas.”
“The second area is aerodynamics. Formula One teams have aerodynamic capacity in terms of technical advancement, wind tunnels, computational fluid dynamics (CFD) that is way beyond any other industry. This gives us a capability that we can apply to other areas particularly given the level of detail that we go to.”
“The third area is lightweight structures. F1 cars are famously lightweight. They are mostly made of very exotic materials that aren’t always accessible to other areas but we use materials which are becoming increasingly more available in quantity and at lower costs to the rest of the world now. Obviously, we’ve been working with carbon fibre structures and low mass metallics for a very long period of time and have a very good understanding of the properties: how to use them, form them, how to simulate them in terms of analysis, and then deploy them in a variety of different ways. We also have our own in-house manufacturing capability in all of those materials as well so we can work from raw materials to small numbers of parts very, very quickly.”
“The fourth area is driving dynamics. Obviously an F1 car operates at the absolute extremes of performance levels in terms of driving dynamics and in the methods that we use and the simulations that we have available to us, and we’re able to offer that capability to other lower race series as well as to products being used on the roads.”
The fifth area is interesting because it isn’t really a technology at all. Paul said: “We are specialists in low volume operations, so areas such as the procurement and manufacturing, and this allows us to rapidly produce highly specialised products in very small numbers. In F1, it’s typical to build two to three cars per year, which to a mass manufacturer is absolutely nothing, but you produce a new car every single year and to have the capability to do that reliably and to a high standard is a skillset that makes us stand out. The cycle time through that activity is very, very quick indeed. So, this can be translated easily into prototype quantities for mass manufacturers and we’re optimised to deliver against those numbers.”
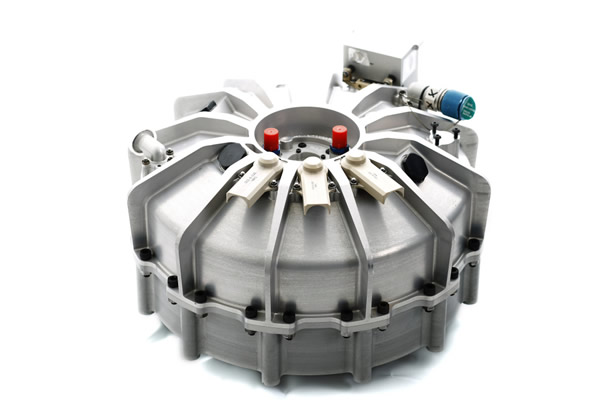
From pit stop to bus stop: adapting Formula One technology
Currently Williams Advanced Engineering focuses largely on adapting technology within two areas of business activity: motorsport in general, and the new FIA Formula E electric racing series. Williams also has another arm of its business, Williams Hybrid Power, which is focusing its attention solely on flywheel energy storage systems and the company is enjoying success in bringing this technology to endurance racing. As Paul explained: “Obviously what we learn in Formula One has applications in other forms of motorsport. Williams Hybrid Power, which is also based at the Williams factory in Grove alongside Williams Advanced Engineering, supply the flywheel energy storage system that has been used on the Audi R18 e-tron Le Mans car which won Le Mans this year and last year. That flywheel technology was initially developed for Williams’ 2009 Formula One car and it was the potential of this technology beyond the sport that kick started Williams’ diversification into new areas.
“Recently, Williams Advanced Engineering has been awarded the contract for the supply of all of the batteries for Formula E. We are using the same technology that we’ve developed for our Formula One KERS battery systems as the basis for the battery design for Formula E. In this electric racing series, the cars are 100% electric, so, unlike in F1, there is no engine to rely on as well, which means that the battery is significantly larger than the one used on an F1 car where the electric motor is supplying supplementary power.”
“The first race is in September 2014 and we’re contracted to supply all of the batteries to the grid. It’s a common battery specification for all of the vehicles at the start of the season, and we’re at the design stage of producing the batteries for that product. Approximately 40 batteries will be required for the start of the season.”
“Everything we’ve used to maximise the efficiency of the usage of a battery cell and their operation in the world of Formula One we’ve been able to apply across to Formula E.”
Naturally, motorsport is an obvious area in which to adapt technology: it’s the field that Williams is known for and has been in for a significant period of time. However, moving beyond that, high performance or high efficiency road cars is one of the next and most obvious areas of application for Williams.
