March 28, 2011 proved a defining day for Mark Stein, plant director at GM Manufacturing Luton, for which there are plans to rebrand as the Vauxhall Luton Plant. That date marked the point when the green light was finally given for work to start on the new Vivaro van.
The decision had been expected nine months earlier, placing Stein and everyone connected with the plant on tenterhooks to meet unrelenting targets. “That was the biggest challenge for us,” admits Stein. “To do whatever was necessary to win the new model. We had to keep all our score cards green and meet every objective and target.
“I have ‘four walls’ responsibility which, of course, includes all of the score cards we are measured against,” adds Stein. “This includes internal targets, warranty, cost, suggestions, attendance, training and employee engagement. The workforce kept delivering on the score cards right throughout the period when we thought we had passed all the deadlines for a positive decision.
“Our attendance is an industry benchmark. It is a good workforce, and one that is significantly smaller than it was. The plant is driven by performance metrics addressing, for instance, safety, people engagement, quality, cost and efficiency.”
One major benchmark is the time required to build a van – hours/van or HPV – and gross conversion rate (GCR). Stein does not discuss figures but bar charts on these and every other yardstick fill his office walls. HPV and GCR are very important; all he admits is “the plant is very competitive”.
“We punch above our weight,” he declares. “There is no Vauxhall/Opel plant building fewer vehicles. It is a low-investment, low-cost plant. We do not have the same automation as other plants. We must be more efficient with our people.”
One French plant has as many robots in general assembly as Luton has in its entire bodyshop.
Stein’s next target date is 6 January 2014. “That’s D-Day,” he says. “That’s when the first new X82 model – the next-generation Vivaro – goes down the production line at Luton. We run out the current Vivaro, X83, in December 2013.”
Over the next 30 months, General Motors is investing £175 million to bring new life to its aged Luton plant in readiness for the next-generation van, a joint development with Renault in France which has lead responsibility in design. A further £130 million will be spent by each company on vehicle engineering.
“In 2012 we will see early prototypes, and before then mule build. We have increased virtual build to minimise the number of prototypes,” explains Stein. “During 2013 we will go through various trial builds in parallel with the current model.”
But from 2014 until 2025 the plant will produce only Vauxhall and Opel vans; no longer, as now, will vehicles be built for Renault and Nissan. Renault will build its own version of X82 (the Trafic) at Sandouville, near Le Havre, where planned capacity will reach 100,000 a year.
This plant is much larger than Luton. Nissan’s Barcelona plant currently builds the H2, a high-roof version of the X83, but from 2014 Sandouville will build the next-generation H2 and will supply Vauxhall/Opel.
In another marked change from the present contract between GM and Renault, dating back to 2001, from 2014 Luton will build only diesel versions – no petrol models. And diesels will be smaller, as powerful and more fuel efficient. All Vivaros have front-wheel drive.
“We can now concentrate on our own company,” declares Stein. “Results are already showing through; the sales forecast for this year is rising steadily and we are aiming for 70,000 units. We are increasingly reliant on Vauxhall and Opel sales. But our UK sales team is leading the way in Europe in winning additional market share. This might be because we are building in the UK.
“The next 30 months will be important for the sales team. We have to bridge the gap – Vauxhall/Opel sales must increase because we will be building only these models.”
One of the first steps is to boost output and line speed. The plant runs at 20 jobs an hour but the plan is that this number will rise. The plant currently employs 1,500 directly – it was 2,000 when the factory ran on three shifts in 2007 and hit a record 95,030 units. Some 1,100 are Vauxhall employees and 400 are contractors and service providers.
Although the X82 is a co-owned development, Vauxhall/Opel has full responsibility for manufacturing strategy for Vauxhall/Opel products. And in this Vauxhall’s Commercial Vehicle Engineering Centre (CVEC) at Millbrook, Bedfordshire, plays a leading role. While the whole vehicle is a joint development between Renault and GM, with the French company responsible for base engineering of the vehicle, the task of implanting the Vauxhall/Opel DNA falls to engineers at the CVEC.
At the moment, only a handful of engineers are engaged in the task but gradually the team will build to 35 or so, most based in the UK.
