It looks an obvious win-win. Every year in the UK, in the region of 16 million tonnes of food goes to waste, most ending up in landfill sites, and these sites can take no more. At the same time there’s continuing commitment by government, widely supported, to generate more of our energy and heat requirements from renewable sources, and particularly attractive are sources that aren’t weather dependent.
So the answer is obvious. Take the mountain of food waste and convert it to energy. Job done.
This is broadly the government’s thinking in its waste policy review produced last month; on the same day, it also put out a “strategy and action plan” for anaerobic digestion, the principal technology likely to be used in plans to convert more food waste into usable energy.
So a waste strategy and an energy strategy, but which takes priority? You get a clue from the fact that both emerged from Defra, the environment, food and rural affairs ministry, rather than from the energy and climate change department. Waste comes first.
But that’s been welcomed even by renewable-energy groups. “The government’s aim of getting ‘the most energy out of genuinely residual waste, not to get the most waste into energy recovery’ is spot on,” said Gaynor Hartnell, chief executive of the Renewable Energy Association in response to the two documents. The aim is high recycling of valuable commodities within waste as a whole and then high energy recovery.
But with food waste there are really only two possible end-products: a residue that will, it is hoped, be nutrient-rich enough to be valued and used as a fertiliser without containing the unpleasantnesses that would stop it going back to the food chain. And energy. But this simplicity masks several difficulties and they are getting the nascent UK industry a bit steamed up.
Earlier this year, PDM, which claims to be the largest UK food recycling group, put out a “manifesto” – Vision 2020 – in which it called for campaigns of national awareness of food recycling and an outright ban in England by 2020 on putting food waste in landfill. Chief executive Andy Smith said that acceptance of food recycling by the public and business was “reaching a tipping point,” and the moment had to be seized.
PDM’s first ReFood anaerobic digestion (AD) plant, close to completion at its site in Doncaster, is part of that. Commercial director Philip Simpson says: “We’re also looking at building four more AD plants around the UK on our existing sites.”
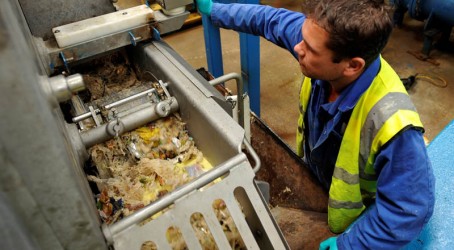
The Doncaster plant will handle 45,000 tonnes of food waste a year, and will produce 2.8MW of power and heat. In PDM’s idealised Vision 2020 world that food waste would come from sorted trade and municipal refuse. And indeed in the medium term that may very well happen.
But, in this area of waste and energy, what looks to be eminently sensible and straightforward isn’t quite there yet, in England at any rate. The numbers don’t quite add up; the political will is strong, but maybe not yet strong enough. PDM’s four new AD plants are geared, says Simpson, to match the growth in food waste that’s projected to move away from landfill in coming years.
But it’s all slightly up in the air. “In several places in Europe, in Ireland, Germany and even Scotland, all these countries are looking to take food waste out of landfill within a defined timeframe,” says Simpson. “In England, we have a very vague move towards a date. Obviously what we want is a definite ‘You will do it’ by that date. Because then we can start spending serious money knowing that something serious is going to happen.”
In the absence of that, contingencies have to be made. At the new Doncaster AD plant, some of the baseload feedstock will come from PDM’s own food processing factories on the same site: “We have four production plants there, including a pet-food primary processing facility and an edible-oils refinery. So to start with the AD plant will almost be an embedded facility supplying service to those factories, and that takes some of the risk out of it,” says Simpson.
This pattern of operation in which a plant that could form part of a national resource is bolstered by an in-house demand is not new: in fact, PDM uses it elsewhere with different technology. At Widnes on the Mersey, it operates a food-waste incineration plant which again takes much of its feedstock from its own plant, this time a meat-rendering plant, next door. The fluidised bed combustion plant, built a decade ago, is a legacy from the foot-and-mouth and BSE mad-cow diseases of that time. It was designed to put the equivalent of a fire-break in the food chain to stop these diseases from recurring.
Because its primary purpose is food-waste incineration, Widnes is pretty much a model biomass burning plant, says Simpson – many other biomass installations have been converted from other fuels. Nevertheless, the current baseload raw material, rendered protein parts of animals that are barred from use in animal food, is a dry-ish sticky powder that would need water adding to it in normal circumstances. Which is where more general food waste, with a higher moisture content of around 75%, comes in. “Obviously there’s a commercial benefit in not burning water and we burn this wet material in with the dry material,” he says.
