Cambridge is given its unique character by the strength and reputation of its university. Even on a grey day, with the rain lashing down, tourists mill around the streets in their droves, visibly awestruck by the imposing colleges and well-kept courtyards that are dotted liberally around the city.
You might expect the head of the engineering department at such an august institution to exude an air of scholarly seriousness befitting their seniority. But Professor Dame Ann Dowling is happy to break the mould – she’s far more likely to be wearing a radiant smile. And it doesn’t take long to discover the reason for her seemingly perpetual good mood.
“Who wouldn’t want to work at a place like the University of Cambridge?” she asks. “I’m heading up one of the best engineering departments in the world. That means I get to work with some wonderfully talented people carrying out some amazing research. And our collaborative engagement with industry means we get to work on projects that can make a real difference in a commercial setting. It really is a fantastic job to have.”
Dowling’s elevation to the role of head of the department of engineering at the University of Cambridge is the latest chapter in a glittering career which sees her widely acknowledged as one of the world’s most respected authorities in the fields of combustion, acoustics and vibration. Mathematics was her first love, having studied the subject as an undergraduate at Cambridge in the 1970s. But a summer job at the Royal Aircraft Establishment in Farnborough researching aircraft noise helped her identify what was to become her area of specialisation.
“I was at the Royal Aircraft Establishment for two summers and my experiences there helped crystallise what I wanted to do,” she says. “Concorde was carrying out its proving flights and noise had become the issue that would decide whether or not it would be allowed into the US. A whole new field was opening up in front of me. In some areas you can study very hard and only make a small change – but here there was a whole ‘order one’ effect to be found. It was an exciting time that proved crucial in the development of aviation.”
Dowling returned to Cambridge enthused by her experiences at the Royal Aircraft Establishment, immediately switching from mathematics to the engineering department to carry out a PhD in aircraft noise. Her supervisor was part of the Concorde noise task force, and with his guidance she began researching aircraft noise at higher speeds, carrying out fundamental research into the modelling of jet noise and how higher-speed motion affected noise sources. The work showed that it was a more complex relationship than originally thought and that unexpected effects were coming into play. “Previously people had talked about it purely in terms of a Doppler shift,” she says. “But there was more than that going on, there was actually a change in the character of the noise source as well. I wouldn’t say my PhD work solved the problem of aircraft noise at higher speed, but it did go to show that a whole new effect came into being when aircraft moved faster.”
Concorde eventually gained the required acceptances for entry into the US and Dowling’s role in the successful outcome hadn’t gone unnoticed. She was subsequently asked by the Ministry of Defence to expand her research into the area of submarine noise. At that time the next generation of Royal Navy submarines were expected to move through the water listening to very distant passive sounds, while actually existing in an extremely noisy underwater environment characterised by turbulent flow. That environment resulted in pressure fluctuations which were much louder than the distant sounds being listened for. So Dowling was asked to work on ways to model that phenomenon and then to develop compliant flexible coatings that would reduce certain aspects of noise. The modelling work she carried out was passed on to the Royal Navy and eventually shared with the US military through a technology exchange.
“However, I had to wait a long time to see the fruition of my work, as it had been applied strictly on a need-to-know basis,” she recalls. “It was actually some 15 to 20 years later, when I was serving on a promotion board for the Defence Evaluation and Research Agency, that I saw more details of the benefits that my research in this area was bringing. Compliant coatings had found their way onto submarines without me knowing the details of their use. It was rather nice to discover that, albeit after such a long time.”
These successes provided the foundation for Dowling’s career. She quickly went on to form a very successful relationship with Rolls-Royce, helping the company to solve the problem of instability of jet engine afterburners which comprised an interaction between acoustics and combustion. If the combustion was unsteady, sound waves would be generated, which reflected off the ends of the afterburner duct, interacting with the returning sound waves, and potentially leading to a phased relationship that could produce oscillations that would grow in amplitude. Rolls-Royce didn’t have the models to understand when the phenomenon might occur and how to eliminate it.
Dowling’s work homed in on the interaction between the oncoming flow perturbations in the combustion and found ways of characterising that. An afterburner rig with a small cross-section was developed to test an active control technology that could be used to manage the instability. The success of the technology encouraged Rolls-Royce to go straight from the laboratory rig to full-scale demonstration using an afterburner on an RB199 engine.
“The active control technology worked very convincingly but, because it was a joint Rolls-Royce/Ministry of Defence experiment carried out using a military engine, the work was quickly classified for the best part of 10 years,” says Dowling. “During that time I couldn’t talk about it being applied on a larger scale. I’d go to conferences in America and I’d hear people say ‘yes, it works in a laboratory, but it will never work at full scale’, and I’d have to keep quiet. Eventually active control was applied in gas power stations which were also suffering from instability problems.”
Perhaps the highest-profile research project that Dowling has been involved with was the Silent Aircraft initiative, a collaboration between the University of Cambridge and the Massachusetts Institute of Technology in the US. The initiative, established in 2003, had the ambitious aim of developing a conceptual design for an aircraft whose noise would be almost imperceptible outside the perimeter of a daytime urban airport. The design was to address the aircraft “generation after next”, employing medium-term technologies that would enable the concept to be a reality by 2030.
“We really wanted to make a difference – not just shaving a few decibels off – but to reduce aircraft noise down to background levels in an urban environment,” recalls Dowling. “We were keen to collaborate because we wanted to know the ultimate limit of what could be achieved.”
