Therapy industry: Guy's Hospital in London is hosting the Cell Therapy Centre Catapult
The tower of Guy’s Hospital retains an unmistakable place among London’s skyscrapers, although it has now undeniably been usurped – and overshadowed – by its gigantic, fashionable and more tourist-friendly neighbour, the Shard. Built in 1974, the tower was the tallest hospital building in the world until 1990, when the O’Quinn Medical Tower in Houston took the title.
This year, however, a programme of repairs and environmental improvements saw the addition of a light sculpture that made Guy’s tower 148.65m high – enough for the London landmark to regain the crown lost to its rival in Texas.
If lofty academic ambition should be measured by reaching for the skies, then the Cell Therapy Catapult centre – one of the seven centres set up by the government in response to recommendations made by Silicon Fen entrepreneur Hermann Hauser – is in the right place, situated as it is on the 12th floor of the Guy’s tower. The views may be stunning, but the challenge is to ensure that the research work remains commercially grounded – and that great ideas don’t go the way great ideas often seem to go in the UK: nowhere.
Before the Chancellor’s autumn statement gave a clearer idea of forthcoming science and innovation policy, Hauser was relaxed and refreshingly candid as he outlined the results of his review of the new Catapults at the Cell Therapy Centre last month. He was clear that there should be more, perhaps as many as 30 by 2030, and that they would require a lot more money, meaning a doubling of the budget to £1 billion by the end of the decade, echoing the findings of an earlier study for Labour by Jaguar Land Rover executive director Mike Wright.
The centres that were based on bringing existing institutions under the Catapult umbrella were doing well: it was too early to say for some of the others, said Hauser. Encouragingly, the High Value Manufacturing Catapult, which consists of seven technology and innovation centres, including Sheffield’s Advanced Manufacturing Research Centre and Warwick Manufacturing Group, overseen by Innovate UK with more than £200 million of government investment, has been an early success story of the programme.
Hauser’s review comes four years after his original proposals – made for Lord Mandelson under the previous government – were adopted by the coalition, to some surprise. The fact that the concept survived the change of government, and looks like it will do so again next year following the general election, is testament to cross-party recognition that the Catapults are filling a long-recognised gap in translating Britain’s stellar research base into commercially viable industrial activity.
But the fact that this is happening at all was never a given, admits Hauser. “Yes, I was surprised,” he says. “It was done for Peter Mandelson, so when Vince Cable and former science minister David Willetts had me back and said the report made sense to them as well, it was a surprise.
“However, if you look at the substance of the report – as opposed to the politics – that had a lot of cross-party support. And I have not had a critical voice from the Opposition now saying ‘these Catapults are a bad idea’.” Hauser says there was an acknowledgement that “scientists had become too esoteric and detached from the industrial base”.
He adds: “If you look at the history of the Royal Society, the science had always been quite applied and used to solve real-world problems. We felt it was time for society and science to reconnect with industry. And although academics are notorious for not voting unanimously on anything, we managed to get the council of the Royal Society to support that.”
Citations for academic research in science in the UK are second only to those from the US, says Hauser. And yet there is a sense that this pioneering work is continually underexploited. “We have real prowess in science,” he adds. “But everyone laments the fact that we don’t seem to be getting as much value in the UK from our science as other countries do. One of the problems is the lack of intermediate institutions – which is what the Catapults are there for.”
Professor Ric Parker, director of research and technology at Rolls-Royce, says he admires Hauser’s ideas and he regards the High Value Manufacturing Catapult, which is helping the aeroengine maker to develop cutting-edge turbine-blade designs, as a success. “I got so used to the previous government talking about how it wouldn’t pick winners,” he says. “Well, it seemed to be pretty good at picking losers.” Labour has backed the government’s industrial strategy and said it would persevere with it, adding to the programme if necessary, if it comes to power next year.
In turn, Parker is happy to praise the £2 billion Aerospace Growth Partnership and the creation of the Aerospace Technology Institute. “We’re particularly pleased with the institute, which is already doing some good stuff, and it’s something I’ve been pushing for. I think the Technology Strategy Board – now known as Innovate UK – has been a great model, and it’s actually stimulated a lot of collaborative, innovative work.”
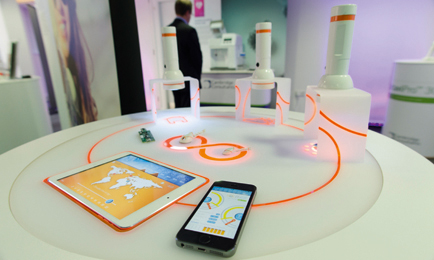
Sun tracker: Innovative device for measuring sunlight from Cambridge Consultants
But not all support for business and innovation has been as welcome, says Parker. For instance, he says the former regional development agencies should not have been dissolved in the so-called ‘bonfire of the quangos’ as the government frantically cut public spending following the financial crisis.
Although there are many innovative small aerospace engineering firms working in the UK sector, which is second in value only to the US, that are benefiting from initiatives such as the Rolls-Royce-backed Sharing in Growth scheme, Parker says the new local enterprise partnerships are too small to engage with them effectively.
