About 5 years ago I did a more detailed series which will undoubtedly be out of date in places but they are still worth a read, a consolidated PDF version is available here.
I aim to take you through the thought processes envisaged so that you can follow a clear and logical path to success. I will probably not give you “absolute answers” as such but I will provide you with the necessary hints and tips that will allow you to define your own “answers” and, most importantly, some justification to support them. It should go without saying that any numbers mentioned are most likely made up examples, or not?
Let us remind ourselves that FS is an educational engineering event that utilises the “glamour” of motorsport to create better engineers. And that everyone’s situation is different.
Part 1
The envelope governing FS is the Rules. In the UK there is a base set of Rules (FS Rules) which are supplemented by the UK Supplementary Rules (UK Supplementary Rules). These supplementary rules cover changes unique to the UK, e.g. the integration of both EV and IC cars into one class, the addition of Class 2 for which a running vehicle is not required etc.
I like to visualise the FS Rules as setting a series of challenges or questions to which you need to supply justifiable answers.
Takeaway 1: there is no correct answer to any of the challenges set by the Rules. All answers (solutions/designs) depend on your own resources.
This first article is primarily aimed at Class 2 teams although most of the information here will also be of use to new Class 1 teams. Reference to guiding documents requires you to locate them on the official FS UK website. Explicit links have been avoided as documents are updated regularly and diligent research of information is a key FS, and life, skill.
There are many queries about the Rules that we, as organisers, have officially answered before. We provide a searchable database known as FSQD, which we would urge you to review before asking us a question as it is possible it is already answered. Please do seek official answers before believing the Internet about a FS Rules query, as the local UK rules do differ slightly in areas from the FSG and FSAE ones.
Why enter Formula Student?
You’re reading this because you have heard so much about this wonderful event that you can no longer miss out on it. Or someone instructed you to do it. Or you are set to gain some credits towards your degree. Or because race car. Or something…
In order to achieve anything, or to get anywhere, you need to know where you are starting from, where you need to end up and any restrictions that might shape the path between start and finish. It’s like map reading: there are many possible routes and some may have weight or height restrictions!
Takeaway 2: the best reason for doing FS is that it will make you a better engineer, a better person and a more employable future graduate.
FS is not something that can be achieved by a single individual but equally there is no need for a massive team. A small team requires far less organisational overhead and should be easier to motivate.
Where do I start?
I would suggest that the minimum team size is 6 persons. Even such a small team should be able to design and assemble a running Class 1 car in 12 months although that would require huge commitment.
So Class 2 is effectively a “concept design” class where the amount of stuff you actually need to make or build is entirely up to you. The Score Sheet includes a section relating to prototype parts and lessons learned in moving from drawing to hard parts. The key advantage here is that you are not having to manufacture and assemble a complete vehicle. Consequently, you don’t need full workshop facilities or training and so it should be much easier to get the necessary “buy in” from your University or Department.
Takeaway 3: the more you make the more you learn. No parts mean no points (in that section) as usually it means little learning!
Class 2 is intended to make the learning curve shallower by spreading the design and build of a Class 1 vehicle over 2 years. As organisers we don’t see that students, or Universities, should view Class 2 as an ultimate standalone ambition.
Looking inwards: self-reflection time
Start with a reality check as to where you are and what you have. This is back to the map analogy, where are you starting from and what might confine your journey path?
Consider your resources, i.e. people, time, skills, money, knowledge, facilities, help etc.
Takeaway 4: write it all down as this documentary evidence is how you justify things to Judges.
By way of example if you have no real electrical/control/electronics wisdom in your enthusiastic team then an EV is not really a viable design. If you have no access to a workshop then all your fabrication will need to be sub-contracted which will add significantly to your manufacture time, etc.
Looking outwards: Research and Benchmarking
This is the first step in deciding what you want to achieve; in the map analogy this is your end destination.
My advice is to look back over say the last 3 years of competitions and review the points scores obtained, across the event disciplines as well as overall and tabulate them. You might find someone online has already done that, if so, use at your own risk! Look through past event programmes or entry lists, photos and team blogs etc. and try to add basic vehicle details to your table. You should certainly be able to find major conceptual facts such as tyre size, engine configuration, 2 or 4 wheel drive, full aero pack or not, fuel and very importantly mass. You might usefully consider adding in any official Cost score or any published real-world costs.
If you are very capable you may be able to add basic dimensions for wheelbase and track width, possibly even claimed power and battery pack capacity. You could perhaps estimate the likely team member count from team photos or again from the proud blogs that FS teams like to operate.