The Silent Aircraft initiative grew in status to attract some of the finest aerospace engineering brains from around the world and included companies and organisations such as Boeing, Cranfield University, Lufthansa, Marshall Aerospace and Rolls-Royce. The result, after several years’ work, was a conceptual blended-wing design that the partners said would be 25dB quieter than any commercial aircraft then in service. The findings have since fed into a Boeing blended-wing demonstrator.
“The airframe team came up with a different kind of aerodynamic profile on the centre body of the blended-wing design,” says Dowling. “The problem with blended-wing bodies had always been that to get a really good lift-to-drag ratio there needed to be tail-less design, but that brought into play the problem of how to do pitch control. Boeing had a blended-wing body design which was putting some downward force at the back but, because there was no tail, it required quite large forces to get the nose up.
“Instead our design had a chin – an indentation in the centre at the front that brought the lift forward. So we got the required ‘moment’ by having more lift at the front rather than needing a downward force at the back. These kinds of carvings had been used before to move the lift distribution around on wings but using it for a blended-wing body was new. “That gave us a design that had a higher lift-to-drag ratio than the Boeing blended-wing body aircraft. Initially Boeing didn’t believe it. So it took our airframe and carried out the work using its own in-house CFD. Boeing worked away with intensive calculations and came up with the same results as we had. So Boeing switched designs and it is currently working with Nasa doing wind-tunnel testing on our airframe. That was a great result.”
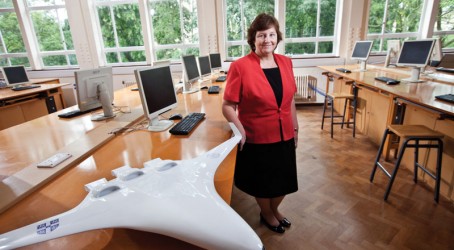
Some of the engine technologies developed on the Silent Aircraft initiative looked ambitious at the time. The project developed the idea of variable area nozzles so that it was possible to have a low-speed jet with low noise near the ground, which could be retuned in flight, closing the nozzle to allow the engine to operate at optimum efficiency. Such technologies are now being considered for nearer-term engines that would not require a whole new airframe. The Silent Aircraft initiative also pushed forward knowledge in the area of boundary layer ingestion – reducing the size of the wake by taking some of the boundary layer through the engine. Nasa now has a sizeable research funding programme in that area.
Looking back, the Silent Aircraft initiative showed the real potential of blended-wing bodies, says Dowling. But in the end the commercialisation of the technology comes down to finance. “No one ever made money out of developing a new airframe,” she says. “So it’s hard to see that there is a commercial case for an air-framer to go to a blended-wing body unless someone else foots the bill.
“Of course, blended-wing bodies do have tremendous potential for military transport applications. You’ve got this huge empty volume inside where you could put tanks or large troop numbers, but I think realistically it relies on some other source of funding to see it go forward. Boeing has said that if it gets a defence contract for a transporter it could do it in seven years.”
One of the aspects of the Silent Aircraft initiative that really pleased Dowling was the way that it encouraged integrated thinking using multidisciplinary teams. That has fed into her thinking on current research programmes as part of her new role as head of engineering at Cambridge. For example, Dowling is currently taking the lead in a collaboration in the area of energy-efficient cities, taking an integrated look at buildings and building technologies, transport, distributed power generation, urban planning and design. The aim is to look at ways of producing a city development plan that assesses the true impact on the environment and the well-being of people who live in it.
“It’s a big aspiration but we have a lot of people involved on it and we have been able to get funding and some additional academic staff posts in transport and building technologies, urban planning and architecture,” says Dowling. “I’m interested in how we can pull people together to take that sort of joined-up approach. Where Cambridge is unique is with its ability to join up across different branches of engineering, acting as a hub to bring in other disciplines as appropriate.”
Dowling’s position as head of the department of engineering at the University of Cambridge means that she inevitably has less time for her own research activities these days. But she remains very engaged with what’s going on within the department, both research and teaching. She is proud of Cambridge’s reputation as having one of the best engineering departments in the world, and is determined to enhance it further.
“We are looking at ways of engaging with industry in a slightly more strategic fashion,” she says. “We’ve always had good collaborations with industry but on occasion they have been a little bit piecemeal. We are now getting industry partners around a table to address some of the really big issues in their businesses and to look at innovative ways of solving problems. What’s great is that such an approach means that everybody spurs on everybody else, so the academics and the industrialists really enjoy the discussions that come out of it.”
Professor Dame Ann Dowling’s career
Ann Dowling is head of the department of engineering at the University of Cambridge where she is professor of mechanical engineering. She also chairs the University Gas Turbine Partnership with Rolls-Royce.
She has held visiting posts at Massachusetts Institute of Technology (MIT) and Caltech in the US. Dowling’s research is primarily in the fields of combustion, acoustics and vibration and is aimed, in particular, at low-emission combustion and quiet vehicles. She was UK leader of the Silent Aircraft initiative, a collaboration between Cambridge and MIT which resulted in the conceptual design of an ultra-low noise and fuel-efficient aircraft, the SAX40.
Dowling is a fellow of the Royal Society and a fellow of the Royal Academy of Engineering (where she was vice-president in 1999-2002). She is a foreign associate member of the US National Academy of Engineering and of the French Academy of Sciences. She has served on a number of industry and government advisory committees, and chaired the Royal Society/Royal Academy of Engineering study on nanotechnology. In 2008 she chaired the engineering panel of the UK Research Assessment Exercise. She was appointed CBE for services to mechanical engineering in 2002, DBE for services to science in 2007, and received an honorary ScD from Trinity College Dublin in 2008.
- List of some of Professor Dowling's recent publications.