A heavily modified Trent engine demonstrator with no fan blades is starting to excite engineers at Rolls-Royce as they look to develop the next generation of civil aerospace gas turbines.
The engine is being put through its paces at Rolls-Royce’s test facility in Bristol and so far has delivered no show-stoppers that would prevent further evaluation. Indeed, the engineers involved on the project are so confident about the potential of the so-called environmentally friendly engine (EFE) that an extended period of cyclic testing will start in the second half of the year as part of the technology proving process.
David Cross, chief project engineer for EFE, says the engine demonstrator could play a crucial role in helping Rolls-Royce to reduce the environmental impact of its products. “Carbon dioxide output is proportional to specific fuel consumption and there are two levers to reduce this in a gas turbine, either improving the propulsive efficiency or the thermal efficiency of the engine,” he says.
“Improvements in propulsive efficiency generally come from higher bypass ratios or novel low-pressure (LP) systems such as an open rotor. The EFE focus is on improvements to the thermal or cycle efficiency of the engine which are yielded from higher temperatures, higher pressures, or improved component efficiencies within the core. A low-emissions combustion system will also be tested to significantly reduce NOx output.”
The EFE emerged from a UK-funded collaborative research programme between industry, academia and the public sector, with Rolls-Royce acting as the lead partner and being responsible for the core engine demonstrator including all hot-end technologies. The programme started as far back as 2006 with the other partners being Bombardier Aerospace, HS Marston Aerospace, Unison Engine Components and several leading UK universities.
The EFE demonstrator has been developed from the Trent 1000, the launch engine for the Boeing 787 Dreamliner. It is heavily modified but retains the three-shaft Trent pedigree.
The most striking difference between the Trent 1000 and the EFE is that the new demonstrator has no fan blades. The fan case is retained to mount the accessory gearbox, control system, wiring and other externals. The fan rotor has been replaced with a four-stage booster feeding directly into the intermediate-pressure compressor, meaning that there is no bypass flow, so the EFE operates as a turbojet rather than a turbofan.
The booster was designed specifically for EFE. It delivers a pressure ratio of just over two and has a variable bleed from stage four. The intermediate-pressure compressor and high-pressure compressor are taken directly from the Trent 1000 engine and incorporate minor design changes to cope with the elevated conditions that EFE will achieve.
Cross says: “The heart of EFE consists of the combustion and high-pressure turbine systems. It is here that most of the innovation and technology validation will occur and these components are bespoke to the demonstrator engine.
“The engine features a low-emissions combustion system, also known as ‘lean burn’. The fundamental objective is to combust fuel and air at lower temperatures – with an excess of air in the primary combustion zone. This process is inherently unstable and is overcome by each fuel sprayer having both pilot and main zones. These zones are then phased to best suit the combined requirements of flame stability, smoke, emissions and combustion efficiency. In this field EFE is developing new design methods which have enabled a combustor which provides stable combustion at low power and optimised high-power lean stoichiometry exhibiting low emissions.”
The other key area on EFE for technology validation is the high-pressure turbine. This area has arguably the most arduous duty of any in the engine. The rotor blades rotate at 13,500rpm with tip speeds reaching 1,200mph while operating at temperatures well in excess of the melting point of the alloy, and each is developing 800hp, equivalent to a Formula One engine.
On EFE the turbine rotor blades feature a shroudless design. Traditionally Trent engines have incorporated a shrouded blade but as the turbine entry temperature increases the benefits of a shrouded design reduce. Here the main areas of investigation will be iterations of the film cooling for the aerofoil of the blade and control of the tip clearance.
Different cooling specifications are being tested and each build of EFE features several specific designs of the rotor blade to enable a back-to-back comparison to be made.
Innovative designs have been developed to allow closed-loop control of the tip clearance by both thermal and mechanical systems. The blade tip and the adjacent rotor path also feature state-of-the-art coatings to ensure through-life performance retention.
To enable the correct conditions to be achieved, EFE has been designed with a variable cycle by means of bleeding air from the compressors, adjustable final nozzle area, and inlet screens that allow a pressure loss at entry to the engine core. This gives the ability to test components at temperatures and pressures far above those in service today.
The intermediate-pressure turbine is again taken from the Trent 1000 – although rotor blades made from an enhanced material, providing greater temperature capability, will be included for endurance testing.