“That’s really where organisations such as Leicestershire’s Pera Technology can become a one-stop shop for some of the smaller firms that don’t have the time or the people to find their way around the various schemes. They supply a useful service in terms of being able to pull groups of companies together in the UK and help them find their way into Europe.”
Rolls-Royce has launched an ‘innovation portal’ on its intranet so people can post ideas on how to solve problems facing the business. Parker says: “It is surprising how often the most promising answer to a challenge doesn’t come from the area that’s charged with coming up with that answer in the first place. You always do things in a particular way. Someone says ‘to make it 10% better would be impossible – it took us 20 years to get to where we are today’. Someone looking at it from the outside sees things differently, and that’s vitally important.”
The OEM also operates an inventors’ portal so that external inventors have a formal route to submit ideas. It gives them advice on protecting their ideas properly and how to form non-disclosure agreements. “If an inventor can’t afford the patenting process themselves, we may be able to help,” says Parker.
Hauser notes that technology transfer is “essentially about transfer of people,” whether from within an organisation, or from the research community into industry, and vice versa. Parker says one of the challenges is to ensure that a design dreamt up by a team of PhD students can be made by the manufacturing staff on the other side of the factory wall.
“You have to get engagement between them, which is why I favour a model where people are more embedded,” says Parker. “That is about people moving around. Designers and manufacturing engineers sit side-by-side. And one of the joys of my jobs is getting out to visit our suppliers.”
Sometimes those suppliers follow Rolls-Royce overseas, for example to its operations for turbine-blade design and manufacture in Singapore. Manufacturing has a share of GDP there almost double that of the UK. “It is a great place to innovate as well,” says Parker.
“They have a government that’s open to innovation, and is very imaginative. It is not just in the sense of financial investment. It is creating the skills in Singapore. In a lot of the schemes we are involved in they will lend researchers to work on our projects.”
The fact that Rolls-Royce is such a multinational business today means more opportunities for young engineers. “When I joined Rolls-Royce in 1978, I had a choice of Derby or Bristol,” says Parker. “Now young people can have a career that will take in several different countries. And I think if they want to get on, they will have to do that.”
If vital commercially important intellectual property is generated from the design and manufacture of a new turbine blade, Rolls-Royce hangs on to it. “There are certain things where the intellectual property rights are so vital from the manufacturing process itself, and we are good at it, and we want to keep that in-house. Our hollow titanium fan blade is very important to the company so we do it in our Singapore factory. It’s a Rolls-Royce product in-house.”
Alternatively, says Parker, if the company wants high quality but cheaper parts it will find the best supplier. A third area involves transforming its own innovations into products with tier-one suppliers, such as a fan blade produced in partnership with giant aerospace supplier GKN.
Innovation, as in many areas of engineering, concerns compromise: fan sizes can be made bigger, which makes engines quieter, but bigger fans mean more weight, less efficiency – and more fuel burn. From a cost point of view, moves are afoot to replace titanium, an expensive material, with more composites in aeroengines. “All the environmental legislation is about cleaning up the planet and global warming, and then there is the issue of local air quality and, around airports, noise.”
Parker says there is a level of naivety around these issues and “we’re not getting the message through to politicians that you can’t achieve all these goals simultaneously – there are some fundamental laws of physics that are working against you”.
More efficient engines, where the core gets hotter, create more NOx, says Parker. “The lobby that says ‘that aircraft’s too noisy – I don’t want it flying over my house’ has a lot more political power than those trying to combat climate change. The priorities can get distorted. We have been publicly attacked by politicians in the US and elsewhere who say noise is the issue.”
But global agreements are needed to control emissions of greenhouse gases from aeroengines. “You cannot just impose a carbon flying tax for Europe. People will avoid flying into or over Europe if it is imposed unilaterally,” he says.
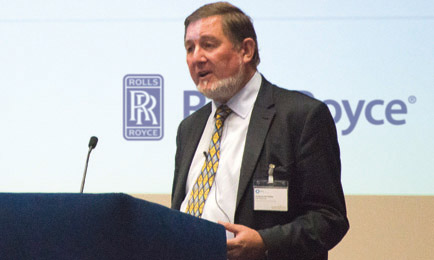
3D printing shapes up
Rolls-Royce is using additive layer manufacturing to test ideas for new turbine blade shapes. “With 3D printing, the biggest benefit in the short term is being able to make something to a different shape and test it – so immediate rapid prototyping is the first application,” says research director Professor Ric Parker (pictured right).
He adds that a lot of post-processing of components made using additive layer manufacturing is required if they are to be used for aerospace applications. Consumer-led mass customisation, such as for footwear, is likely to be where the technology achieves critical mass in the near term. “It will then trickle through to more safety-conscious industries,” Parker believes. “There is quite a lot of work to be done to really understand the manufacturing parameters.”
But the potential for innovation in the technology is clear. He says: “It can enable you to make shapes and components that you couldn’t make from any other technique, and that’s where it comes into its own. If you come up with something that’s high value in that it’s more efficient, and 3D manufacturing is the only way you can make it – those will be the bits that get done that way.”
