Apprenticeships are in the spotlight this month with National Apprenticeship Week taking place in the wake of the coalition government’s announcement that it intends to create up to 50,000 apprenticeships with money saved from scrapping the Train to Gain programme.
At luxury carmaker Bentley, apprentices play an important role, with more than 50 on the company’s books currently. Christine Gaskell, member of the board for personnel at Bentley and a key figure at the independent Apprenticeship Ambassadors Network, is in no doubt as to their value to the business, whether joining as youngsters or taking equally important adult apprenticeships. She says: “The biggest issue with apprenticeships is the majority of people don’t understand what they are, and we work hard in the network to help people understand what an apprenticeship can do for a young person. Adult apprenticeships are also very important in our business as well in terms of upskilling: just because somebody’s missed an opportunity when they were 16 doesn’t mean they can’t train and gain qualifications in their thirties.”
Although Bentley, like other carmakers based in Britain, suffered during the recession, losing some 16% of its staff, funding for apprenticeships and graduate training was protected. There were no compulsory redundancies and Bentley actually upped the number of apprentices and graduate trainees it was taking on during a very tough period. This, Gaskell believes, has left it well placed to take advantage of improved fortunes for British manufacturing and the car industry. She says: “The one thing that is certain is that if you stop your graduate and apprentice recruitment at the start of the recession, when you come out of it you don’t have the skills in the business you need to hit the ground running.
“The decision to ring-fence that funding has really paid dividends for Bentley. We have apprentices and graduates who are now completing their training and are ready to take on their positions. We could have lost three to four years if we’d stopped our programmes. And it’s difficult to get that back. Once it’s gone, it’s gone.”
Charlotte Gough, a trainee electrical engineer, and Louis Warburton, who is training in mechanical engineering, have both completed Bentley’s four-year apprenticeship. Both youngsters are now studying for foundation degrees in their respective subjects on day release. Once the foundation courses are complete, a further two years’ study will lead to an honours degree.
As a schoolchild, Gough always knew she wanted to work with cars, while the father’s side of Warburton’s family ran a garage. Being a mechanic wasn’t for him, but he applied to Bentley’s apprenticeship scheme and was accepted. He soon became fascinated by mechanical engineering. Gough, meanwhile, applied to every carmaker in the country and turned down an offer from Ford to join the Bentley scheme, relocating to Crewe, where Bentley designs, develops, manufactures and sells its vehicles, from her native Cambridgeshire. Both have had the opportunity to travel, particularly to Mosel in Germany, where Volkswagen, Bentley’s parent, manufactures body shells for the new Bentley Continental GT, which both young engineers have worked on.
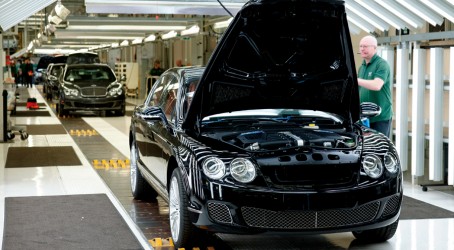
Gough says: “When I came here I never really thought of myself as an engineer – in some ways I thought it was out of my league. With the support you get at Bentley, however, it allows you to do anything you want, within reason. They’ve given me the support and confidence to become an engineer, which I didn’t necessarily think I would do – I was just happy working on cars.”
Gough and Warburton concur that there’s not a great deal of appreciation of the benefits of apprenticeships among their peer group. Warburton says: “Some of my friends are living at home with their parents, with masses of student debt; they have a fantastic degree but they don’t have a job. I’ve got my own place, I’ve got a fantastic job, and I’m still getting that degree – but without any student debt whatsoever. It’s brilliant. To me it’s the obvious choice.”
Gough says: “A lot of my friends went down the university route. They don’t understand what an apprenticeship is. They can be ignorant of apprenticeships, thinking you’ve got a job and you’re stuck there. But I will end up with a degree anyway, plus eight years’ work experience. And I'm being paid for it and I have no debt. It’s so much better.”
Gaskell is well aware of the tough situation that youngsters are now faced with in a scramble for university places and increases in tuition fees. “I think it’s difficult for young people now,” she says. “There are fewer university places, fewer options. Suddenly being an apprentice is a pretty good option. You’re paid, you’re in employment, you've got money in your pocket. Your friends who might be at college or university are working behind the bar on a Saturday night because they need to pay their fees – you’re in front of the bar. And you get qualifications too.”
