Energy demand is set to double over the next 40 years. By 2050 there could be nine billion people on the planet, up from seven billion today. As well as facing the challenge of providing energy for this extra population in the face of depleting oil and gas reserves, there are additional environmental drivers to reduce CO2 emissions. So energy efficiency is set to become increasingly important.
Car manufacturers are staring down the barrel of stringent emissions targets. New cars in Europe will have to comply with a specification of 95g of CO2 emissions per kilometre by 2020. Despite developments in hybrid, fuel-cell and electric vehicle technologies designed to reduce emissions, the International Energy Agency predicts that two thirds of vehicles on the roads in 2050 will still be using internal combustion engines. These engines have been around for many years, but there is still room to improve their energy efficiency.
Dr Selda Gunsel, vice-president of global commercial technology at Shell, thinks that lubricants, in combination with emerging engine and fuel technologies, can play a key role in improving energy efficiency and reducing CO2 emissions in the automotive sector. She says: “This is a very complex problem and there is not a silver bullet. We need a range of solutions.”
One of these solutions could be to reduce friction. More than 20% of the energy that is generated from the combustion of fuel is lost by friction, depending on the engine type and driving conditions. Gunsel says: “The right lubricant choice can make a big difference in reducing friction.”
She adds that lubricants can also play a role as an enabler in new technology, such as turbochargers, transmission systems, low-friction coatings and alloys used in piston design.
Shell has been working on a number of projects in partnership with other companies to help develop the next generation of lubricants. A project with Daimler saw the development of oil for use with the latest engine technology for heavy-duty trucks. “We were able to go 100km by using less than 19 litres of fuel, which is a world record,” says Gunsel.
They have also developed a fluid for ZF Transmissions’ latest eight-speed transmission system which gives an 8% improvement in fuel economy compared with previous designs.
Gunsel says that industry specifications for lubricants need to keep pace with the latest developments in the technology. A concept oil that Shell has developed in partnership with Gordon Murray Design (see box overleaf) has been demonstrated to improve fuel economy in the T25 car by 6% but cannot be commercialised.
“The way that we set the specifications of lubricants needs to change,” says Gunsel. “Some of these very promising lubricants will not fit into the standards even though we know that they provide the protection to the engine that a lubricated system needs.”
She adds that some industry specifications are outdated and “don’t really make sense”. These rules limit the range of chemicals that lubricant manufacturers can use in formulations.
“We have shown that these oils work in a concept application and we are now working with some major OEMs, such as Tata and Chrysler,” she says. The work involves durability testing in the laboratory and in the field in passenger cars and heavy-duty trucks, and so far the results are good.
Developments in lubricant technology are also being made in the high-speed world of Formula One, where engine development has been frozen since 2008. This has pushed F1 engineers to turn their attention to other parts of the system in the hope of gaining a competitive advantage. Dr Dave Salters, head of engine development at Scuderia Ferrari, says: “Oil and fuel was not frozen so for the last few years we have beavered away in dark rooms and learnt more about oil and combustion.”
Within the Scuderia Ferrari team, a small group of engineers works on mechanical friction reduction. The engineers are working on lubricants containing non-linear viscosity modifying polymers that can be shaped to different frictional regimes to do different things.
Work is also ongoing in a new area of engine coatings, where the team is looking at heat transfer and heat exchange. Salters explains that developing these high-technology lubricants causes air in the oil to be an important factor. To help counter this, the team is starting to develop devices that can separate air from the oil, or use clever chemistry to keep air out of the oil.
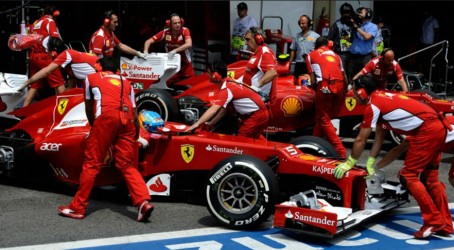
According to Professor Hugh Spikes, head of the tribology research group at Imperial College, London, the engineering focus for mature components such as ball bearings, cams and pistons has shifted over the past 10 years. Previously the main emphasis was on durability, reducing wear and friction, and making machines more reliable. He says: “Now in most mature components it is about reducing friction and therefore improving energy efficiency while maintaining very high levels of reliability.”
In the automotive sector this is reflected in a shift in emphasis from engines to transmissions. “It’s no longer about engine efficiency, it is about vehicle efficiency and CO2,” says Spikes.
