The small Lancashire town of Leyland has seen plenty of industrial development. Agricultural equipment and steam-powered machines were being made there in the twilight years of the 19th century, and, in the 21st, manufacturing continues to take place at Leyland Trucks.
You’ve probably heard of Leyland Trucks – whether as part of the nationalised conglomerate of British Leyland, or on its own. But you might not necessarily imagine that the company was still assembling trucks in the North West, having endured what might be viewed as a turbulent recent history, including its parent company, DAF, going into receivership and a management buy-out, before the acquisition of the firm by US group Paccar in 1998.
Paccar, which now owns DAF and the leading American truck brands Peterbilt and Kenworth, seems to have provided Leyland Trucks with a measure of stability. “It’s a capital-intensive and prosperous company,” says Denis Culloty, chief engineer at Leyland. “We very much need its support to sponsor some of our major new truck projects.”
Having a profitable parent does help. Paccar is said to have made a profit for every one of the past 73 years. Even during the recession, when automotive companies endured a torrid time, this record was maintained although the margins were eroded. “In the automotive industry we think our record is unique, certainly in the truck business, but also in the sector more generally,” says Culloty.
Leyland Trucks now operates out of a one million ft2 factory in the town. The company has 1,000 employees, 100 of whom are design engineers. It designed the LF truck at Leyland, which assembles the LF, CF and XF models. All these trucks are branded DAF – further adding to Leyland’s opaqueness. DAF-branded trucks enjoy a market share in Europe of about 25%, putting them third among heavy-duty truck makes on the Continent, behind Daimler and Volvo.
It’s been a turnaround, says Culloty. “We were bottom of the heap in 1999 and now we’re running at third. We are also a centre of excellence for truck manufacturing within the Paccar group.” This has been recognised by the Institution of Mechanical Engineers, which made Leyland Trucks the only firm to win successive overall Manufacturing Excellence awards.
Volumes of Leyland-built trucks dropped off during the worst year of recession in 2009. But they enjoyed a boom year in 2008, when a second shift was added for six months at the factory. Recently there has been a recovery from recession, but the economic outlook remains fragile. This hasn’t stopped the company introducing new models, however, with a series of projects backed by the Technology Strategy Board (TSB) having helped deliver to market a diesel-hybrid truck, and the development of a prototype all-electric truck.
The LF hybrid went on sale in December 2010 and is a 12-tonne parallel hybrid truck with a 44kW electric motor between the engine and six-speed automated manual transmission. Although hybrid trucks are quite common in the US, where incentives in eco-conscious states such as California are accelerating their development, the hybrid LF, claims Leyland, was the first of its type in Europe.
The truck is a self-contained diesel-electric hybrid, which means it generates electricity by recovering energy during braking and cannot be plugged in. Rob Lawton, engineering project management at Leyland Trucks, says: “It can drive as a pure diesel truck, or it can drive in what we call blended torque mode, which is a combination of diesel power and electric power, and electric vehicle mode. But even in this last, the engine is still used idling to power auxiliaries such as compressors and power steering.”
The energy generated by braking is converted by an inverter from AC current to DC and stored in the LF hybrid’s lithium-ion batteries. The environmental and fuel economy benefits are pronounced, says Lawton. “Clearly, the LF hybrid has lower carbon emissions and lower fuel consumption. We have seen fuel savings in the range of 11-24%. We have proven fuel savings and, added to that, the truck is easy enough to drive. To get the full benefit, it should be driven on a stop-start cycle, because it regenerates the energy you use in braking. If you stick on a motorway, it drives like an ordinary diesel truck and you wouldn’t notice any difference. But for driving in cities like London and Manchester, it’s ideal.” Leyland Trucks has also worked on a second-generation hybrid with TSB backing, which features a 75kW motor, electrification of all auxiliaries so the engine can be turned off completely in EV mode, and much bigger energy storage.
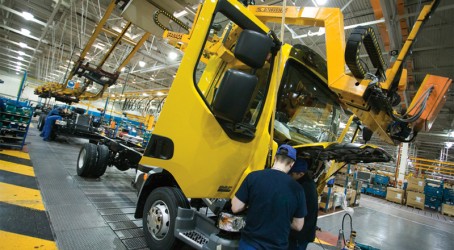
The trend towards increasing urbanisation and the growth of cities, as well as concerns over climate change, will help to make the electric or hybrid diesel-electric truck a more common sight on our streets, just as is happening with passenger cars, Lawton believes. “The development of megacities – with more than 10 million people – will change transportation. Freight will be going into the cities, but there will be issues of traffic, air quality, and, of course, climate change. It’s possible to see more and more city centres becoming limited-access. But if you have all-electric vehicles, you deal with emissions, smog and noise,” he says.
None of this will take place if the eco-friendly trucks aren’t economic to run, says Lawton. “If the customer can’t make money out of it, it doesn’t matter how good the technology is – he isn’t going to buy it. So we need to make trucks that are nicer to drive, enhance their performance, make them cheaper to operate by saving fuel, reduce their maintenance costs, and ensure they have a higher resell value.” Work must also be done to maximise the payload available to operators.
Governments should incentivise firms to use hybrid and electric trucks, he adds. For instance, legislation such as London’s congestion charge has favoured passenger EVs but lagged on creating incentives for trucks. The London Low Emission Zone could be tweaked to allow hybrid or electric trucks in, says Lawton. “If not, we’re not going to sell these trucks in huge numbers. It’s a chicken-and-egg situation at the moment. We can’t get cost down because volumes aren’t enough.”
The electric truck developed with the help of the TSB is based on a 12-tonne LF chassis and carries a payload of 7-8 tonnes. The diesel driveline was removed, apart from the rear axle, and a 150kW permanent magnet traction motor installed. The truck features a single-speed transmission, because the electric motor has peak torque at zero rpm, and because top speed is limited to 50mph, which also improves energy efficiency. The vehicle carries 100kW of lithium-ion batteries, with the potential to extend this to 130kW. Unlike the hybrid, the auxiliaries are driven electrically. The vehicle can be plugged in to a three-phase supply to recharge.
The electric truck has been extensively tested at Millbrook, which Lawton believes may have dispelled some of the myths about such vehicles. “We wanted to understand why some of the early-generation trucks had some deficiencies in driveability, not being able to go up hills effectively, for example. What we found is they have quite inconsistent motor output performance, based on temperature. When they got warm, the output dropped. What we proved with this project is that there doesn’t necessarily need to be a problem with electric trucks. With the right motor technology, you don’t have those issues.”
The TSB has provided 50% of the funding for each project. John Laughlin, programme manager, low-carbon vehicles at the TSB, says: “From our perspective, this allows innovation to happen because we de-risk it. Rob could do a business case to develop an electric truck and be told ‘no’ because it is too much money, too much risk. Even in a downturn, if you’re innovating, you stand a chance of making a step change commercially, not just technically. It’s important in a downturn that there is the option to de-risk the technology.”
Some of the benefit that Leyland Trucks has gained in working on cutting-edge projects has also been felt by its major suppliers in the UK. “The TSB does a good job in stimulating the right areas of research in Britain,” says Lawton. Dealing with the board also compares favourably with dealing with certain government departments, he adds.
The development of eco-friendly trucks is likely to be a tortuous process. For example, you would need 28 tonnes of lithium-ion batteries to store the same energy as in a 400-litre tank of diesel. But programmes such as that initiated at Leyland Trucks with the help of the TSB are at least helping to get the ball rolling. “They drive the agenda at points in your business: here is the funding, here is the enabler,” says Lawton.
“The end result is that, with your suppliers, it forces the development of UK plc.”