Vauxhall’s engineering function is to liaise closely with GM engineers in Paris and Russelsheim, Germany, as well as teams at Renault in France. British engineers working in Paris are responsible, under the leadership of Craig Jones, head of vehicle engineering, for GM-specific items that differentiate the vehicle from its French counterpart.
According to Jones, this includes the front face of the vehicle, fascia and some elements of interior design. “GM’s German-based designers, led by Luton-born Malcolm Ward, both direct and create the unique differentiation,” says Jones. “Three members of my team work on the project in Paris while a further two in Millbrook are engaged in 3D data liaison and transfer.
“We have passed the advanced engineering stage and are moving into engineering execution. This will be followed by prototype and validation builds,” adds Jones. “The task of our engineers is to ensure that we can facilitate the vehicle in the Luton plant. We are responsible for releasing the vehicle using all the engineering information. This requires us to translate the entire technical content of the vehicle into GM systems to allow a bill of materials to be built. We are working very closely with GM manufacturing engineers in Germany and in Luton where the van will be built.
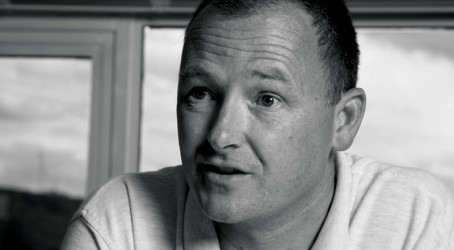
“Our current focus is to ensure the 3D data is available to allow virtual confirmation of the production methods using CAD data to make sure we can accommodate the new vehicle in the plant,” says Jones.
Although the current Vivaro was designed in 1997-99, and so is Euro 3-compliant, many aspects of vehicle design have evolved to meet legislative and customer demands. The vehicle will end life Euro 5-compliant, having had two major facelifts. The task of Jones and his team is to work with Renault to ensure that the new vehicle not only meets current requirements but future ones as well.
Stein meanwhile is responsible for what happens within his “four walls”. A major part of the investment will be in the bodyshop with new robots and fixtures; the rest will be split between the paint shop, press shop and final assembly.
Requests for quotations for new equipment such as robots (the current plant has 89 robots in the bodyshop) will go out in the coming months. There will be new assembly fixtures for underbody, bodysides and closure lines, and body framing.
Luton will continue to stamp large body parts using a blanking line and two presses; however, the oldest press dates from 1962, and could be replaced. The principal investment will be for new dies.
The paint shop remains a big investment. Some £700,000 was spent on it a year ago.
“We have 50 robots and we will carry forward the same process. We are extremely competitive in terms of paint quaity in the market with the current technology,” says Stein.
“The new model will need roughly the same floor footprint, though for a time we will have a common final line (for the X83 and X82) in the bodyshop where we will change over the unique tooling in between trial builds of batches,” he says, adding that the final layout has not yet been decided.
“We want to minimise investment, therefore we must reuse as much equipment as possible. We also want to improve efficiency. We have many lessons that we have learnt since the bodyshop was conceived 13 years ago, including access floors and the delivery of parts to the bodyshop. The bodyshop is the present bottleneck.” The bodyshop is spread over three floors.
“We will require a new turnaround area,” says Stein. “This is a temporary on-site space for the storage of components whilst we build new cells or lines in some areas. Once we switch over from X83 to X82, old cells will be dismantled and these areas used for storage.”
Although an old plant with a layout that sets some challenges, Luton is still efficient, having one of the lowest cost bases in Europe, according to Stein. And there are plans to boost integration on the site to increase the supplier footprint, even to create a supplier parc.
“Last year we brought in the outside supplier of longitudinals and cross-members,” says Stein. “It installed the whole of its assembly lines on our premises. Production of struts and corner assemblies has also been brought in.
“We are working with purchasing and global supply chain to increase the local supplier footprint for Vivaro,” says Stein. “If more vendors come on site, fantastic. We are looking to maximise manufacturing and supply work in the UK.”
The Luton plant will continue on two shifts to build more than 70,000 vans a year based on an uptime of 95% in assembly. That the plant performs so well is due in no small part to the maintenance teams.
And, for the first time in living memory, Luton is recruiting apprentices. The apprenticeship programme begins in September.