Earlier this year Nasa took an unprecedented step – it awarded a substantial grant to a non-US institution to fund research into future propulsion systems.
Such projects are normally carried out on home shores. But in this case an endowment from the legacy of a Scottish space enthusiast led Nasa to seek out aerospace experts at Cranfield University to study a concept that could one day revolutionise air travel, much as the arrival of the jet engine did in the 1950s.
The three-year research programme will look at the novel concept of distributed propulsion, which brings the potential of huge cuts in fuel consumption and could even pave the way towards the use of hydrogen fuels.
The research could see aircraft fitted with multiple small engines across the width of a wing. Advantages of such a design would include safety through increased redundancy and economies of scale in production and maintenance.
A second approach could see the use of a few cores powering many propulsors such as fans, which could be driven mechanically via shafts, by hot gas ducted from the core engines via tip turbines on the wings, or even electrically.
These approaches could be used in conjunction with blended-wing body design airframes. Over the years Cranfield University has been engaged in this field of research and has developed novel concepts of its own to improve propulsive efficiency and airframe performance. This wide-ranging work has considered future distributed propulsion systems including turbo-electric. And it was this expertise that convinced Nasa to award the grant.
According to Riti Singh, professor of gas turbine engineering at Cranfield, and one of the most highly regarded aerospace propulsion academics in the world, the funding will enable researchers to fundamentally re-evaluate the way that civil aircraft are designed and built. He says it will allow careful consideration of what the next generation of propulsion systems and airliners might look like and the sorts of environmental savings that might be achieved.
“Today, we stand at a crossroads, as we did in the 1940/50s when all airplanes had piston engines,” says Singh. “Then along came the jet engine which allowed us to fly over bad weather in comfort and safety and to fly much longer distances. It opened up passenger travel, making it much more accessible.
“The consequence, though, is that there is so much air travel that, whether or not we think it’s a problem now, it’s difficult not to concede that it won’t be a problem in the future. So the question is – what are the options? Should we curtail aircraft use? Or should we try to use more biofuels?
“Or do we start to look at the nature of truly disruptive technologies such as distributed propulsion that could really change things. I think it’s time to consider where we go next.”
The predominant configuration of aircraft with podded high-bypass engines seems to provide the best solution for civil transport. But Singh argues that this might not necessarily be the case in the future. An alternative platform might derive greater advantage from the infusion of emerging technologies.
The work at Cranfield University on distributed propulsion has looked in detail at spreading the thrust of the propulsion system along the span of the aircraft. Theoretically, the concept could potentially allow far better integration of the propulsion system within an airframe, resulting in improved aerodynamic performance and more efficient use of the thrust stream from the many propulsors.
Singh says the Cranfield team’s calculations show that use of such a system could potentially result in noise reduction, lower propulsion system life-cycle costs, lower maintenance costs and reduced fuel consumption. A lower probability of critical propulsion system failures could make aircraft even safer.
“The benefits of multiple small engines are easy to define,” he says. “In a modest-sized aircraft you might have 20 engines and in a larger aircraft it might be 40, or even 100-150 in a 777-sized aircraft and up to 250 on the A380. But they would be the same engines.
“The number of these engines being manufactured would be so large that their price would come down, as we have seen with the cost of the motor car. There would be huge economies of scale.”
There would also be redundancy advantages, he argues. “In a twin-
engined aircraft, if you are going down the runway to take off and one engine fails, the remaining engine has to be big enough to safely take the aeroplane up, so the engine has to produce twice the power it would normally be producing. With 100 engines, though, if one or two fail you only have to install 1% or 2% more power.”
Management of the fleet would be so much easier, he says. “Again, if you have 100 engines and you are monitoring them, and you are of the view that one of them has a problem, then when you land these engines would be so small that you would just unplug the faulty one and replace it. You would never wait and investigate it, as there would be so many spread across the wing.”
To determine the feasibility of distributed propulsion using large numbers of small gas turbines to produce the thrust required, Singh and his colleagues have already spent many hundreds of hours modelling the effects of engine performance scaling on small gas turbines, along with other factors such as nacelle weight and drag, wing bending relief, fin sizing design requirements and climb gradient design requirements. Singh says that long-term cost-benefit considerations of implementing such a radical concept have also been studied in detail.