Takeaway 5: the table above will show you what has been successful, and not, in the past. It’s cheaper to learn from others’ mistakes than your own!
Analyse and consider the table information very carefully: you will certainly notice that only those that completed all Dynamic events were in the top points section. The table will also show you, within reason, the limits of what was realistically achieved. For example, you will now have an idea of what the lightest car was, the most powerful, which had the smallest power pack etc. You will also have an idea as to the most popular configuration, which tyre statistically seems quickest, did the really expensive, very light full aero car actually corner quickest?
Armed with the above you can now shortlist a few conceptual layouts (complete with some pretty valid numbers for main parameters) to consider further. Remember the dynamic points include a strange variable: the driver!
Assuming that you have looked at enough vehicles you will have a fair idea of the performance of the main types of car which will allow you to distil it down into very basic performance facts to correlate things like mass and power against dynamic performance, especially acceleration and skidpad where the (unknown) influence of the driver is less of a factor.
Takeaway 6: the above is, by definition, going to preclude anything completely novel. For a first-year team this is a good thing.
True innovation or originality implies a high degree of risk as you can only learn from your own mistakes. This is something for later years when you have some experience.
Iteration: the circle of design
You now need to return to your resources list and go back and forth a few times to realistically balance what you want versus what you might be able to do. This is an inexact science as you won’t 100% know what you can or cannot do but at least you will know what was/is possible.
What you should be able to do is to look at say 3 possible sets of specific performance targets found from your benchmarking table, e.g. high performance orientated, mid performer and what is hopefully a low-cost low performance option.
You now need to move from the performance outcomes (i.e. acceleration and skidpad time, economy etc. and not forgetting cost) to the design targets (power, mass etc.).
The waterfall of logic
Judges want to be shown a clear logical progressive design process. They need to see how the 150kg, 60 bhp car is a sensible solution to meet your (customer) performance requirements of say 4.75 seconds acceleration, 5.5 seconds skidpad and 0.13 fuel efficiency factor.
Your benchmarking table will form the empirical basis of showing how the design targets are cascaded down from the performance requirements. Fundamental calculations, simple simulations etc. are also part of this as there are several ways to achieve the same end result.
You most likely won’t know the CoG height of past competitors nor their gearing. But you do know the angle required to pass the Tilt Test and you might know the minimum track width previously specified in the Rules and so you can make an educated estimate of a likely maximum CoG height. You can probably find out the claimed maximum speed obtained in Endurance or Sprint and most motorbike engines have an integral gearbox so again an idea of gear ratios can be deduced… Most of the basic tyre information is available from the manufacturers.
With all this knowledge you should therefore be able to provide supporting justification as to why and how your specified basic vehicle parameters are cascaded down from the performance targets.
Options and conceptual decisions
Now you have some realistic design targets to aim for, with respect to likely customer performance requirements and all you have to do now is decide exactly what that design will look like! I suggest for each of the major vehicle areas you now list out the possible options, maybe then add a weighting based on your resources and you will quite quickly see what you need to be doing. This is a classic decision matrix type approach, see below example for Powertrain:
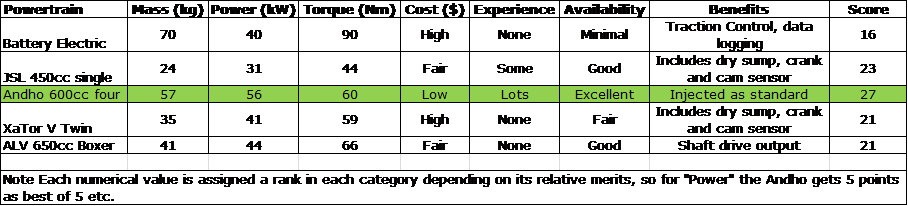
If you follow the above for the main functional areas then your main vehicle components will fall out from all the above possibilities. It is your design as it is based on your resources. Assuming that it continues to meet the Rules, it will represent a good answer to the challenges posed by the competition.<.p>
Takeaway 7: I will humbly suggest now that a first-year team (Class 2 or Class 1) should not consider any carbon composite parts, should not look at any aero package and should not consider an EV. So, you will be looking at a steel tube frame car with an IC engine, minimal bodywork and minimal complicated electronic driver aids.
Want more? Turbocharge your team's car at Learn to Win 2020, taking place on 25 October 2019 at the Manufacturing Technology Centre in Coventry. This is the first date in the diary that kickstarts the new season and brings together the event organisers, head judges and teams to discuss the year ahead and get feedback on every aspect on your car. See you there!