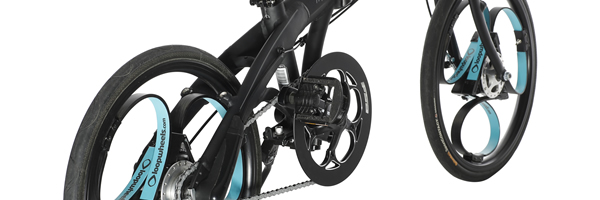
How would you go about reinventing the wheel? Industrial designer and mechanical engineer, Sam Pearce, knows how, as he has just done it. Here we find out more about the result: the remarkable loopwheels for folding commuter bicycles.
If like Institution President, Patrick Kniveton, you are looking for inspirational engineers or designers with a fascinating story to tell about their work in engineering, you would be hard pressed to find someone more intriguing than Sam Pearce. An engineer by training, he has a desire to make things cooler, and, to a soundtrack of Queens of the Stone Age, uses Lego then CAD to design his products. Oh, and he’s just reinvented the wheel.
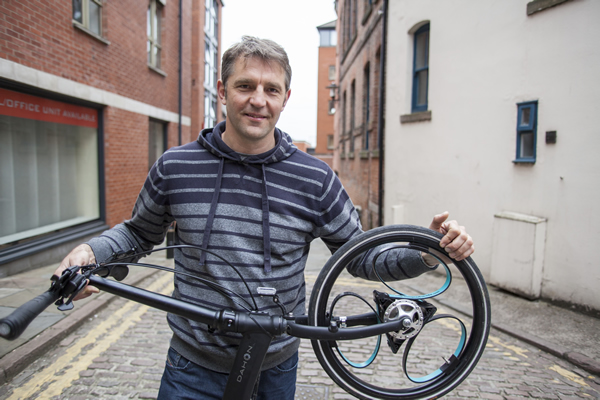
Sam’s invention, loopwheels, are a new type of wheel, initially for folding commuter bicycles, that have been designed to make cycling more comfortable. Loopwheels have suspension within the wheel itself: in place of rigid spokes, they have three loop-shaped springs. Loopwheels have a spring system between the hub and the rim of the wheel which provides suspension – cushioning the rider from bumps and potholes in the road. The springs also absorb road noise, reducing vibration through the frame and into the rider’s arms. Because of the suspension within the wheel, you can use high-pressure or puncture-resist tyres, eliminating the need to rely on fat tyres to cushion your ride.
The story behind the development of loopwheels is an interesting one, as Sam explains: “I invented and developed them at my home in Nottinghamshire. By training and profession, I am a mechanical engineer and industrial designer. By nature, I love making things: designing, building, doing. I love the way things are made, work and fit together. Above all, I love simplicity, and products that work well. I’ve got no time for unnecessary gimmicks, products that are complex to use, a lack of honesty. I am practical and hands-on. I am stubborn and don’t give up easily. When I believe in a product idea, I really believe in it. If it doesn’t work the first time, I keep at it, and keep at it, until trial and error gets the result. All useful traits when you find you’ve set out on a journey to reinvent the wheel.”
Sam first had the idea of a wheel with integral suspension in 2007. Having discovered his passion for industrial design while working with composite materials as a mechanical engineering finalist at Leeds University in the late 1980s, he went on to do a Masters in industrial design for engineers at Teesside University. He got his first job as a designer in 1993, for what was then a very new ‘keyhole surgery’ company Surgical Innovations. He worked for the London palm-top computer company Psion, before setting up his own industrial design consultancy Jelly Products. One of his first innovative design ideas was for a baby stroller. He patented a brand new compact folding mechanism which he sold to Dorel, the company behind Maxi Cosi and Quinny. Working with the R&D team at Quinny, they won awards for the baby stroller which he designed for them: the Quinny Yezz.
It was after a meeting with the team at Maxi Cosi, while sitting at Eindhoven airport waiting for a flight, that he first thought of the concept of a wheel with tangential suspension. He explains: “I saw a mother pushing her child in a buggy. The front wheels hit a slight kerb and the child jolted forward because of the impact. It had big suspension, but in the wrong direction. So, I asked myself why a wheel couldn’t have suspension inside it, so it would soften an impact from any direction. I sketched the idea in my notebook, got on my flight, and didn’t think much more about it for a couple of years.”
“In 2009, I still thought that this was a good idea, and on a spare Sunday afternoon, I thought that I would make a model in plywood and C-shaped guttering from B&Q. I rolled it across my finger, and it worked! I wondered how I was going to prove the concept, though, because I had to be able to verify it.”
“Because at that time, I was doing a lot of mountain biking, I decided to make prototype wheels for my bike and had a ride up the road. The springs were steel and you could hear me coming from a mile off. They worked OK, but those early prototypes didn’t really perform better than a spoked wheel. I knew that to be worth doing, the wheel had to be better than what was already available. It took many more attempts, and many more prototype wheels, to get to that point.”