Dr Robert Plank, vice-president of corporate engineering at Schaeffler Technologies, also has his sights set on improving the efficiency of the transmission. He believes that there are several areas within the powertrain where mechanical losses can be reduced. “The first is to reduce the normal forces – we can do this by lightweight design,” he says. Concentrating on the preload in the sealing of the bearing is another area. The sealing in a bearing creates 50% friction, so by optimising the design you can make gains, he says.
Plank goes on: “On the other side, we can also work on the friction coefficient, by optimising the macrogeometry on the surface, or by combining the materials with the lubricant to optimise the interaction.” Simply choosing the correct type of bearing and the correct arrangement can reduce friction.
Another solution for decreasing friction in the powertrain is to electrify it or downsize it. “You can take an electrical camshaft fastener and just move it when you need it. Throughout the whole system you can find places where you take small steps to optimise,” he says.
Aside from electrification, Plank says that there are two big areas where the industry can take steps forward in efficiency. Lubricants need to be considered during the design phase, he says. “If we take lubricant as a design parameter and bring surfaces or coatings together then we can go into another area of optimisation.”
He also sees value in working with lubricant manufacturers to benchmark simulation methods to provide more precise optimisation effects and better predictions.
Another area within tribology where work is ongoing to create the next generation of lubricants is in additives. All lubricants contain additives, chemicals that are added to extend the life of the oil and help protect the engine. There are typically 10-15 chemical additives in car or truck lubricants. The chemicals range from polymers that control the oil to antioxidants that stop the oil gelling at the surface. Some have very small molecules while others are polymers of very high molecular weight.
One company that formulates and makes these additives is Infineum. Mark Struglinski, vice-president of technology at the company, says that legislation is requiring lubricant additives to contain fewer metallic components, to help make the oil more renewable. “Part of what makes engine oils good is that they have some metallic-containing additives in them,” he says. So now manufacturers have to find new additive components to solve old problems. “It is requiring incremental innovations,” he says.
Infineum has recently developed a new additive that helps to keep engines factory clean as well as providing fuel economy. A clean engine lasts longer and gives off fewer emissions. So the benefits of such an oil are straightforward, but developing the additives for the purpose was not.
Struglinski says: “The things that you add to an oil to keep the engine clean also tend to make the fuel economy worse. So we had to find a way of working to balance these things.”
Struglinski and his colleagues used innovative chemistry, which is not typically used in engine oils, to create a new friction modifier.
Taking to wider industry the lessons learned from the automotive sector’s work on lubricants could help to reduce emissions, says Imperial’s Spikes. He says that much bigger gains could be made more quickly by applying these principles to industrial motor and gearbox lubricants.
“You just have to reduce friction by 1% to save terawatts because there are so many of those facilities. But the trouble is there are no drivers,” he explains. The driver for efficiency savings is usually legislation and there is no legislation for industrial gearboxes, he adds.
Spikes admits that there are still areas where tribologists are troubled with more traditional concerns such as improving durability and reducing wear. Engineers creating components for wind turbines, for example, are still solving the immediate problems of extending life. Designs for energy efficiency are likely to come in five years’ time once those challenges have been met, he says.
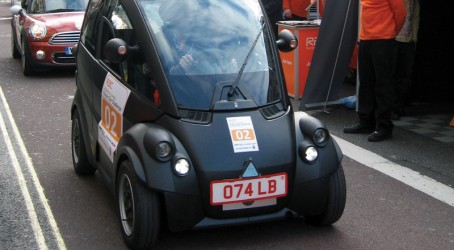
Concept oil boosts fuel efficiency
Surrey-based Gordon Murray Design has designed an innovative low-carbon city car, called the T.25. The lightweight vehicle has a very small engine for high fuel efficiency.
The company worked with experts at Shell to develop a low-viscosity lubricant that improves fuel efficiency while protecting the engine. Tests demonstrated that the “concept oil” improved fuel efficiency by 6.5% when driving in urban areas.
Professor Gordon Murray, chief executive and technical director, says that the work he did with Shell really galvanised the firm: “We could see the difference you could make with one bit of attention to detail on the powertrain. We got fired up about what we could do if we looked at the entire motor car. When you look at the internal combustion engine, all the low hanging fruit has been picked. The big bit that is left is a detailed attack on efficiency.”