Part of Gaskell’s role with the Apprenticeship Ambassadors Network is to try to overturn any stigma that might be attached to apprenticeships and increase awareness of their benefits. Bentley has set an ambitious target of upskilling a further 30% of its workforce by 2018. About half the staff there will then be classed as skilled.
Julia Gill, Bentley’s head of attraction and development, who is responsible for the apprenticeship and graduate schemes, says the company’s schemes could expand further. She joined Bentley herself as an apprentice in the 1980s. She says that apprentices often have valuable real-world experience allied with their academic work. “We have a good graduate programme and we look there for our future leaders, but they don’t have the practical experience the apprentices have,” says Gill.
“The apprentices are more worldly-wise because they've come straight from school and into a working environment. Sometimes the apprentices are more logical than the graduates, and they don’t mind getting their hands dirty. They get stuck into a problem easily, and we tend to look to graduates as our managers of the future. That’s not to say apprentices won’t reach management level – it might just take slightly longer.”
Warburton says that graduates may have outstanding academic skills but their lack of experience can be telling. “You get people who are fantastic with CAD. They could design anything but when it comes to making it you have to say: ‘you can’t make this from your drawing, go back and start again’. They don’t understand the whole process of manufacturing.”
Both Gough and Warburton are eyeing posts as senior engineers at Bentley once they have completed their honours degrees. The investment the company has made in them has made them loyal, they say. Warburton says: “When they are willing to invest in you and continue your education after your apprenticeship with a degree, it’s got to be a sign of good things to come. Effectively, Bentley is paying for us to continue to be educated. It makes you feel loyal to the company.”
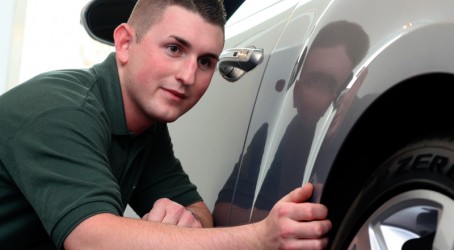
Gaskell believes that the apprenticeship scheme at Bentley bears comparison with the best in Europe. It was not always that way: numbers of apprentices had dwindled and the company made a conscious effort 10 years ago to remodel and revamp its scheme.
Gough says she would recommend a Bentley apprenticeship “100%”. “There can be a stigma attached to apprenticeships that they are lesser, or lower class. That’s just rubbish,” she says. “I would recommend the scheme here to anyone, male or female, whether they want to be an engineer or not.”
Volumes of cars produced by Bentley at Crewe dipped in the recession from its record year of 2007, when the factory manufactured 10,000 vehicles. The site is expected to produce 6,000 cars this year, and volumes are gradually improving. About 1,000 of these will be the flagship Mulsanne model – the “pinnacle of the brand” – with the other 5,000 coming from the Continental range, including the new Continental GT.
The company employs some 600 engineers, designers and stylists among a staff of 3,500. Bentley has a 90-year history. In the period between the First and Second World Wars, the company produced car chassis and engines, with the bodywork for vehicles being manufactured and fitted by coachbuilders. It was not until 1946 that Bentley produced its first steel body. The company’s first design studio came into being in 1951.
Today, the company employs a number of designers, many of them British, who work to ensure that new models preserve the distinctive design cues of the marque, such as the speed line and rear haunch. Typically four concepts for a new car are gradually whittled down to one design, of which a full-size clay model is constructed. The model is scanned to produce engineering drawings and the design is proven through further modelling. A final physical model will be produced in clay before the design is signed off so that tooling can be produced.
A great deal of hand craftsmanship goes into the build of a new Bentley, such as the distinctive wood veneers and leather seating used in the car’s interior. The factory employs a relatively low level of automation – there are just 16 robots on site – and models are often personalised at the request of customers. Full facilities for customisation exist at Crewe, and most of the vehicles produced at the factory are exported to countries all over the world.
A Mulsanne can use as many as 17 cow hides, which are carefully inspected to ensure that no blemishes make it into the final vehicle. Hide waste – typically only 60% of an individual skin will be used – is recycled. The company employs around 90 sewing machinists. A team of four can produce the leather seats for a vehicle in around six hours. There are 5,103 stitches on the Bentley logo.
Bentley invested €30 million last year in a new body shop for the Mulsanne, which welds together pressings from 15 suppliers. Most welding is carried out by hand. Bodies for the Continental range are sourced from Germany and Volkswagen.
The engine shop at Crewe assembles the Mulsanne’s V8 6.75-litre engine and the W12 6-litre engine used in the Continental range. The former is derived from an engine that Bentley originally developed in the late 1950s and which has been continuously refined and made more powerful in the decades since.