Frank Bachmann points out of his office window towards a menacing-looking, red-and-black John Cooper Works Mini. “Let’s take the car out for a spin,” he says. “You cannot truly appreciate a Mini unless you’ve felt the sensational ride quality.”
Bachmann has more reason than most to feel a sense of pride over his choice of wheels. He is managing director of the BMW Oxford plant where the cars are made, along with the body pressings and subassembly facility in Swindon. That makes him a busy man: the Oxford plant produces 200,000 Minis a year, with plans to ramp that up to almost 280,000 in the mid-term. Yet he enjoys the challenges that workload brings. “I’m an engineer. So what better job is there than making cars that I love? Coming to work in the morning and knowing that this is my team, and that I have responsibility for the plant – that’s what drives me forward.”
Bachmann is well aware that he is the custodian of 100 years of carmaking history on the Oxford site. The story begins in 1913, with the first Bullnose Morris Oxford being built by William Morris just a few hundred metres from where the modern Mini plant stands. Over the years, an array of famous – and some infamous – cars were produced there, including the Morris Minor, the Morris Marina, the Princess and the Austin Maestro. At various stages in its history, the plant also built Tiger Moth aircraft, ambulances, parachutes and iron lungs.
But it is in recent years, since it has been under the stewardship of the BMW group, that the Oxford plant has been reborn. Back in 2001, there were doubts that re-engineering and re-styling the iconic Mini would prove a successful move.
But those fears have been well and truly confounded: more than 2.25 million Minis have been made since then, with proliferation of the brand to encompass seven variants, five of which are produced at Oxford – the Hatch, Clubman, Convertible, Coupé and Roadster. The German automotive giant pumped hundreds of millions of pounds into the site, and now the plant is receiving more heavy investment to produce a new generation of the car.
“When we started the plant in 2001, there was a basic plan for 124,000 units a year, but the success of the Mini forced us quickly to increase capacity,” says Bachmann. “Today, we produce around 200,000 cars a year – that’s roughly one every 68 seconds. That is going to rise to around 280,000, thanks to an investment of £750 million across our three plants for the next-generation Mini, which will include 1,000 new robots in the bodyshop at Oxford. It is an exciting time.”
Such levels of output require enormous logistical planning and execution to ensure that production runs according to plan. The manufacturing operation at Oxford relies on a wide ecosystem of suppliers, some based on site and others around the country and beyond. Together, they supply around 6,000 different parts, which are delivered on a just-in-time basis. Major components are supplied to Oxford from BMW’s two other UK production facilities. Hams Hall, near Birmingham, makes the four-cylinder petrol engines, while Swindon stamps out 90% of the body pressings.
The flexibility of the Mini production line at Oxford means the plant can build any of the five different body styles produced there in any sequence. When this choice is added to the range of paint, interior trim, accessories and specialist equipment, the result is an almost infinite number of combinations. However, this flexibility means components have to be delivered in exactly the right order, the moment they are required on the production line – an approach that brings challenges, says Bachmann.
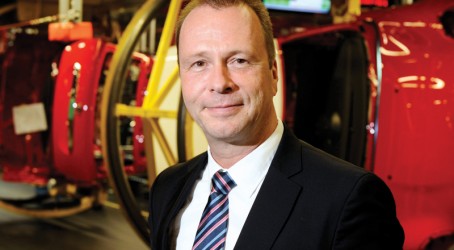
“We have a one-line system – all our options, derivatives and accessories are run through it. The big challenge is to equalise the workloads at each station. There could be a convertible coming along, then a US model high-loaded with options, then a hatchback with fewer options – it’s a balancing act,” he says.
“The second challenge is the logistics chain. It requires the right parts, at the right time, at the right station. The line operator is concentrating on fitting the correct part with the correct process into the car. So we try to set up the supply chain, as much as possible, to allow sequencing so that the operator can just grab into the tray and the right part is there.”
This approach means a shift in supply chain responsibility, says Bachmann. “Some of the responsibility the line operators would have had in the past is being pushed backwards to our suppliers. It requires a much closer collaboration with our supply chain. You cannot underestimate the impact the supply chain can have.”
The bodyshop is one of the most complex parts of the production chain. Back in the early days of Morris production on cars such as the Bullnose, coachmaking skills were employed. Panels were fitted by hand, and the eye was the most accurate quality assessment tool. These days, the tools are very different. The Oxford plant has around 500 robots which bring together 340 panels required to make the Mini bodyshell. Each bodyshell has 4,000 individual welds, and laser cameras check the accuracy of the assembly to within half the width of a human hair.