When Sam reached that point, he filed a patent, and he was amazed to receive a report back with 15 quite similar patents from 1912-1917 – a time before the invention of the pneumatic tyre. Sam explained: “People had clearly had the idea of a wheel with suspension at the turn of the twentieth century, and had tried to invent ‘resilient wheels’, and I had to ask myself why these earlier inventions did not work when the loopwheel did.”
“I realized that while some of the early designs were right in theory, the inventors hadn’t been able to make them successfully because at that time, with no CAD and no carbon composites, none of the extant materials had the right properties.”
“I needed to make my springs from a material that was stiff yet flexible. Steel springs were no good. Having always worked with carbon composites from student days onwards, I felt that if I were to use them to make my springs, then I might begin to get the high level of performance needed for the wheel.”
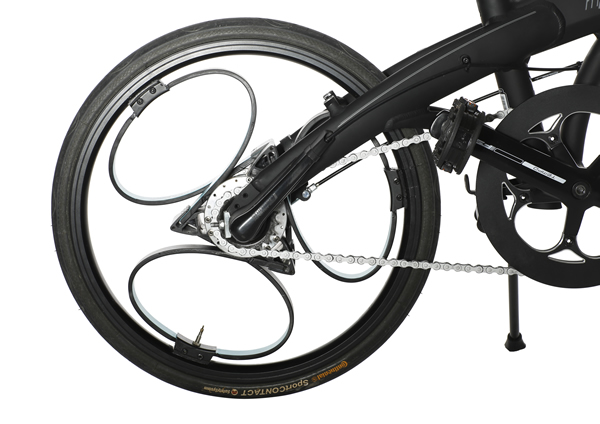
Sam believes passionately that engineers should never go to the same place for inspiration, but should take an expansive view of their environment and get ideas, even from what might appear the most unlikely of sources, in order to solve a problem. He said: “Give me CAD, music and Lego and magic happens. Listening to Radiohead and Queens of the Stone Age gives me inspiration. Brian Wilson, of the Beach Boys, said that when he was creating a melody, he could see the notes in the air and can grab them. I feel the same about design.”
“I was given a box of Technical Lego when I was 11, and I’ve been using it ever since to build all the models for mechanisms I’m working on. My children are not allowed to touch this Lego – though they’ve got lots of their own! I do a first sketch on paper, then build the Lego model, then go to the CAD station and create 3D CAD animation so that I can scroll through really quickly and see it moving. I have even built a curved wooden bridge in my house that I designed using CAD.”
“Going back to the loopwheels problem of how best to make the springs and thinking that carbon composites were going to be the answer, I took inspiration from my immediate environment. I live in an area of Nottinghamshire which was once Sherwood Forest, the home of Robin Hood, and at the end of my street there is an archery shop. One day I had the idea that carbon composite archery bows probably went through similar kinds of stresses as the springs in my wheels.”
Sam worked with a small local company, KG Archery, on the development of the springs for loopwheels. Currently, KG Archery is one of only two UK companies specialising in traditional expert craftsmanship. The Master Bowyer there, Keith Gascoigne, developed the world’s first all carbon bow handle in 1991, and his team was proud to take their expertise into new territory with loopwheels.
“The carbon composites for the springs were carefully developed and tested to give optimum compression and lateral stability as well as strength and durability,” Sam explained. “Specially-designed connectors attach the springs to the hub and rim. There are three springs in each wheel, which work together as a self-correcting system. The spring configuration allows for the torque to be transferred smoothly between the hub and the rim.”
“Front and rear loopwheels have different spring rates. Most of the weight of the rider is at the rear of the bicycle, so the rear loopwheel is stiffer. A front and rear loopwheel can be used together as a set, or you can use a single loopwheel alongside a conventional spoked wheel. Loopwheels provide suspension on a bike which has none, or can be fitted in addition to suspension forks. Either way, you get a smoother, more comfortable ride.”
It took at least 200 springs, 40 wheels, lots of riding, lots of crashes, and lots more riding, before Sam was fully satisfied that he had proved loopwheels. He tested and over-tested wheels on their longevity and strength before he felt ready to show them to the world. An experienced industrial designer, he was careful to operate under the radar in order to protect his intellectual property. Sam launched loopwheels in April 2013 at the hand-made bicycle show Bespoked Bristol and has since taken the wheels into production through a successful crowd-funding campaign on Kickstarter (www.kickstarter.com).
As more and more commuters choose folding bikes as a means of keeping fit or getting to work without resorting to public transport, loopwheels could well play a big part in making the daily commute a lot more comfortable. Most folding bikes have no suspension, because conventional systems add weight and bulk to the frame. So they tend to be useful and practical, but not always a joy to ride. Sam says: “Commuting should be fun. Comfort shouldn’t be buying a huge padded seat and wearing padded shorts, it should be solving the issues that cause this: the road. Removing the road vibration from the equation solves a lot of comfort issues, and that’s exactly what we’ve done with loopwheels.”
