Open-rotor engines a ‘game-changing’ solution
Rolls-Royce is convinced that open-rotor engine design will deliver a “step-change” in performance over existing turbofans.
The company has completed a third set of windtunnel tests of potential open-rotor designs and the results have encouraged it to predict that the technology will enter service by the first half of the next decade.
Mark King, president civil aerospace at Rolls-Royce, said: “The open rotor is the only real game changer relative to an advanced turbofan. This is the only thing that can deliver clear daylight – a clear 10% better than any advanced turbofan. It’s a prospect for a significant step-change.”
Wind tunnel tests had led the company to believe that an open-rotor design would be quieter than any engine of an equivalent size that is flying today.
Rolls-Royce said that an open-rotor engine based on gas turbine-powered contra-rotating propellers was suited for the 20,000-35,000lb thrust range, powering a narrow body aircraft of 100-200 seats. “One of our priorities is to make sure we are ready for the new aircraft.”
Open-rotor research is being undertaken at several Rolls-Royce plants and the company continues to discuss the technology with Airbus and Boeing.
King said: “I don’t think we’ve seen any showstoppers in bringing open rotor to market.
“It’s early days but I don’t think we see anything that says it’s not possible.”
King admitted that Rolls-Royce still harboured hopes for blended wing body aircraft design.
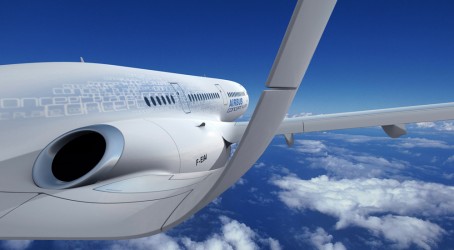
Aerospace engineers take a flight of fancy
Airbus has given its engineers the chance to fully open their minds and imagine what an aircraft could look like in 2050.
The “engineers’ dream” features ultra long and slim wings, semi-embedded engines, a U-shaped tail and lightweight ‘intelligent’ body, all aimed at improving aerodynamic performance and reducing fuel burn.
Inside, the plane features morphing seats made from ecological, self-cleaning materials which change shape for a snug fit; walls that become see-through at the touch of a button, affording 360° views; and holographic projections of virtual decor.
Green energy sources such as fuel cells, solar panels and personal body heat might power some systems.
Charles Champion, executive president engineering at Airbus, said: “The technologies it features, though feasible, are not likely to come together in the same manner. Here we are stretching our imagination.”
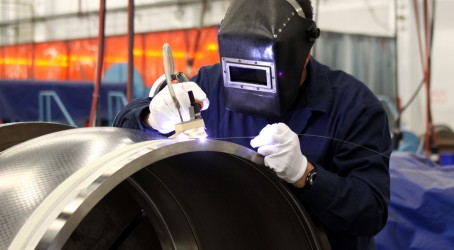
GKN puts faith in metal products as future of aerosapce
GKN has instigated a tranche of advanced metallic research projects working with materials such as advanced aluminium and titanium alloys, reinforcing the company’s belief that metal parts will continue to find a role in future aircraft programmes.
Despite the emergence of composite technologies on new aircraft such as Boeing’s 787, GKN said that metallic technologies would continue to form a key part of its aerospace products portfolio, with around 50% of its business still metallic-based.
Rich Oldfield, director of technology at GKN Aerospace, said that over the next decade new developments in metal manufacture, including the use of robotics, new cutting and joining processes and machining developments, could cut material consumption by 50% while improving the speed, capacity and quality of the manufacture of complex aero-engine structures.
“Advanced metallics still have a key role to play in aerospace,” said Oldfield. “In many applications, metals remain the right material.”
The company has embarked on a three-year project looking at linear friction welding of aluminium and titanium billets which Oldfield said could deliver a 40% reduction in material consumption relative to plate-machined components. The work will run until 2012.
Other projects include research into electron beam additive materials, which could help accelerate customer acceptance of additive manufacturing components, and research into hybrid machining to achieve a 50% increase in metallic removal rates for roughing operations on titanium aerospace components.