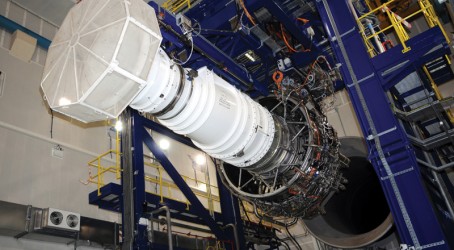
The low-pressure turbine is another component specifically designed for the EFE demonstrator and is a single-stage machine rather than the multi-stage turbine required to drive a fan on a conventional turbofan engine. The low-pressure turbine also features components made from single-crystal alloys to allow the full potential of the EFE cycle to be realised.
Most of the engineering design and analysis on the project was carried out at Rolls-Royce’s Derby site, while the assembly and test activity is taking place at Bristol where EFE has a dedicated test bed. Initial runs focused on the functionality of the various engine systems. “Engine performance was generally as modelled by the specialists and from the first runs to power it became obvious that we had a vehicle that was fit for purpose,” he says. “One of the major concerns before the first run was the performance of the LP system as neither the booster nor the LP turbine had been subject to an aerodynamic rig test. As the aerodynamic modelling fidelity increases, the need for a rig test diminishes. This was proved on EFE with both of these components meeting the desired characteristic. The booster passed slightly more flow than predicted at the design point pressure ratio, an encouraging result.
“Both the intermediate- and high-pressure compressors were judged to be known quantities as they were basically Trent 1000 components. Working lines and flow/speed relationships were all within expectation.” Measurement of the pressure loss during the combustion process was not as expected but investigation of this considering other recorded parameters has highlighted the need to relocate the pressure tappings, says Cross. “This will be corrected for the next phase of testing,” he says.
“Analysis of the turbine efficiencies and the air-fuel ratio were all within expected scatter of the pre-test model, as was the case with the turbine capacities. This was an important building block in calculating the core mass flow of the engine and here two methods are used to ensure any errors are, as far as possible, eliminated.
“The two methods are based upon turbine capacity and heat balance. A set of separate parameters are used in each to converge on the same answer, and the conclusion was an uncertainty in core flow of less than 1%.
“With a vehicle as complex as EFE, a one-off engine with a bespoke bleed system, this was a great result.”
Overall, the initial performance analysis has supported the pre-test model with the outcome that the vehicle is capable of delivering the required test conditions. Engineering data was acquired on many of the new systems operating on EFE – the overall quantity was 1TB of data recorded from 2,500 individual measurements.
The low-emissions combustion system operated without hitch, says Cross, exhibiting great starting characteristics through numerous fuel staging points at part power without perturbations. It also demonstrated low thermo acoustic noise at high overall pressure ratios.
Measurements of strain and temperature were also taken on the combustion system for lifting and thermal model validation. The project has also performed the first engine test of an advanced external dressing system which will be used initially on the next generation of large civil engines.
Most recently, a thermal paint test was conducted. “This is an experiment to collect detailed information on the temperature distribution observed on components, primarily the combustor and high-pressure turbine regions,” says Cross.
“Performing a test of this nature is all about the preparation, both in the assembly stages and the build-up to the test. The test point itself comprises only a few minutes on condition, so it is vitally important that everything is ready and ‘all systems are go’ – you only get one chance.
“The components under investigation are coated with temperature-sensitive paint during the assembly process. This paint changes shade, indicating the actual metal temperatures the surface of the components encountered during the test and giving detailed information on the temperatures achieved. But the shape of the contours is just as important for the analysis.
“The test is run to a predetermined turbine entry temperature, and the team made comprehensive use of risk assessment techniques to ensure the test was a success. The objective of the risk assessment was to ensure that the paint was protected from fuel contamination during starting and also that the temperature that the paint will change shade at is not exceeded during the build-up to the test point.”
The mitigations put in place for both of these events paid dividends but that did not detract from the high-pressure environment in the control room during the run itself. He says: “The engine was stabilised at a preliminary condition and whilst at this point performance engineers and other specialists performed online analysis to ensure that the engine was behaving as expected and that the engine matching had not affected the target temperature.
“Happily everything was in order and the team secured the test point as planned. Following a controlled shutdown the engine was removed from the test bed and returned to the assembly shop for strip to component level.”
The next task for the demonstrator is to perform a cyclic test. Modules for this are now on build and it is planned to conduct the test in the latter half of 2012. The first product to benefit from technologies developed on EFE will be the Trent XWB programme for European planemaker Airbus, says Cross.
The EFE project is also expected to go on to deliver technologies for the next-generation of Rolls-Royce aeroengines, further improving fuel-burn efficiency and reducing environmental impact, he says.