“Because the springs in loopwheels absorb shocks and isolate the rider from the vibration of the road (or road noise), one of the first things that new riders comment on is that they don’t experience the usual vibration through the frame and up their arms. So you’ll get less wrist and shoulder ache on long rides.”
“I’ve spoken to people who have ridden on loopwheels for the first time, and their comments are along the lines of: ‘Wow! This is fun,’ and ‘It’s like riding on a velvet cushion.’”
Sam is now selling Loopwheels via an e-commerce site, both as single wheels and ready fitted to a folding bicycle. Perhaps as might be expected from a new technology made in small numbers, prices are not cheap: a single front wheel is £360 and a folding bike fitted with a front and rear loopwheel retails at £1,400. To date, Sam has had more orders for export than from consumers in the UK.
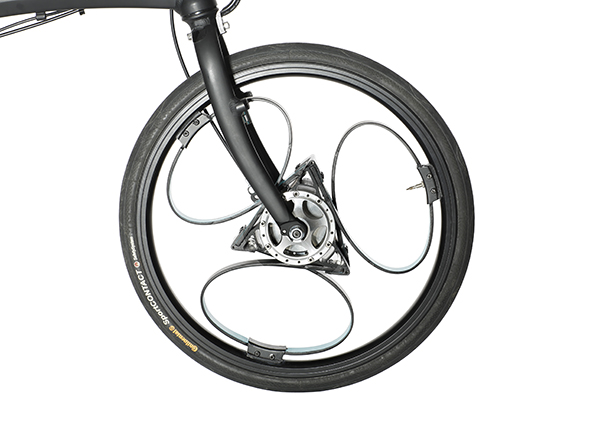
Because of the way the wheels work, not every 20” wheeled folding bike is suitable for his Loopwheels. Sam explained: “You need 50mm space between the outer edge of the tyre and any part of the frame to give enough clearance for the movement from the hub. There wouldn’t be enough space on a Brompton without the wheel rubbing against the frame for example (and anyway, Bromptons have smaller wheels, at 16”). However, some of the world’s biggest selling folding bikes such as many of the Dahon and Tern models are suitable, or can be easily adapted for Loopwheels by replacing the front fork with a wider one.”
Sam is already working on some new variants of Loopwheels, but he’s coy about saying too much as yet: “Straight away people asked me about a 26” Loopwheel, which is the standard size for most bikes, but I’ve also found there’s a real demand for suspension on recumbent bicycles and trikes. I’ve always believed there’s huge potential for my wheel to be used on other vehicles, as well as bicycles. But for now I need to focus on doing one thing well, rather than getting too distracted into lots of interesting projects.”
Passionate about craftsmanship and in the skills and knowledge that come from practical experience, Sam said: “We believe in taking pride in making things by our own hands, which is the literal meaning of manufacturing. So we make loopwheels ourselves, by hand, in Nottinghamshire. We can’t claim that every component of a loopwheel is local or British, though perhaps we’ll get there one day. But we are proud that the springs are made just a few miles from where the loopwheel was invented, and that we assemble our wheels in Nottinghamshire too. We care about nurturing creativity, our engineering skills, and manufacturing. We are not nostalgic or sentimental about it: we just believe in making and doing, and making and doing it well.”
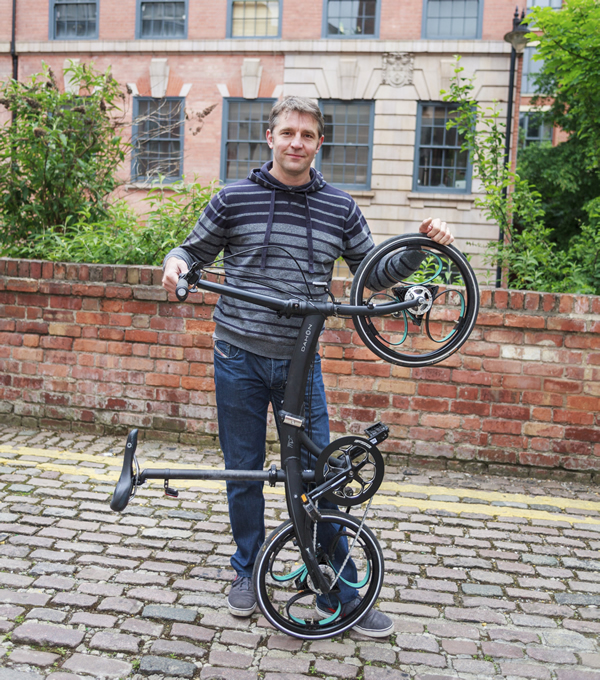
Smiling, he said: “I know that ‘reinventing the wheel’ is a bit of a joke. But that’s just what we’ve done. And when you ride on loopwheels, you’ll wonder why no one did it sooner.”
For more information about loopwheels, please visit www.loopwheels.com
Photography of Sam Pearce by Andrew Smith of Full Phat Design