Indeed, one of the products which has given Paul a great sense of personal pride, is the C-X75 hybrid supercar. Williams Advanced Engineering worked with Jaguar to design and develop the car which has utilised Formula One based technology in a number of areas. Paul said: “Most of the adaptive technologies which Williams specialises in were used on this car: the hybrid systems, the lightweight materials, the aerodynamics, the singulation techniques; we also used our manufacturing operation, because the prototype cars were built here at Grove. All of that has been fed into that programme. It is a very exotic road car, it’s not an everyday family vehicle, but it does demonstrate how far you can take a car using that technology. It is probably the most technologically advanced road car in the world today and it delivers a unique set of performance and environmental targets.”
Beyond this, Williams is moving into ever wider and perhaps, on the face of it, unexpected industry sectors which are benefiting from applications of technology. Paul said: “Williams Hybrid Power are currently working on taking the flywheel technology - which started in a Formula One car, then moved to endurance racing - into public transport systems. The company has developed prototypes and are moving forward to production now with the use of the flywheel energy storage on buses and trams.”
“The great thing about buses is that they have a very consistent stop-start drive cycle which allows you to regenerate and then re-use the energy which you have just collected or harvested, very repeatably and very reliably. The flywheel energy storage system lends itself very well to that predictable cycle. It’s a nice example of a piece of technology moving from a Formula One car to an everyday vehicle in less than four years – demonstrating the growing relevance of our technologies to the wider world.”
“There is more common ground than you might think though between Formula One engineers and bus operators. In simple terms, a Formula One engineer is looking for efficiency in the same way that a bus operator is looking for fuel consumption reductions – it’s actually the same target. The money available to be spent on the subject is different in the two fields but actually the engineering solution doesn’t have to be. Motorsport and road cars are probably the first places where people would recognise that we can apply our Formula One technology, but we can go way beyond that.” Williams Advanced Engineering is following Williams Hybrid Power by moving into the public transport arena, developing at its Technology Centre in Qatar more powerful versions of the Williams Hybrid Power flywheel that can be used in metro systems.
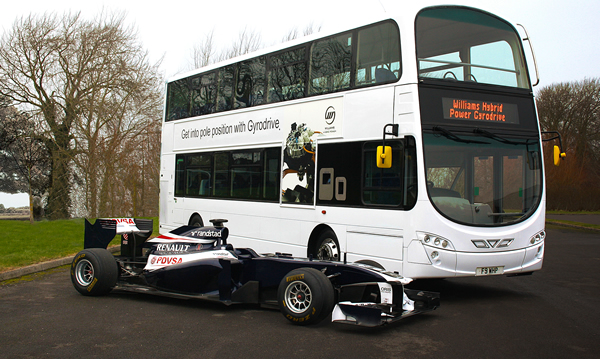
No such thing as a typical working day
Perhaps predictably working in an industry sector renowned for its intense creativity, innovation and dynamism, a typical working day doesn’t exist in Paul’s life. Paul smiled as he explained: “The only way I can really give you an insight into what I do is just to tell you about my day yesterday. I couldn’t really describe it as a typical day, it was just a day!”
“I spent the day at Grove, which is Williams’ main site. The majority of the advanced engineering team are located here, alongside the Formula One team. At 8.30am, I joined a start the day build meeting. We have a vehicle project - one of many in our workshop at the moment. When the vehicles are going through their build phase - this is a prototype technology demonstration vehicle – we hold a start the day meeting on a daily basis: it brings together the engineers and the technicians, the procurement team and anybody else who is supporting the activity to go through whatever is supporting that day’s activity.”
“The meetings are relatively quick –about 20 minutes. It’s all about getting to the nub of the issues that we’re facing. The meetings are run by the manufacturing leader for that particular project and he effectively has the support of the rest of the team so that he can deliver on his plan to build the car in that time.”
“We have some very skilled technicians at Williams Advanced Engineering. The vast majority of them have spent time as Formula One technicians. They contribute significantly to the design of the products we work on. They don’t just build what they’re given – they are a key part of the design process and we wouldn’t be the same place if we didn’t have this standard of technician supporting our activity.” It’s quite hard to tell the difference between a qualified engineer and a technician in our group. Our technicians have good CAD skills as well as the ability to put vehicles together and we encourage that activity to work together. Fundamentally the principle of technicians contributing significantly to how a vehicle should be designed is important, and it’s a nice activity to see.”