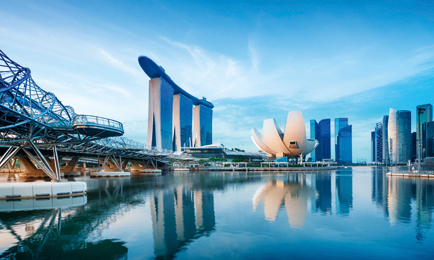
Island life: Rolls-Royce set up an aerospace factory on Singapore
British companies turn to Singaporean expertise
British engineers are exploiting the research and development and industrial bases of countries overseas as well as manufacturing abroad. Rolls-Royce developed a facility in Singapore to manufacture hollow titanium wide-chord fan blades, the first place outside Britain to make this specialist component. The factory is at Rolls-Royce’s Seletar campus, alongside the company’s other new facility for the assembly and testing of aircraft engines. The campus will create up to 500 jobs.
Aerospace firm Meggitt also has a factory at Seletar Park, and RLC Engineering Group, a small firm based on the Isle of Man, which has a thriving aerospace sector, set up there too so it could supply titanium alloy for Rolls-Royce engine blades. British aerospace manufacturers are exploiting Singapore’s strong science base for R&D activities.
Aerospace is an important sector for the island, worth almost S$9 billion (£4.4 billion). The Singapore air show, meanwhile, is Asia’s largest aerospace event. Much of the growth in aircraft new build and the booming global order book is being driven by the region, according to aerospace and defence trade body ADS.
Singapore is “fast establishing itself as an R&D hub,” according to the island’s Economic Development Board. In 2010, Singapore’s gross expenditure on R&D grew from $S6 billion to S$6.5 billion. The number of research scientists and engineers rose from more than 25,600 to almost 28,300 in 2010. The World Economic Forum’s Global Competitiveness Report for 2011-12 ranks Singapore as having the best intellectual property protection in Asia. Manufacturing accounts for 18% of GDP.
Rolls-Royce is not the only major Western manufacturer to have operations on Singapore. Bell Helicopter, Cessna Aircraft and Hawker Pacific also have facilities at Seletar Park, while ABB has its regional robotics packaging application hub on the island. The ABB centre provides value-added engineering solutions for industrial manufacturing processes tailored for the Asian market. The hub is developing robotics manufacturing solutions in hardware and software for sectors including food and beverages, pharmaceuticals, consumer electronics and solar photovoltaics.
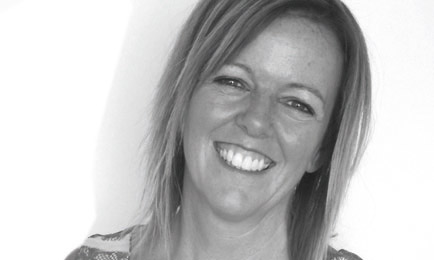
Q&A with Sally Uren, chief executive, Forum for the Future
As an organisation focused on sustainable development, does Forum for the Future work with manufacturers?
We are trying to get manufacturers to focus on innovation to deliver sustainability. We have worked with automotive catalyst maker Johnson Matthey, for example, on sustainability, and we feel business-to-business brands hold many exciting ideas. We’d like to see the ones that are sustainable make it to market.
Engineers will play a key role in development challenges. How do you see engineers helping to change the world for the better?
Engineering is part of what I would call a systemic solution. While we are ferrying in aid to deal with the symptoms of water-borne disease we are not getting to the cause. Putting in infrastructure to give people access to clean water should be where we are investing. Engineering is a real tool for positive change when it comes to sustainable development.
What is the relationship between sustainability and innovation?
The real opportunity is to ask how innovation might drive more sustainable products and services. What is it that we are trying to do? From my perspective it is to create a sustainable future and a sustainable society, and innovation gives you the ability to leapfrog, and think transformationally. Equally, there are some innovations where you question the point. But harnessing innovation to deliver sustainable development outcomes is a massive opportunity.
You say we are on a ‘hedonistic treadmill’ at the moment. What should we be on?
We should be running on equipment that is generating energy for the grid – and feeding it back in. We generate so much energy that we just lose.
You also say corporate social responsibility (CSR) became a PR move in the noughties. Where are we at with it now?
There are still some businesses that have yet to be enlightened that CSR isn’t the answer – but there is also an increasing number of businesses that are talking about sustainability, and putting big environmental and social challenges at the heart of their business model. They are experimenting – and they are innovating for the future. CSR has no role in that at all.
In the face of a lot of bad news on the environment, how do you maintain an optimistic outlook?
I do see innovation, and I do see breakthroughs. There is cause for hope. You could get depressed if you thought innovations would never scale, but I’ve seen them scale. Just think about what happened with smoking. Change does happen. We managed to legislate to close the ozone layer and ban CFCs. It can happen. My big question is whether it’s going to happen fast enough. That’s what keeps me awake at night.
Uren was speaking at Cambridge Consultants’ Innovation Day