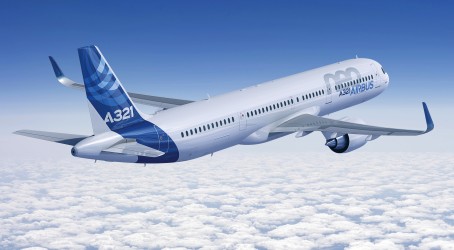
“Small gas turbines might, at present, be less reliable than their large counterparts, but that is because the bigger engines have had many billions of pounds research spent on them. Over time I think it would be possible to develop smaller gas turbines with similar reliability levels,” he says. “However, it is unlikely that their fuel efficiencies would match those of larger engines, and this would present a major hurdle.”
The propulsion units used for a distributed system might not necessarily be gas turbines. Other options being considered at Cranfield are gas-driven fans and electrically driven fans. The concept of a few fuel-efficient cores with many propulsors could take advantage of alternative airframes, maximising thermal and propulsive efficiency.
“If you went down the route of driven fans, then you could design the individual engines for maximum thermal efficiency, the fans for maximum propulsive efficiency, and you would then be left to take care of the transfer of power so that reliability was high and the transmission losses and weight requirements were low,” he says.
Singh and his colleagues are particularly interested in superconducting electric propulsion systems, with superconducting electric fans powered by two turbine-engine driven superconducting electric generators, with cryogenic hydrogen as fuel and cooling ufb02uid for the superconducting system. He believes that superconducting rotating machines could achieve power densities comparable with those of turbine engines, making superconductivity an enabling technology for the more efficient turbo-electric aircraft of the future. “Superconductivity is already being used in some local power transmission situations, so it’s not unknown,” he says.
“However it is used in quite unusual circumstances where the return on investment is very large. But if you go down the business of a step-change for civil aviation, then we could see the necessary research and development funds becoming available.”
Indeed, Nasa itself has already invested millions of pounds into turboelectric drive systems through its N+3 research programme. It believes that decoupling of the propulsive device from the power-producing device could result in high performance and design ufb02exibility and high fuel efufb01ciency.
The speed of the power turbine shaft in the turbine engine would be independent of the propulsor shaft speed. There would be minimal engine core jet noise due to maximum energy extraction, and large electrical power off-take for in-ufb02ight and ground use, according to Nasa. Singh’s work will progress in tandem with Nasa’s own programme. “By using superconductivity for reducing the transmission losses and for cooling of the electric motors, you could get a significant improvement in the transmission loss and a significant reduction in the weight,” he says.
“If you bring everything together – moving to a more efficient airframe, improvements in engine design, distributed fans and superconductivity – then by the time all that is factored in you could talk about changes and improvements of 65-70% in performance. This could be the time when it is appropriate to introduce liquid hydrogen, first for cooling and then as a fuel for the new fleets of aircraft.”
This kind of distributed propulsion system could also see a better integration of the propulsion system with the airframe for noise reduction. It could also result in reduction in aircraft propulsion installation weight through inlet/nozzle/wing structure integration and elimination of aircraft control surfaces through differential and vectoring thrust for pitch, roll and yaw moments, says Singh.
“You would have a large number of small fans integrated within the airframe, capable of tilting. So you remove the control surfaces from the aeroplane, and it becomes totally smooth, meaning there is less drag.”
Looking even further into the future, Singh says he can see a time when hydrogen-fuelled planes could be used to warm or cool the atmosphere. “If you are using hydrogen as a fuel then at the exit what you get is water. You could condense the water and put it out at different droplet sizes to achieve global cooling or warming. As you take off from Heathrow, for example, air traffic control might say ‘it’s cold over Europe, can we have warming’. But as you fly over the Middle East you could have cooling. We have developed a patent on this and it’s a really interesting technology.”
Ultimately, he says, such a technology could see aerospace playing a vital role in the battle against the effects of climate change. “Instead of saying let’s curtail civil aviation, it might be an industry that helps the environmental situation.”
50 years of research on gas turbines
Riti Singh is an emeritus professor of Cranfield University. Until 2006, he was the deputy head of the school of engineering and the head of the department of power, propulsion and aerospace engineering.
He is the director of the Rolls-Royce University Technology Centre in Performance Engineering at Cranfield and is a past chair of the aerospace industries board of the Institution of Mechanical Engineers. He has received many accolades during the course of his career, including the international aircraft engine technology award for 2010, presented by ASME’s International Gas Turbine Institute for innovative personal contribution.
Singh has chaired many international conferences on gas turbine technology and holds numerous patents and has published widely. He has provided consultancy to more than 40 organisations, including gas turbine manufacturers and users in 20 countries.