After a project review on the Formula E battery supply project, Paul had a conference call with Williams Advanced Engineering’s team in Qatar to go through its programme of work, in particular its focus on adapting Formula One based simulation technology. He said: “We are working on a road safety programme in Qatar whereby we borrow Formula One simulator technology to produce fully immersive road safety simulators that train and certify drivers in a realistic and safe environment.”
“Safety is another pillar of Williams Advanced Engineering’s portfolio. Williams’ Founder and Team Principal Sir Frank Williams has always been a strong voice on the subject of safety and has always pushed us in this particular direction. Qatar has a poor road safety record and we are working with local organisations to use our simulator technology to cut the number of accidents on the country’s roads.”
The Williams Advanced Engineering business is growing, and straight after lunch, Paul had a meeting with the marketing team and HR Director to agree plans for advertising to support a major recruitment campaign, which ultimately will see Paul’s team double in size.
He said: “Williams Advanced Engineering is about three years old now. We’ve grown year on year during that period, and we are again in a position where we need more good engineers in particular to support our growth. We are very much a hands on engineering business: the number of people who work here who are not either an engineer or a technician is a handful. We are expanding and we have secured high profile and interesting work by collaborating on projects with Jaguar Land Rover, our work with Formula E, and more recently the relationship we have formed with Nismo, the motorsport arm of Nissan”
“We have a number of engineering places that we are looking to fill over the short and medium term to expand the group. We don’t ever expect to be a huge organisation. We are operating at quite an extreme level of technology – we don’t expect to become a large consultancy group. We want to be very specific about what we offer. So, at the moment, we are about 80 people in Williams Advanced Engineering out of approximately 660 in the whole of Williams. We plan over the next 12-18 months to grow that to approximately 150, which is nearly double, so we have a significant number of roles that we need to fill.”
At the end of his day, Paul took the opportunity to check up on progress on the new facility that is currently under construction at the Grove site that will house all of the Williams Advanced Engineering people, capability, manufacturing facility. Paul said: “The building is due to be ready in December this year, and it’s on plan. It’s a significant facility, and it will house the expanded workforce, but more importantly it will provide us with the manufacturing capability to build small numbers of vehicles from this point in, because again our speciality is making small numbers, typically less than 100 per year.”
“We specialise in relatively small numbers of vehicles which can translate into the quantities of vehicles needed for a race series, or it can be the quantity for a prototype build for a production vehicle – not, obviously, the production number - or, in extreme cases, it could be a very limited run production product. We have no intention of competing with the likes of Magna and Valmet and producing large numbers of cars. We plan to continue to specialise in this particular area.”
What inspires an ultimate innovator?
Asked if the fact that no two days are ever the same is an aspect of the job which appeals to him, Paul smiled and said: “Yes, absolutely. We are a consultancy business, if you lift it to the highest level. It’s very specific in terms of what we do and the type of business that we are part of. But it does mean that although the technology we develop in Formula One sets us off in a certain direction, we never really know what the next significant project or programme is going to be. For me, that’s one of the most exciting things about it but to some people, it’s unsettling. It does depend on the individual and the character.”
He continued: “This may sound a little unusual, but actually, the aspect of engineering that I appreciate the most and which I find the most inspiring is the simple, elegant solution. There are many, many ways of achieving a result. It’s always the one which is done with the simple methodology. I’m still firmly of the belief that in engineering terms, if it looks right to an engineer, then it is a long way to being right. Having said that, I live in the modern world and my expectation is that we don’t release a design without conducting analysis of it or taking the opportunity to optimise it and so on.”
“But even so, it always surprises me and inspires me that when you get to the end of the day, the designs or ideas that survive all that analysis best are the simple solutions: the ones with less moving parts, with less component parts to them, often the most cost effective as well. And it doesn’t always take a long list of technologies and a sledge hammer to achieve the target. By far the best result is the simplest one.”
