It is said to be the largest nuclear project of its type in the UK. The Evaporator D, upon its completion in mid-2014, will play a crucial role in handling some of the most radioactive waste generated by reprocessing spent nuclear fuel at Sellafield.
The £400 million scheme is progressing rapidly, led by a team from the cradle of the British nuclear industry comprising Sellafield Ltd, which manages the nuclear site in Cumbria, supported by partner Costain Oil and Gas Process, the prime contractor, and the wider supply chain from Britain and overseas.
In a progressive move – and unusually for such a large Sellafield project – the design and construction of the Evaporator D facility has been modularised. This provides benefits in terms of overall cost and makes fabrication and testing much easier than a traditional on-site construction approach: for the Evaporator D, only connections between modules and existing services will be made on site. Fabrication is taking place at Interserve’s factory at Pioneer Point, Cheshire. From there the modules that will form the plant – primarily vessels and their interconnecting pipework within a structural steelwork frame – will be transported to Ellesmere Port and then to Cumbria by barge. Meanwhile, the construction of the building that will house the new unit is ongoing at Sellafield.
Andy Rimmer, senior mechanical engineer on the Evaporator D project and a member of the IMechE, explains that the approach to design and construction is to maximise the skills available in the supply chain. He says: “If we went back 20 years, we would have delivered this project within Sellafield, probably within our own design offices and bringing people in to supplement our own workforce.
“But the model we’re following these days is to engage with supply chain expertise and allow suppliers to bring that expertise into our nuclear world.” Costain was chosen, for example, because of its civil engineering know-how, expertise in the petrochemical industry, and experience of delivering modularised facilities.
The largest of the 11 Evaporator D modules will weigh 500 tonnes and measure 12.5m x 7.5m x 27m tall, so the logistics of transporting it onto the Sellafield site are complex. “We need to be able to get the modules on and off the barge, which will be beached adjacent to the Sellafield site,” explains Rimmer. “That has entailed a lot of engagement with stakeholders, because in getting the modules to the plant we will cross a tidal river, sand dunes, roads, and a section of Network Rail track. That has meant engagement with landowners and so on.
“They are hurdles we haven’t crossed before in terms of the various people we’ve had to get agreement from.” The modules will be transported on a multi-axle vehicle from their landing point to the construction site. A purpose-built gantry system will then be used to lift the modules and transfer them to their installation positions within the concrete structure. The gantry system uses two 38m-long beams that were used to lift the Russian Kursk submarine after it sank in the Barents Sea in 2000.
Evaporator D will play a critical role in the handling of highly active radioactive waste generated by nuclear fuel reprocessing at the Thorp and Magnox reprocessing plants at Sellafield. Historically, a number of evaporators have been built on the site and the latest follows on from a series of evaporators known as A, B and C. The evaporators are used to “boil off” materials within the waste to help reduce its volume before it is vitrified, or chemically combined with glass for storage.
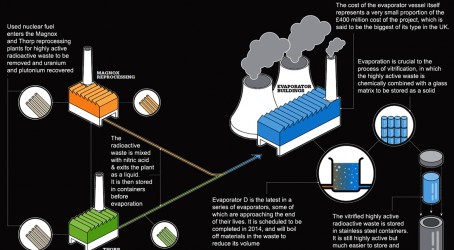
Spent fuel enters the Thorp and Magnox reprocessing plants where reusable uranium and plutonium can be recovered. But the process also generates high-level radioactive waste, which exits the plant in liquid form – in a highly corrosive nitric acid solution – which is then stored in highly active storage tanks (HASTs).
Once stored in the HASTs, the radioactive liquors are agitated and cooled. Agitation is necessary to prevent fissile materials in the waste settling and generating too much heat. “There is still radiolytic heat coming from these liquors,” explains Rimmer. “In other words, they generate heat themselves.” An appropriate analogy for imagining how they are treated in the tanks is to look on the fissile materials as sand in water, explains David Campbell, the senior welding engineer on the Evaporator D project. “The particles of sand in water, or in this case the fissile or active materials, generate heat when they come very close together. So in the HASTs this active material is being moved around constantly to stop it settling.”
Rimmer goes on: “The waste is in a liquid form at this point, which is not ideal. The aim is to vitrify as much waste as we can – to make it solid so you don’t have that problem.”
Before the waste is vitrified, however, the evaporators are used to boil off acids and some other chemicals to leave concentrated waste at lower volumes that is ready for vitrification in one of three lines at Sellafield. Evaporator D is being built because A, B and C have either reached or are approaching the end of their lives. Rimmer says: “An important part of this process is to reduce the volume of waste before trying to vitrify. Clearly, you want to end up with the minimum quantity of vitrified waste for storage purposes and you don’t want to have to store benign materials with the waste.”
