Nick Kimber’s “office” is a very strange place indeed. At first glance it looks like an Olympic-sized swimming pool, stretching as it does for more than 100m into the distance. But in the centre of the water there is an enormous mechanical arm that rotates at a thunderous speed. It really is the oddest of working environments.
But this mysterious water-world is where Kimber evidently feels at home. For the past 20 years he has worked at the Haslar hydrodynamics facility at Gosport in Hampshire, evaluating the performance of model ships to predict how full-scale vessels will fare when they go for sea trials. He is currently responsible for the control and data-logging systems used in all the free-running ship and submarine models tested in the Haslar basin. And it’s a job that clearly gives him an immense amount of enjoyment and pride.
“For me the job is all about getting my hands wet, helping to ensure that all the required experiments are carried out as they are meant to be,” he says. “It’s a role that involves a real team effort. If there is a piece of information that we need to get, then the scientists and engineers work closely together to get the submarine models to do what we want. And then we have to ensure that all the data is logged and delivered back poolside so that it can be analysed. It can be a real technical challenge.”
The Haslar hydrodynamics facility, owned and run by defence group Qinetiq, provides advice and support on submarine manoeuvring and control to the sea systems group and the in-service submarines project team at the Ministry of Defence’s Abbey Wood site in Bristol. This information, in turn, enables the MoD to provide safety assurance and operational guidance to the submarine command teams.
Haslar is responsible for maintaining the mathematical models of all in-service submarines and is able to simulate responses to a range of emergency manoeuvres, establishing how a vessel would perform under scenarios such as hydroplane failure or flooding. So it’s crucial that its work is accurate.
The mathematical models originate from physical experiments using towed vessels in the ocean basin, with validation coming from free-running model experiments, backed up by full-scale trials where possible. The experiments enable Kimber and his team to refine hull designs to reduce resistance, as well as to predict how the vessel will perform when it is built and starts to undergo its sea trials.“
Some aspects of our work are to do with refinement of design, such as improving flow over the hull,” he says. “But it’s more about understanding how a ship manoeuvres and handles. For that, we do model tests before they are built, so there are no surprises. There’s a long history with model testing and correlation with full-scale test results. We can usually satisfy ourselves and our customers that the boat should perform well.”
Towed testing in the ship tank sees the models pulled along under specific conditions such as a particular attitude or rudder angle. This enables the measurement of force. Parameters such as yaw or pitch can then be varied, enabling the effects of individual components to be separated out. This work, carried out over many weeks, is how the mathematical models are built-up.
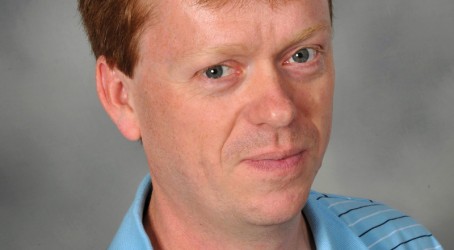
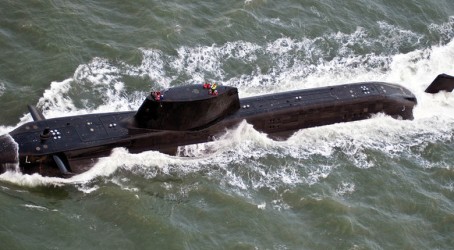
Free-running models, on the other hand, are capable of autonomous operation, making it possible to see how the vessel actually performs, and so offering a more accurate representation of what will happen at sea. The free-running model at Haslar is capable of diving to depths of up to 30m and is bristling with a host of high-tech equipment including 58V lithium-ion batteries, a 2kW propulsion motor, control surface servos, pressure-depth transducers, ring-laser gyroscopes and a Doppler velocity log.
Central to its function is the control system, which is required to gather data from the on-board devices, at various rates, and to log that data synchronously. The control system must log data to an internal file when requested, act on external commands and return the data poolside when instructed via an antenna on the bridge. All this functionality has to be achieved in the tightest of spaces.
With the submarine model being 25 years old, its on-board computer systems have been upgraded several times but they were still becoming outdated, says Kimber. “We were starting to struggle with processing power and we were having trouble communicating with the model. So we decided to give the submarine model a complete overhaul, including a new control system,” he says.
Instead of opting for a bespoke control system, as had always previously been the case, an off-the-shelf modular design from National Instruments called Compact-Rio (Crio) was selected. The device promised several major advantages including standard networking interfaces and expandable architecture where extra channels and I/O types could be added as required.
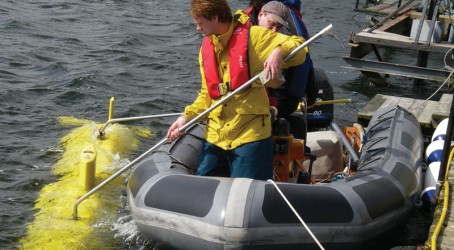
Kimber says that modularity was an important consideration. “The Crio unit itself is quite small and sits comfortably inside the model’s anodised aluminium hull. Attached to it is a rack where we slot in different cards comprising analogue inputs or outputs, digital inputs or serial ports. We slot in whatever card we need for the application and build up the control system in that manner.
“For our immediate work we had a predefined list of what we wanted. But since then we have found that we can use the Crio on other experiments simply by changing the slot-in cartridges for different purposes.”
The Crio unit is the heart of the submarine model, linking to components such as rudders and hydroplanes, propulsion motor, depth transducers, leak detectors and wireless router. The unit logs data from the experiments on to an internal flash memory card. This information is relayed poolside by wi-fi link once the model has surfaced. Kimber says the flow of information is quick, typically 20 seconds per run.
“The upgraded control system using Crio technology has proved to be extremely reliable,” he says. “The transfer of data from the model happens quickly, so that we can start working on the data almost as soon as it has been logged.
“The system has also been highly reliable, which is impressive bearing in mind that the model is in and out of the water.”
Operating and analysing the submarine model requires the contribution of mechanical, electrical and software engineers. Kimber says he loves the multidisciplinary aspect of the role. He also enjoys the fact that hydrodynamics continues to throw up surprises. “I’m still fascinated by the hydrodynamics aspects of how a submarine behaves. It’s a long-standing and well-studied field but there are still some mysteries. The more we study it the more we think ‘why did that happen?’ or ‘how could we improve that?’.
“When it comes to full-scale sea trials, we measure how the boat performs and correlate it back to how we said it would behave. If we get that right there is a real sense of pride – we say ‘I knew it would do that’. Most of the time it is exactly how we expected it to be – but occasionally some data comes back not quite as we would have thought. It is those bits of data that we refocus on, going all the way back and correcting our predictions.”
Crio was originally chosen purely for the submarine work at Haslar. But it is now also being used for free-running surface-ship modelling to measure sea-keeping and roll stabilisation, and for high-frequency data logging (~5kHz) for slamming events. And in the near future it will be used for model testing of the Successor nuclear deterrent fleet.
“That work will take place in the next couple of years,” he says. “We have already bought the Crio unit for Successor and it will have a faster processor and more memory.”