What does Blatchford do?
Blatchford designs, engineers, manufactures, makes and fits assistive products (devices) such as artificial limbs (prostheses), splints (orthoses) and special seating for people with physical disabilities.
The devices we make are fitted to people who have lost a limb or physical function. The devices must meet the needs of users, be technically sound, designed for manufacture, safe for the user, of highest quality and reliability, economically affordable for payers such as the NHS and commercially viable for the company.
What are the key innovations of Blatchford?
The company’s deep understanding of the underlying science of locomotion is key to our success. The ability of Blatchford’s multi-disciplinary engineering team to focus on a project where manufacturing and quality engineers have the same say on product development life cycle as design engineers, in a flexible, fast-responding environment, provides a higher degree of agility to spot opportunities and use them to deliver robust solutions. Our Germany, Iceland and US-based competitors are similar or much larger in size. However, we have the advantage of 126 years of experience in practising innovation.
We also have the key advantage of being a product and service supplier contracted to the NHS and Ministry of Defence, which our competitors lack. Looking after 25,000 amputees and patients in the UK and Norway means we have direct access to users, a clearer picture of their needs, and over 250 clinicians as part of our development team. This unique capability compensates for a lower level of resources, enabling us to come up with unique ideas and concepts that users really want and find of benefit.
Having the right measures or indicators to validate our ideas in terms of comfort and increasing confidence by the user is key. We translate these key performance indicators in the use of our devices by measuring stability, gait symmetry and physiological energy consumption. We measure the interface pressures to redistribute forces and provide a means of energy absorption, and return to enhance comfort. At the two extremes of verification, if we do not get an almost immediate ‘Wow!’ from the user, we have learned that there is no point pursuing an idea further. Equally, if we cannot demonstrate we have reduced the risk of falls, or reduced severe low back pain, or excessive load on the sound limb joints and reduced risk of ulcerations, the buyers will not pay for such a device.
What are the key challenges for the company?
We have an established team of great research & development engineers, who have successfully implemented into production over 30 products in one decade. We have been raising the standard of care in our industry through innovation, while working with our competitors in setting standards for safeguarding the quality of care through the regulatory framework.
The pace of technological evolution is very rapid and we need to adapt and adjust to remain one step ahead. Induction of new talented staff into our highly specialised industry takes an average of five years, with an average product development cycle of over two years (due to the need for safety testing and clinical evaluation, as well as establishing evidence of clinical benefit). Recruitment, retention of passionate talent and their induction into our business, are key factors for our future progress.
Like many industries in the south-east of England, we face shortages of talented staff. We heavily rely on European engineers and technicians.
Most of our staff remain in this field for their career, and as the only remaining UK manufacturer of artificial lower limbs, it is imperative we address the issue of educating the talented future staff we need. So far we have been fortunate, through close links with local universities, to induct, excite and then recruit a number of talented young postgraduates, and ensure they enjoy their work through enabling creativity and problem solving. I am confident that most engineers, once exposed to the satisfaction that is gained from working in this field, would not find any other engineering role as satisfying. Long term, improving lives and finding solutions to help amputees and patients for an entire lifetime is likely to be even more satisfying than landing a 5-ton vehicle on Mars.
Watch some of Blatchford's innovative designs in action
How many engineers does Blatchford employ?
We have a number of manufacturing engineers, who specialise in advanced manufacturing, and material engineers as well as quality engineers. Our clinicians in Scandinavia are known as orthopaedic engineers. We spend 10% of our product revenue on R&D and that enables us to have a team of over 30 dedicated research and design engineers, as well as technicians, pre-production detailed design engineers and material scientists.
Our team of biomedical engineers has grown and we rapidly convert our mechanical, material, electronic, control and mechatronic design engineers into biomedical engineers within their first project. Our head/principal (equivalent to senior manager) role reviews projects as well as mentoring seniors. In turn, juniors who join our team are inducted into mentoring. The Technical Director role is at Board level, to support the heads, provide technical strategy and direction.
Do you think we do enough to promote engineering and science in the UK?
As a member of the biomedical engineering panel and a Fellow of the Royal Academy, I think we can do more. We are constantly looking at ways to ensure Government policymakers understand the importance of engineering. We heard at the MacRobert award ceremony from the Royal Academy of Engineering, that whatever God did not create was created by engineers.