Vitrified waste, which is stored in stainless steel containers, still generates high levels of radiation. “But that’s relatively easy to manage,” says Rimmer. “We deal with the radiation by storing the highly active waste in stores with thick concrete walls. And the fact that it’s been vitrified means that we don’t have the issue of a mobile liquid that can leak.”
Vitrification is not the same as encapsulating waste, but actually involves chemically combining the waste in a glass matrix. “Encapsulating something is like putting steel swarf in a container and mixing it with concrete,” explains Rimmer. “If you blasted the concrete off, you’d still have steel swarf there. But vitrification is a chemically incorporating process – you don’t encapsulate the waste in glass, it becomes part of it.”
Campbell adds: “It’s more manageable because it’s solid, there’s no dust, and it generates a given amount of heat because of the way radioactive material is distributed in the glass matrix.” Rimmer says: “Evaporator D will support and is crucial to vitrification. If we can’t evaporate, we can’t vitrify.”
The new evaporator has been designed to accept a wider range of feed stream than previous evaporators, which will enable it to be used to help clean up the older evaporators for decommissioning. It will handle material from the “post-operational clean out” phase, a new development. This means that, as the other evaporators wind down, Evaporator D can be used to clean them up. Rimmer explains: “Instead of just dealing with arisings of waste from nuclear fuel reprocessing, the facility will eventually deal with arisings from the existing high active liquid effluent facility. The feed stream from those vessels – the original evaporators – may not be exactly the same as that arising from a normal evaporation cycle. We have widened the feed stream envelope so that the Evaporator D facility can enable clean-out.”
Sellafield has a commitment to reducing the level of waste stored in liquid form over time as part of the process of hazard reduction on site. The nuclear regulators and the community at large want to see the stocks of hazardous liquors reduced in quantity. “As a business, we've had a requirement to reduce liquid stocks for some time,” says Rimmer.
The links in the chain of nuclear plant that the evaporators are part of have to work smoothly, explains Campbell. “That’s the difficulty: you have a lot of different interacting plants and they have to run sweetly together.
“That takes a lot of effort, management and control. Clearly if one of the links breaks there is the potential to generate a backlog of waste.”
Meticulous design of plant’s central vessel
The Evaporator D vessel, the hub of the new plant, will be 11.7m high, feature six cooling and heating coils, and have a diameter of 3.4m. The main process vessels and pipework are made from a special grade of stainless steel suitable for handling nitric acid at high temperatures – of around 80°C. This material has been developed and refined by Sellafield after many years of handling such corrosive liquors. The material to be used in Evaporator D has a corrosion resistance some 20% greater than that used in earlier evaporators.
David Campbell says: “The heaviest module contains the hub, the Evaporator D vessel. If you were to buy the vessel on its own compared with the overall cost of the project it would be quite a small percentage – £1.5 million, so less than 0.5% of the total cost.
“Yet it’s costing £400 million to put that vessel in a building with all the protection, additional pipework and other vessels to support the evaporation process.”
The stainless steel for the evaporator facility is specially ordered from steelmakers. It is a refined version of a 304L grade that has enhanced corrosion resistance, produced to a Sellafield Ltd specification and named nitric acid grade. The project has procured some 600 tonnes of this steel as pipe and plate.
Campbell says: “The steelmaker carries out corrosion testing as part of the requirement to underpin the performance of the material. The steel coils, vessel shell and heads are all made from steel with a known corrosion resistance. The welding electrodes and welding consumables are similarly qualified. The result is we have a footprint of the plant’s capabilities to withstand the effects of nitric acid at 80°.” The welds on the pipework are to be X-rayed prior to the modules being closed off to ensure their integrity. “You have to have the highest level of welding and inspection to ensure you don’t have a failure in equipment that is not accessible,” explains Andy Rimmer.
“Once we’ve closed the cell, access for repair or maintenance is not possible.
“Evaporator D is designed robustly, to the highest modern standards, including seismic design. You engineer in as much redundancy as you can so you are not susceptible to single-point failures.”
Civil work on the building at Sellafield that will house the evaporator is progressing next to the highly active waste plant that stores the radioactive liquors. Once the modules have been transported from Interserve, they will be installed in cells and connected up at Sellafield. Rimmer says: “We are already starting to put some of the plant infrastructure in place. In three years’ time, there will be a gradually phased introduction of radioactive liquors as the plant is commissioned.”
Then, Evaporator D will take its place in the suite of facilities that process highly active liquid waste.