“As an aside, I often find engineers make the best inputs to new products when they are given a significant number of constraints – some of the greatest ideas have come out of constraint rather than blue sky. The more constraints you throw at them, the more they have a better opportunity to perform. It’s important they get the opportunity to understand what we’re trying to achieve and then how they can best support it.”
“I enjoy the times I spend with my engineers in front of CAD screens reviewing products and in the workshop with technicians – that’s by far the best part of my working day and I think it’s where I add as much value as it’s possible for me to add to the activity. I do spend time in business meetings, I travel around visiting customers and talk to them about what we can do, but at the end of the day, we are here to make a technological advancement in product and to deliver the best answer, and that is what inspires me most. This is the bit that makes the difference.”
He added: “I was very, very proud of the press response that we had to showing journalists the C-X75 product and it seems to have been extremely well received by the journalists whom we allowed to drive car and it’s a great feeling. But it’s normally something like three years from the start of that project to that point occurring so it’s not what drives you to come in and do the job on a daily basis. It’s more about delivering that engineering solution and I still think that that the simplest most elegant solution is the one that is the most inspiring.”
Encouraging and supporting international professional excellence
Paul believes firmly that the reputation for British engineering is something that has improved in recent years from a lower point that it was in previously. He explained: “I feel that many of the things which have occurred over this century in particular, have made a huge difference to how people see engineering in Britain.
“The team we have is extremely multicultural and we have people from Brazil, Iran, France, Italy, Germany, Canada, US, and India. The list is very significant. It is a diverse and very inspiring environment to work in. The point is, they’ve all come to Britain to do this and they’ve come because the opportunity is here to do it and the drive is here to deliver engineering at the highest level and the environment to do that is better now than it has been for a long time in terms of the investment in engineering taking place in this country. I think it’s fabulous that we can be in a position to inspire people to travel half way round the world to come to Britain to work on engineering projects, because I don’t think it was like that 15 years ago.”
“Motorsport engineering is at an absolute pinnacle in the UK. We lead the world. 8 of the 11 Formula One teams are located in this country and most of them are very close to where I’m sitting now in Oxfordshire. Automotive engineering has definitely seen significantly improved investment in this country. What’s being achieved is fantastic now – it really is. I’m proud to be a British engineer.”
Paul is a Chartered Engineer and Corporate Member of the Institution of Mechanical Engineers. Having worked in both motorsport and the wider automotive engineering sector, he is uniquely placed to consider his industry’s perception of the value of professional registration.
He said: “Does the motorsport industry now value professional registration more? I believe so. Motorsport does still lag behind other areas of engineering in this country in terms of professional registration, but it has taken on a higher relevance as has the value of support from the Institution to an individual’s career.”
“I guess there are two reasons for this: first, motorsport is opening up significantly now, and becoming bigger and bigger. Secondly, we are seeing significantly greater movement of engineers between motorsport and other engineering or industry disciplines and that’s had a significant effect because people recognise the achievement of chartership as a fundamental recognition of what they are capable of.”
“I have engineers whose histories are in all sorts of different areas: aeronautical, composites, electronics, IT, all sorts of other areas. And in that world, people feel a much stronger desire to have a professional recognition of their qualifications and capability and also to have the support of the Institution, too.”
“From my point of view, I’ve been a member of the Institution ever since I was a student reading mechanical engineering at Sheffield University. I joined Austin Rover Group and then went through the Monitored Professional Development Scheme (MPDS) which took me through to Chartered status probably as easily and quickly as it was possible to do, which was a fantastic opportunity for me to do.”
“MPDS provides a consistency of approach which I think is fantastic. I think it’s important not just for graduate engineers, but for people who have come through different methods of achieving their technical capability, for example technicians. It’s moving into the motorsport and automotive industry slower than other industries, but I do see that change taking place, and it does matter to people.”
“We don’t demand it that people achieve professional registration, but I do encourage it. The thing that I have to recognise is that not only do I have a group of engineers who are having to deliver pieces of engineering work, but also I’m also selling an engineering capability to an outside world and the recognition of the status of the people working in the business is a hugely important part of that so I think it adds to the credibility of the business, so I encourage people to do it, and for many, they recognise the advantage of it.”
For information about Williams Advanced Engineering recruitment campaign, please visit: http://www.williamsf1.com/Careers/