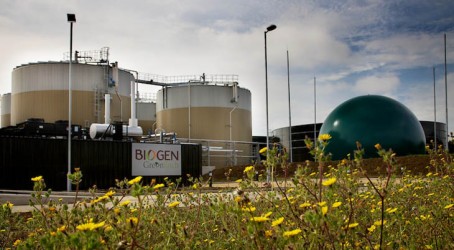
The output from Widnes, though, is energy, and only energy. Combustion is good technology where the feedstock has to be destroyed. But with most food waste there’s a potential second end-product in the fertiliser that is produced, and this could tip the balance towards AD plants.
Biogen Greenfinch is a second UK-owned designer, builder and operator of AD plants. It comes at the technology from a different direction from PDM, but ends up at almost the same point: a 45,000 tonnes/year two-tank plant as standard.
Biogen Greenfinch’s antecedents are in a long tradition of AD. Engineering director David Woolgar worked in the sewage industry, where anaerobic sludge digestion has been a standard treatment for many years, and the company originated as part of a farm business, treating agricultural slurries to produce a non-toxic useful end-product, the digestate used as fertiliser.
These are essentially wet processes and in Biogen Greenfinch’s early food-waste AD trials it used the animal slurries both to add moisture to the waste material and to transfer some bacteria cultures back into the mix. After a demonstrator built for Defra in 2005 that used pig slurry from the company’s own unit, it went for a food-waste-only plant at Westwood, near Rushden in Northamptonshire, using no animal slurries at all.
“If you’re using food crops the material inside the tank is thicker, so the mechanics of agitating it become slightly more significant,” says Woolgar. But essentially it’s the same idea: a mix of mechanical and biological engineering with lots of control systems thrown in. It is, though, all dependent for success on upstream and downstream processes and here again you get the impression that the UK, or England at least, is still rather feeling its way towards the answers.
“AD plants are not really fussy, in fact they’re very tolerant,” says Woolgar. “If you fed it just pure maize and cow slurry then even though it’s a single feedstock you’re getting a lot of other things coming in with the slurry, so that’s good. But if it’s just food waste then a good different mix of foods will give you enough for different kinds of bacteria for a really healthy digester.”
So they work. But upstream they need sorted food-waste streams, “source segregated” in the jargon of the business. “That’s very good for AD because you know it’s not been contaminated,” says Woolgar. “The digestate that comes out then is really suitable for going on to the land as a fertiliser.”
But source segregation demands public acceptance, local authority will (and cash), and plants that are relatively accessible. In Woolgar’s estimation, it might work for maybe 4 million tonnes of food waste a year: a significant proportion of the total, but not a panacea. “
At Lakeside in London there’s an incinerator plant where you separate out the easy recyclates and burn the rest. With blocks of flats in cities with only one or two rubbish chutes, that’s probably sensible,” he says. “Go to the other extreme and in a very rural area sending a van around to pick up a couple of kilos of food waste becomes expensive again. There’s a sweet spot in the middle where AD makes sense, but you have to be realistic.”
The realistic figure is maybe about 90 plants of the 45,000 tonnes/year capacity. Currently there are around 10.
Realism is needed too about the digestate. In rough terms, an AD plant produces about 80% of its output as digestate, and, though it can stop fertiliser imports and their heavy carbon footprint, it’s still a product that needs a market: agricultural land. “You can’t just put it down the drain because it’s strong stuff and the water authority would rightly object, but you need your market fairly close by to get the true benefit,” he says.
And then there is a mismatch in some of the energy figures too. At Westwood, Biogen Greenfinch is using about 10-12% of the energy in running the plant “so we’ve got over six times the surplus. We get about 40% in the form of electricity from burning the biogas and 40% or so as heat. There are some losses on the mechanical side and some that can’t be recovered.”
But though the electricity can and will increasingly be fed back in to the grid, the heat has to be used more locally. “At the moment, we don’t recover the heat off the exhaust systems because we have sufficient heat for pasteurisation, heating the building and so on, and the rest is unfortunately dumped.” You might avoid that by putting the plant in an urban setting, but then you’d have the problems of getting rid of the digestate: something of a catch-22.
So, energy from food waste? Nice idea, and sounds obvious. But will it work? The answer is probably yes. But it’s not quite as simple as it seems.
Friendly bacteria get to work
Anaerobic digestion is essentially what it says: a process of bacterial digestion, akin to that carried out by animals like you, me and cattle, done inside big tanks under airless conditions. Feedstock of food waste is shredded to particles of around 12mm size to let the bugs have a good go at it. Working at 37°C, the first set of bacteria attacks the food-waste particles and converts them to soluble organics; another set then converts those into long-chain volatile fatty acids; a third bunch set to and break up the long chains to create acetic acid; and then a fourth lot go to work and turn the acetic acid into biogas, consisting of 60% methane and 40% carbon dioxide.
“All these bacteria live together and operate simultaneously and synergistically inside the one tank,” says David Woolgar, engineering director of Biogen Greenfinch.
The biogas may need traces of other gases removed, but essentially it’s ready to be used straight away in a conventional combined-heat-and-power gas engine to produce electricity and heat.