Rolls-Royce’s MT30 marine gas turbine is said to be one of the most advanced and powerful engines of its type. It will be used to power the Royal Navy’s Queen Elizabeth class aircraft carriers, which are under construction. It has also impressed the US Navy, which is using the MT30 on the Lockheed Martin version of the Littoral Combat Ship. In the future, the turbine will also help to propel the Americans’ DDG-1000 Future Surface Combatant Destroyer.
Rolls-Royce did not dream up the MT30 out of thin air. Or rather it did, in the sense that the marine engine owes its development to the engineering giant’s work in the civil aerospace engine market. Rolls-Royce calls this design process “aero-derivative”. Alan Millichamp, MT30 product director, explains: “What we’re trying to do is take components from the Trent aeroengine family that have proven design integrity. In the marine environment, we are looking to be as low-risk as possible.
“We don’t want to be the trailblazer on technology – we’ll leave that to the civil aerospace guys.”
So the MT30 is firmly based on existing technology – the Trent 800 aeroengine came into service in 1997 and powers the Boeing 777.
The Trent 800 was chosen as the basis for the MT30 because it is among the most powerful jet engines in existence. Millichamp says: “We wanted to create a more powerful gas turbine based on our aero parentage. We went and looked for the biggest gas turbine core we could find within our portfolio and based our engine around that.”
So how was the Trent 800 modified as it evolved into the MT30? Having settled on an engine with a large core size – since its launch jet engine core sizes have come down and fan sizes have increased in the quest for fuel efficiency – Rolls-Royce engineers were able to base the architecture of the MT30 on the powerful Trent core. This provided a platform for the development of the new marine gas turbine.
Step one? Remove the aeroengine fan and fan casing, which leaves the core of the engine. The core must be modified to run on a special grade of diesel rather than kerosene. The core remains with its compressor, combustor and turbines. The shaft that in an aeroengine runs back through the centre to drive the fan, producing thrust, is removed. Instead, the shaft is reversed out of the back of the engine. “That’s the biggest change we make,” Millichamp notes. The MT30 also uses a gearbox from an earlier Trent, the 500, because the Trent 800 version is too large.
Vanes inside the gas turbine that help redirect the flow of air inside the engine on an aircraft are straightened up, and anti-corrosion coatings are applied to engine components to help the MT30 withstand the rigours of the marine environment. “We also have to allow for the fact that, because the fuel is no longer kerosene, there is a higher sulphur content,” he says. The engine must be contained within a compact enclosure which hosts ancillary equipment such as ventilation fans and a fire protection system.
One of the selling points of the MT30 is that it crams a lot of power into a relatively small package compared with the largest diesel engines. “For power density we try and keep the engine as compact as possible,” says Millichamp. For instance, two MT30s might fit in the space of a single large 14MW diesel engine, but would produce a total of 72MW of power.
Originally the MT30 was intended to be a commercial marine design, targeted at cruise ships and fast ferries. However, it’s been the military with which it has found favour. Millichamp explains: “Diesel engines use a much cheaper grade of diesel than we can use in a gas turbine, and that difference has increased since the MT30 was conceived. It’s no longer economic to use a gas turbine on something like a cruise ship, which is just the way the market’s gone. This may reverse itself as the industry starts to move toward liquefied natural gas, with both diesel and gas turbine engines operating a common fuel.”
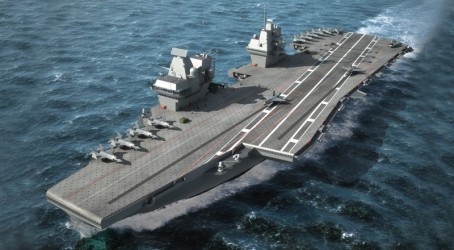
The MT30 is finding favour in applications where speed, power density, or both are needed. It would typically be employed to boost the performance of standard diesel engines, as on the new Queen Elizabeth class carriers. In some defence applications, extra power is needed to provide energy for weapons systems and radar. On the carriers, each of the two MT30s will provide 36MW of power. In this application, the shaft from the gas turbine drives an alternator which produces power that is fed to electric motors powering the propellers. In other uses, such as on the Littoral Combat Ship, the shaft can go to a gearbox to drive a propeller or waterjet.
When gas turbines are used in conjunction with diesel engines, they are there to provide boost. Typically this might involve them being used for 500 hours a year. The MT30 will be adapted for use in different types of application including a single gas turbine system combined with diesels for smaller ships such as frigates and corvettes. Another technological development could be to convert the engines to run on liquefied natural gas if this gains in popularity as a maritime fuel, which could suit commercial shipping.
Aeroengine designers and engineers are not thinking of potential applications in ships when they go about their business, so the onus is on Rolls-Royce’s marine division to take the best of the aeroengine line and adapt it accordingly. “The key feature for a marine gas turbine is to stay as close to its aero parentage as possible,” says Millichamp.
Environship boosts fuel efficiency by 18%
Rolls-Royce Marine believes that energy efficiency and environmental awareness will be key drivers for its business over the next 10 years. The group has been working on several engineering innovations that can bring efficiency savings.
One of these is an integrated rudder and propulsion system called Promas. The system comprises of a specially designed rudder with a bulb that is connected to the hub of a propeller by a tapered hub cap. The hydrodynamic rudder can adapt to the rotation of the propeller slipstream and has a twisted leading edge that is optimised to catch the flow from the propeller and convert it into forward thrust.
These aspects help to improve the efficiency of propulsion by up to 8%, reducing fuel consumption and emissions. Sauli Eloranta, executive vice-president of engineering and technology at Rolls-Royce Marine, explains: “Promas transforms the philosophy of a rudder from a steering device to an energy conservation device.” At the front of the ship, energy can be saved by employing a similar design to that used on high-speed catamarans. A so-called wave-piercing hull form allows the vessel to slice through the waves instead of running on top of them, which reduces friction by up to 8%. This allows ships to travel at a constant speed even in choppy conditions and to cut fuel consumption.
Combining both these technologies in tandem with a gas engine can bring significant savings. A vessel that uses all three technologies, known as the environship concept, can increase fuel efficiency by up to 18%, according to Rolls-Royce. An environship with a lean-burn gas engine emits 17% less CO2 per unit of power than with a diesel engine, and nitrogen dioxide emissions can be slashed by 90%.
Other technologies that the group is working on include permanent magnet technology, electric propulsion systems with a direct-current architecture, and energy recovery from the back and forth keeling of ships.