The new Government Department for Business, Energy and Industrial Strategy is good news, however, we must ensure all stakeholders, all institutions and academia join forces to ensure clear communication of the importance of engineering in the creation of wealth through adding value. Without it, we will all be poorer and our well-being will be at risk as our population ages.
We are highly dependent on society better understanding the role of engineers. I feel after 40 plus years I am still advocating the same message. Part of the problem is communication, as we engineers constantly think of everything as a system, and live and breathe the inter-relation in all the everyday tasks that we carry out, from discovery, research, ideation, design, engineering products, production implementation and post-market surveillance. We sometimes think everyone thinks the same, as we speak the same language, and I believe that is not the case. Engineering leadership is about self-confidence, and the ability to help others understand the intertwined and interrelated multi-faceted discipline and task every engineer considers as a system.
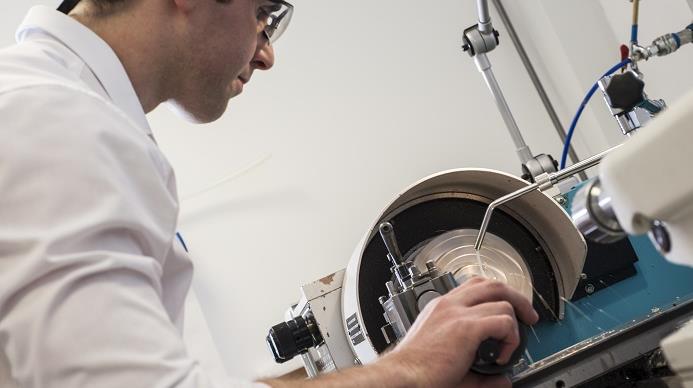
Do you believe the UK provides a good environment for science and engineering companies?
It is interesting that in Germany, China, Korea and Japan, engineers are sent to the UK for training in creativity. London has a large number of design houses, as well as engineering and science research facilities, it is a global centre of engineering animation and everyone talks about growth through culture of innovation, yet we all still ask the same question, ‘Why we are not as successful as Germany, and Japan?’
One of the key aspects of UK culture is education. I was sent by my parents at the age of 16 to the UK to be educated. However, we need to have a long-term industrial strategy, or closer integration of industry and academia with engineering innovation and system thinking at its heart.
We want to look at medical devices, but we mix it up with pharmaceuticals, and end up governed by larger organisational agendas. We need many role models from successful SMEs, and a large number of entrepreneurs who through partnership make the mass of scale that is needed to compete with larger companies. ‘Small is beautiful’ does carry a message of agility and flexibility to spot the next opportunity, and identify the next unmet need.
There are plenty of needs and there is a need to invest more in R&D, perhaps through larger tax incentives and R&D rebate. Allocation of funds for technology innovation growth could perhaps be managed by bodies outside Government, to attract global talent and consortia. This is vital, with the increasing complexity of engineering solutions for the future as we approach the fourth and fifth industrial revolutions in robotics, additive manufacture and artificial intelligence that will be with us in all our products in the coming years.
Do you believe Government should invest more in product development, or that this should be left to private capital investment?
Having worked in academia, the health service and private sector industry, the one common trend is sustainability. The experiences of the past have shown that the most sustainable product development is through industry. Private firms have shown good results and private capital investment with a long horizon beyond five to ten years could see long-lasting effective return. Healthy competition and regulation for environmental safety and the circular economy, thereby creating a level playing field and effective policing (the other key UK cultural aspect is law) by Government, is essential.
What does innovation mean to you?
When we do something new, and the user says ‘Wow!’ – that is innovation.
Professor Saeed Zahedi OBE is Technical Director at Blatchford. He completed a mechanical engineering degree in London before completing a postgraduate degree in bioengineering in Glasgow. He became a Fellow of IMechE after developing the first commercial microprocessor-controlled artificial limb and received the OBE for services to the prosthetic industry in 2000. He is also a Fellow of the Royal Academy of Engineering, and a Royal Designer for Industry.
To find out more visit the Blatchford website.
To watch more visit the Blatchford YouTube Channel.