The first production application of a flywheel hybrid is likely to appear in the Wrightbus StreetLite product range by 2014. This marks a breakthrough for Flybrid Automotive of Silverstone which has pioneered the use of mechanical kinetic energy recovery systems employing either the clutched flywheel transmission or the continuously variable transmission of the type developed by Torotrak.
Flybrid is working with Wrightbus, Voith Turbo, Productiv and Arriva to optimise the hybrid power solution for the StreetLite mid-bus range. Productiv is examining how to put the flywheel hybrid system into production. Flybrid has a unique opportunity to demonstrate the technology. Both Voith and Wrightbus, for example, have many customers in Europe.
“That is why it is important to see that Wrightbus is fully up to speed and into production. That is our first target,” says Tobias Knichel, Flybrid’s commercial manager.
The project, which is part-funded by the Technology Strategy Board, aims to have the system ready for new vehicle introduction in 2014. The intention is to design the system for both new vehicle and retrofit applications. Knichel says: “We have the right partners – Wrightbus, which is making the bus, Voith Turbo, the transmission maker, and Arriva which is responsible for operating the buses. The full chain can share their knowledge, influence the system, and determine duty cycles.”
Flybrid aims to manufacture the units in-house. “For the volumes we are looking at for Wrightbus, we think we can cope with that within Flybrid Automotive. We are looking at expanding our facilities,” says Knichel. “It is on our wish list of how we want to grow. We think that the volumes that will be required for the bus and truck market can be achieved within Flybrid.”
The point at which Flybrid expands its testing and manufacturing facilities to accomplish these requirements is a matter that has to be carefully timed. The firm employs 20 engineers, which implies a turnover of around £2 million. It is searching for extra staff to cope with the increasing workload but is finding a shortage of skilled engineers.
The bus, truck and off-highway sector is just one leg of Flybrid’s business activity. Together they account for 20% of turnover; another 20% comes from motorsport interests and the balance from road-car applications for OEMs.
According to Knichel, truck applications of flywheel hybrids are likely to appear after bus and off-highway launches. The off-highway application has about the same timing as the Wrightbus project. If you look at time to production, motorsport is always the quickest, and this is followed by bus, truck and off-highway applications. The last three are quite similar in terms of flywheel hybrid requirements and in terms of how quickly they can go into production.
Road-car applications are right at the end. Many more people are involved in the decision-making and therefore they require a longer time to go into production.
It is the motorsport side that provides the impetus for the main development thrust. Within motorsport, timescales are short and new programmes are developed quickly. Although production volumes are low, the intellectual effort is high and it is important not to make something that is specific to motorsport, but from which technology can be transferred across to road cars or even bus, truck and off-highway applications.
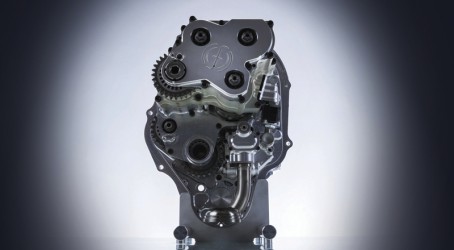
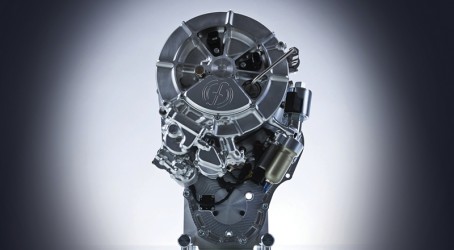
In a motorsport application, the system has to fulfil the identical requirements of a road car, for example controllability, reliability, durability and refinement. But performance aspects are higher, and this assists in the development of bus, truck and off-highway applications.
Flybrid’s systems were used this year in the Dyson Racing Lola B12/66 Le Mans prototype 1 cars. It is expected that a more powerful version will appear in 2013.
On the road-car side, development work with Jaguar Land Rover has proved particularly beneficial and is now being further extended. Initially commissioned to demonstrate fuel economy gains, the new work, still using the basic rear-axle mounted flywheel and continuously variable transmission (CVT), is directed at enhancing performance. But longer term the work could be aimed at the implications of hybrids for downsizing the engine to achieve the same overall performance.
At this juncture Jaguar Land Rover does not appear to have in prospect a platform that is ready to take a flywheel-based hybrid. That does not mean to say it will not happen. It is a question of timing.
In the case of Volvo, however, Flybrid entered the scene at the right time. Volvo was designing a new platform and that is flywheel ready. “It is suitable for our technology and could be launched around the end of 2016,” says Knichel. “All the people we have worked with are open to the technology, and keen to learn.”
Jon Hilton, Flybrid’s chief executive and now responsible for future strategy, says the company is looking forward to starting a new road-car programme next year.
In motorsport, during 2012 all the applications used clutched flywheel transmission (CFT)-based kinetic energy recovery systems. Although the units ran at 100kW, they were designed with 200kW capability in mind. The company hopes that 200kW units will be permitted in 2013.
According to Knichel, the efficiency of a 100kW CFT unit is “well above 80%”. To achieve higher efficiencies, the ratios across the clutch plates must be increased. But increasing the ratios raises cost, so an assessment of the cost-benefits is crucial. In a city car, for example, a three-clutch CFT with a two ratio range-extender would generate a ratio width of six; in motorsport, a seven-speed gearbox with a three-clutch CFT would generate 21 ratios; while a four-clutch CFT would give 28 ratios.
For this reason, a CFT design for a city car will differ from that for a luxury car. In this respect, a CFT is more flexible than a CVT. A CVT for a city car would have to be redesigned for use in a luxury vehicle whereas with a CFT it is necessary only to copy the components, for example using four clutches instead of three.
It is recognised that CVTs do not easily scale down in size, whereas CFTs can scale in both directions – down for city cars and upwards for buses, trucks and off-highway uses.
Flybrid’s kinetic energy recovery system (KERS) can be used in many different off-highway applications. It could be used in dump trunks or wheeled shovel loaders. These operate a “Y duty cycle,” that is they are driven repeatedly forwards and backwards into a pile of earth.
The vehicles are heavy but the travel speed is low so the kinetic energy available is low compared with other applications. The main benefit of KERS comes through improved fuel economy and engine downsizing.
There are multiple occasions when these trucks require high energy, such as driving into a pile of dirt. Power and torque levels are high, requiring a large engine. However, most of the time the maximum power of the engine is not being used. Alternatively KERS could be used as a power boost, but with a smaller engine to cover basic use.
The most obvious trend in flywheel design over the past couple of years has been the reduction in carbon-fibre content. Because of the high cost of the material, engineers are reducing the volume used in the flywheel. A typical flywheel now contains less than half the carbon fibre used two years ago.
Also, flywheel speeds have reduced from around 64,500rpm to 60,000rpm, with a positive impact on the weight of the containment. Design of the steel rotor has become much more sophisticated – again in a bid to save weight.