Articles
A small company in Newcastle has scaled up its innovative method of “metal blowing” to offer a mass market product for the first time.
Engineering and design firm Full Blown is producing and marketing the world’s first “inflated metal” radiator using a bespoke cold forming process developed and patented by Full Blown.
The process takes two sheets of joined metal and injects a high pressure liquid or gas between them to “blow” it up, akin to the process of glass blowing. The inflation process uses metals including stainless steel, copper and brass and exploits the malleability of the metals. Benefits include improved weldability and durability, as well as a more interesting range of available finishes for the product.
Up until now the process has been mainly restricted to artisan applications, such as decorations, furnishings and art installations. Stephen Newby, managing director of Full Blown said variations of the metal blowing process are used in industry, but these use moulds and do not allow the variation of premium finishes available using inflation technology.
Newby said: “We’ve got a specially designed production machine that controls the input of the gas or liquid’s pressure and controls the shape. We design the product using 3D CAD and then it’s a case of trial and error with the machine to produce the shape – you can only get so far with inflating because of the tensile strength of the steel. Prototyping is a slow process but once set up manufacturing is fast.”
All of the “Squeeze” radiators are inflated at Full Blown’s manufacturing site and are fitted out and marketed by different companies. Newby, who worked as a ship builder until 1995, has had help from the Manufacturing Advisory Service to scale up the manufacturing process and set up the supply chain.
Newby said: “I escaped industry and went into art and design, so things have come full circle and I’m now back involved in these trades. It’s been a pretty steep learning curve but we’ve had support on things like planning, price and strategic management.
“Our next step will be taking the technology into a number of different applications. We’re keen to develop architectural products such as large facades.”
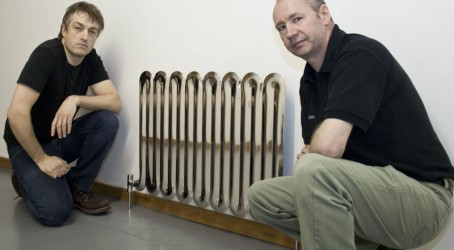