Jon Beasley knows his stuff. As an automotive industry veteran with more than 27 years’ experience of working for multinational suppliers and leading OEMs, he’s been around the block a few times and is acutely aware that the sector has been through more than its fair share of ups and downs.
That historical perspective explains why Beasley has a smile on his face. He knows that now is a good time for the car industry, with UK-based manufacturers such as Jaguar Land Rover, Nissan and Toyota recording surging sales. And then there’s the level of support from government. When it comes to schemes designed to encourage innovation, the automotive industry has never had it so good.
This support is exemplified by the formation of the Advanced Propulsion Centre (APC), for which Beasley is director of technology and projects. The government-backed APC is match funding investment into the automotive sector to help establish the UK as a global centre of excellence for low-carbon powertrain development and production in a £1 billion programme. The centre, which is based at the University of Warwick, aims to bring small companies together with large OEMs to progress new technology ideas such as flywheels, electric machines and novel engine architecture.
Beasley is a passionate advocate for the APC, predicting that it will help stimulate innovation across the industry. “The APC represents a commitment from the government and automotive industry to bring tomorrow's low-carbon powertrain technology to market, for the benefit of UK plc,” he says.
“That means taking promising technological developments through industrial and experimental research to the point of commercialisation, crossing what is sometimes known as ‘the valley of death’. We have a lot of clever people coming up with good ideas, but often the risk of introducing them to the market is too great. Sometimes the technology is not robust enough, or it’s simply not ready for production. We are trying to help plug those gaps.”
The technology considered for APC development funding must relate to four themed areas: internal combustion engines; lightweight powertrain structures; electric machines and power electronics; and energy storage and energy management. In terms of their state of evolution, the projects need to be in the order of technology readiness Level 6 or above, or manufacturing readiness Level 4 or above. They must deliver significant reductions in carbon dioxide emissions compared with current best-in-class technologies, and have a clear demonstrable route to production. Projects must involve one vehicle manufacturer or Tier One supplier, and at least one small company.
“We are not looking to work with people who have an idea sketched on the back of a napkin,” says Beasley. “The technologies must have already showed potential. They’ve also got to have industry interest, not just from the innovator, but also an end customer. We will have at least one OEM or a Tier One playing an active part in the programme. We want technologies that have potential to enter the market for economic impact and not just sit on the shelf.”
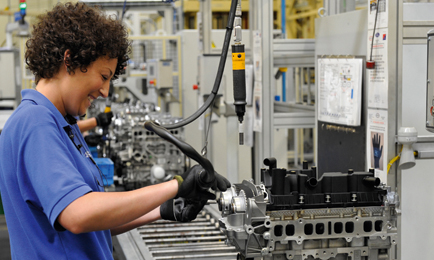
Upgrade opportunity: Ford and its partners won a grant for the EcoBoost
Industry partners will be supported through funding based on the outcome of biannual ‘competitions’, effectively acting as calls for interest. The competition process will see a minimum of two calls per year. “That’s because we want to give confidence to industry that it’s not as and when we have some money available – it’s a regular cadence. What we are promoting is the opportunity for research and development departments to start to align themselves to these competitions,” says Beasley.
The first competition, announced last year, led to four projects which resulted in collaborative funding worth tens of millions of pounds.
Ford and its partners won a £13.1 million grant for the company’s £100 million programme to upgrade the EcoBoost engine. GKN Land Systems and its partners, meanwhile, will receive a £7.5 million grant as part of a £16 million project to apply flywheel energy recovery technology for use in buses. The third project saw Cummins and its partners collect a £4.9 million grant for a £9.9 million project to progress stop-start diesel engine technology for buses. And JCB and its partner Flybrid received a £3.3 million grant as part of a £7.2 million project to apply Formula One technology for use in diggers. “The first four projects confirmed were an interesting mix. There was real breadth to them,” says Beasley.
In terms of return on investment for the APC, and ultimately for the taxpayer, rigorous assessment is carried out at the application stage, he says. Partners must put forward a firm business plan, including timelines towards production for any new technology, predicted sales, employment opportunities and wider supply impacts. “Those factors are all in documentation,” he says. “We want to move from being an R&D demonstrator to a pre-commercialisation exercise.”
The projects themselves won’t be undertaken at the APC. Instead, the organisation is based on a hub-and-spoke structure. A small core operational team will be based at the University of Warwick, while the ‘spokes’ will be established centres of excellence selected by the APC.
“There won’t be a bank of machines here at the hub. Why put money into replicating what probably exists elsewhere?” asks Beasley. “If we take power electronics as one of our technology themes, there is no point in the APC building a power electronics lab here at Warwick – let’s use some of the centres of excellence that already exist. There’s no advantage in duplication.”
That’s not to say that the APC hub will be totally hands-off. Partner progress is monitored to ensure that goals are being achieved. Engineering and business advice and help will also be available. “APC services will help to enable the projects,” he says.
The winners of a second round
of competitions have now been confirmed, and up to £200 million is available for projects in the coming months. There is now some real impetus behind APC activities, illustrated by a high-profile opening of the Warwick hub at the end of last year by business secretary Vince Cable, says Beasley. The APC exemplifies a new era of collaboration in the car sector, with companies realising they can work together to good effect, he says.
“If you went back a few years, you would have been lucky to get two OEMs in the room. But coming together to build consensus is powerful, and collaborating on core technologies can be a good idea. Sharing development can lead to a lower piece price. Then it is up to the manufacturers to use the knowledge and control the systems on their individual platforms. That’s how they get differentiation in the market.”
No clear winner – but plenty of employment
Jon Beasley’s many years of experience in the motor industry give him respected insight into the pace of development of low-carbon technologies. He has worked for multinational suppliers and on government and industry programmes. He has held various leadership roles at GKN, representing Aston Martin, Daewoo, Ford Europe, Honda, JLR, Mazda and Volvo. Recently he was the programme director for the Transport Systems Catapult in the start-up phase, before joining the Advanced Propulsion Centre as director – technology and projects.
So will the winning technology be electric-hybrid, pure electric, fuel cell or hydrogen? That’s a multibillion dollar question. “I remember doing a presentation four or five years ago internally at GKN, and there was a slide showing a set of racehorses,” he says. “The question was: which technology are you going to back? Although we are now finding some differentiation, it’s still a wide open race. Industry is still backing a number of horses, because there is no clearly defined way forward.”
Looking to the future, although the industry’s position at a crossroads in terms of technology presents automotive firms’ money men with difficult decisions, the lack of consensus will bring real employment opportunities for engineers. Two areas that will provide strong opportunities are systems integration and the connected car, predicts Beasley.
“Cars are now incredibly complex machines. How do all the technologies onboard work together? How can they be integrated to make them more effective? The control between devices will provide opportunities for engineers,” he says.