As part of the £750 million investment programme, major upgrades are taking place at the plant in preparation for the next-generation Mini. Current models are built on a unique platform, but the next-generation car will be based on a front-drive architecture shared with other BMW vehicles. In preparation for the new project, BMW is installing a further 1,000 robots, has already added a robotic glazing cell, and is introducing unmanned, automatically guided vehicles to transport components to the line at the right moment.
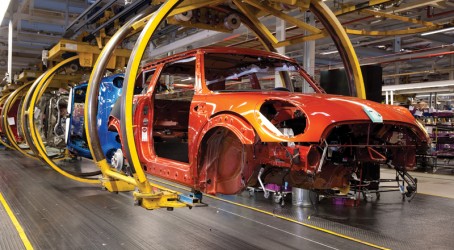
The extended use of robots is intended to ensure quality and reduce costs. “You cannot guarantee repeatable quality of the bodyshell without robots and automated measurement systems,” says Bachmann. “But robots also bring savings in the time and cost of labour, which are essential to help us stay competitive.”
BMW has also introduced ergonomic solutions that move the car to different heights along the line for easier and smoother assembly. “This is an important development,” says Bachmann. “We have invested a lot of money in height-adjustable skillet lines, so that line operators do not need to bend and stretch.”
Automated glazing equipment has also been introduced, alleviating the need for operators to manoeuvre 20kg units with the use of rubbers. “Glazing is increasingly part of the rigidity of the car, so it’s an important part of the structure. It therefore requires much more accuracy in terms of how it is glued, and in which position. The automated process is therefore a quality investment,” he says.
Production of the next generation is expected to begin later this year. Preparation for its arrival hasn’t just been about investments in technology and processes – skills development for the 4,000 employees who work at Oxford has also been high on the agenda.
For example, BMW runs a thriving apprenticeship programme at the Oxford plant, with courses lasting between three and four years, covering a wide range of skills including electrical maintenance and engineering. Training leads to an NVQ level-three qualification, and some apprentices will have the opportunity to progress right through to degree level. All technical apprentices attend a top specification training school at the plant.
“There has been a 10-fold investment in education and training over the past four years,” says Bachmann. But efforts are not just focusing on apprenticeships – the existing workforce is also a priority, he adds.
“We are retraining people to get them used to new processes and methods, in terms of both technical and leadership issues. For example, the next-generation Mini brings new levels of automation, and one challenge is understanding new control systems and techniques.
“Another area of investment in education is language training. The centre for global design for BMW is in Munich and the first language there is German. We need to be able to communicate effectively with our colleagues in Germany. Not every Bavarian speaks English,” he says.
Bachmann has his eyes fixed firmly on the future, with the start of production for the next generation of the Mini looming on the horizon. It isn’t the predicted volume increases at the Oxford plant that faze him – the investments made at the plant ensure that the target of 280,000 cars a year is achievable. The biggest challenge, he says, will be ensuring that quality doesn’t slip.
“Customer demands in the premium car sector are forever increasing. New products will inevitably have additional complexity, based on things such as legal requirements in areas such as crash safety and carbon dioxide output. Therefore, the supply chain will be ever more complex, and it doesn’t look like we will be getting fewer derivatives in the future. These are the real challenges.”
But Bachmann relishes challenges – he always has done. When BMW first announced that it was going to revitalise the cherished brand, and sell it all over the world, he was sceptical. But it didn’t stop him from buying into the bold ambitions.
“When I first got involved, I couldn’t believe we could sell a car the size of the Mini into the American market,” he says. “US customers wanted big cars and trucks – V6s and V8s, that sort of thing. They wanted comfort over a vehicle that was fun to drive. So I have been surprised at how big the success has been in the US.
“But the Mini is something special – it has a legacy and a heritage. It’s so different to drive from what our competitors produce. You are effectively sitting in a car that gives you the feel of a go-cart but with all the safety features and technologies of a big car. It comes back to quality. There is no compromise – we don’t make a difference between a BMW and Mini,” he says.