EADS offers Boeing peace pipe over algae biofuel development
EADS has called on arch-rival Boeing to join forces with it to accelerate the development of biofuel based on algae.
Dr Jean Botti, chief technical officer of EADS, said that algae was the most promising biofuel feedstock that it had investigated.
He said its potential as a replacement for kerosene was so great that the industry needed to put aside traditional rivalries and move forward as one.
“Now is the time to get serious about algae and we need to come together to do that,” he said. “I would love Boeing to work with us on this. Working together with Boeing is key to the success – we can’t do it alone.”
Botti’s enthusiasm for the technology follows a successful EADS demonstration project which has resulted in the world’s first flight of an aircraft powered by pure biofuel made from algae. Only relatively minor modifications and adjustments had to be made to the engines of a Diamond Aircraft DA42 to qualify the biofuel from algae for the demonstration flights.
The results showed that due to the higher energy content of the algae biofuel, fuel consumption was 1.5 litres per hour lower compared to conventional JET-A1 fuel, while maintaining equal performance.
Botti said: “Third generation biofuels are more than just a replacement for fossil petroleum. They push the possibilities of future propulsion.”
The exhaust gas quality measurements indicate that biofuel from algae contains eight times less hydrocarbons than kerosene derived from crude oil. In addition, nitrogen oxide and sulphur oxide emissions will also be reduced (up to 40% less nitrogen oxides and 10ppm sulphur oxides compared with 600ppm of conventional Jet-A1-fuel) due to the very low nitrogen and sulphur content of the biofuel compared to fossil fuel.
EADS research shows that all necessary technologies to develop the production of biofuel from algae are known, but industrial size and economy require further development.
EADS had to go to Argentina to source the algae biofuel for its demonstration project and it could only procure relatively small amounts.
“It is still difficult to get the required amounts of fuel,” said Botti. “I would have loved to run the trials on an A320 aircraft but that would have required much higher volumes. There are still not enough respected people out there supplying the oil.”
It is significantly more expensive to produce oil from algae in comparison to sourcing crude oil. If algae-based fuel is to be able to compete with kerosene, research and development work must aim to establish a cost-effective mass production of algae biofuels using industrial quantities of carbon dioxide.
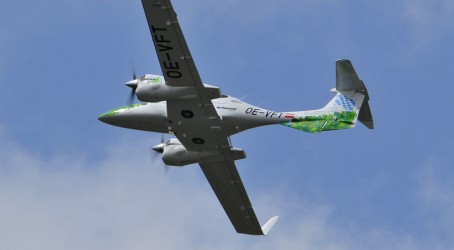
Air security
Thales UK has launched an open challenge to find a technology to improve aviation security at any stage in the air travel process.
The competition, the Instinct-Technology demonstrator, offers the chance to share in a £50,000 cash prize and the opportunity to test the technology in a real environment. The closing date for submissions is 21 August. More details can be found at www.intellectuk.org.
Furnace investment
Doncasters has invested £3 million in its Ross & Catherall superalloy production plant in Sheffield. The money has been spent on an upgraded vacuum induction degassing and pouring furnace, additional furnace bodies and the expansion of its concast capability.
The firm has also invested £1.3 million at its Doncasters Aerospace Components business in Shrewsbury, upgrading its plasma spray facilities and acquiring a CO2 laser.
EcoDemonstrator
Boeing has launched the EcoDemonstrator programme to accelerate environmental technologies such as ceramic matrix composite acoustic engine nozzles, advanced inlets, and adaptive wing trailing edge flaps that can help reduce fuel consumption and noise during take-off, climb and landing.
The programe will also include work to evaluate regenerative fuel cells for onboard auxiliary power applications.
Tugs away
WheelTug is developing a system that will allow aircraft to taxi backwards and forwards without the use of tugs or engines.
The WheelTug system uses two electric motors fitted in the nosewheel to move the aircraft, with power supplied from the auxiliary power unit. The movement of the aircraft can be controlled by the pilots.
WheelTug says the system has the potential to bring substantial fuel savings, faster turnaround times and reduced engine wear and repair costs. The company hopes to trial the technology on a Boeing 737 later this year.