So where does Bachmann see the brand going next? At present, there are seven Mini variants – from the standard saloon through to the more chunkily styled, four-seater Countryman. Automotive industry watchers suggest that the next move could be a smaller Mini, more in keeping with the original Sir Alec Issigonis design. In 2011, at the Geneva motor show, BMW showed the Rocketman concept car – a “mini” Mini that evoked the spirit and packaging of the original design even more faithfully than current models. Ever since, there has been speculation that this model would enter production. There have also been rumours of a hybrid Mini, or even perhaps some kind of Mini pickup van.
On potential brand expansion, Bachmann remains coy. “I’m sure there will be a broader spectrum of derivatives,” he says. “The brand has the potential for a wider spectrum of models, without losing the ‘Mini-ness’. But what we don’t want to lose is what makes it so special – the driving behaviour, design, features, all the iconic stuff that was carried over from the classic model.”
Whichever way the brand develops, Bachmann plans to remain at Oxford to see that the production targets are delivered. Despite all the responsibilities of running one of the biggest car plants in the UK, he loves every aspect of his job. “What I enjoy most is working with the people who we have here. We manage all the challenges we face together. That’s what gives me a good feeling when I go home each evening.
“Yes, sometimes the workload is heavy – and sometimes I don’t even get to have an evening. Performance figures worry me, losing hours due to breakdown – that sort of thing. But, in the main, the positives are in the majority. It’s a great job to have.”

Partners in the Netherlands and Austria help to meet demand
Production of the modern Mini isn’t restricted to the Oxford facility. The success of the brand in recent times has created production constraints at the plant, so BMW has looked to build the cars elsewhere to meet buoyant demand.
Magna Steyr in Austria builds the Countryman sports utility vehicle and the Paceman, a sportier coupé version of the SUV. Mini is also adding capacity at Nedcar in the Netherlands in 2014, although there has been no confirmation of what models will be manufactured at the plant.
The use of partner plants to make the Mini is a sound means of meeting customer demand while meeting quality targets, says Frank Bachmann, managing director of the Oxford BMW plant. “But Munich remains the heart of BMW, and Oxford the heart of the Mini,” he adds.
The deal to see Minis made at VDL’s Nedcar plant at Born – previously owned by Mitsubishi – was struck to establish a contract satellite manufacturer as near the UK as possible. Oxford will provide production expertise for the new operation, particularly in dealing with the high levels of customisation that Mini demands and in operating multi-model production lines.
“I will go to the plant this month,” says Bachmann. “There will be close collaboration with Nedcar. Its management was over with us a few weeks ago and we have Nedcar colleagues here for training in how our production system works. Nedcar will produce a product that we are proud of – that is a prerequisite.”
Bachmann is convinced that the satellite production model will deliver cars that meet Mini quality standards. “Independent of where the cars are built, the quality standards are clear. Nedcar does not have to build the car in exactly the same operation as we do. But it needs to understand how to build the car, and to understand our quality requirements. It has to deliver to the same quality or even better. That way, we can learn from each other.”
A century of car production: Oxford plant facts at a glance
- The plant’s first car was a Bullnose Morris, produced on 28 March 1913
- Scores of models of many brands (MG, Wolseley, Riley, Austin, Austin Healey Sprite, Mini, Princess, Triumph, Rover, Vanden Plas, Sterling, Mini) including one Japanese (Honda) have been produced at the plant
- The current BMW site spans 172 acres
- Employees number 4,000
- Five models are produced on the same manufacturing line: Hatch, Clubman, Convertible, Coupé, Roadster
- Mini is the third largest car producer in the UK, behind Nissan and Jaguar Land Rover
- Since its relaunch in 2001, 1.7 million Minis have been exported to 107 countries
- Minis comprise 14% of total vehicle exports and there are 1,500 dealers worldwide
- The plant has produced 2.25 million cars since 2001
- Total car production at Oxford stands at 11.655 million and counting
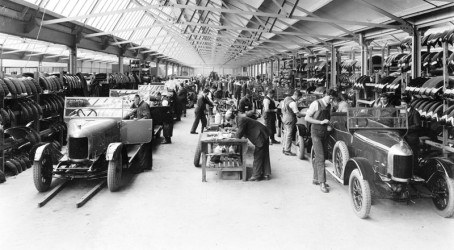
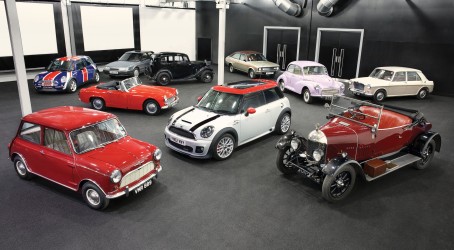