Another week, another multi-million pound investment in the UK automotive industry, or so it seems. The sector is riding high on the crest of a wave of international money flooding into the country. The funding is being used to create state-of-the-art production facilities, develop new models of car and, importantly, provide jobs.
The investment in recent years tots up to an impressive £5.8 billion and has helped to propel the sector back to the forefront of industrial policy. With every new spending announcement, another politician promises that manufacturing, and automotive manufacturing in particular, is going to pull the country from the grips of a double-dip recession.
The sector produces 1.5 million cars and 2.5 million engines every year. About 80% of these vehicles and 70% of the engines are sold overseas, making this the country’s largest export industry. In an average year the industry turnover is £50 billion, delivering £10 billion in net value-added to the economy and 3% to GDP.
Production rates are not yet up to pre-recession levels, but have been steadily rising for the past three years. In 2011, 1.34 million cars were produced, up from just under one million during the height of the recession in 2009. Earlier in the decade, production peaked at 1.65 million units in 2003. Forecasting by the Society of Motor Manufacturers and Traders suggests that by the end of 2015 the UK could be making 2 million cars a year – more than ever before.
Paul Everitt, chief executive of the society, says that reaching that landmark figure will depend on the stabilisation and steady growth of the global economy as well as the continued popularity of the models that are made here. But the underlying factor driving the rising production rates has been investment in the industry from manufacturers based here, he says.
There are seven volume carmakers dotted around the country and every one has chosen to pump millions of pounds into its facilities in recent years. There are several reasons why these international giants have chosen to invest here. Everitt explains: “UK facilities have worked hard over the course of the last 10 or 15 years to make themselves globally competitive. The relationship between company and employees is very strong, and the labour force flexibility gives us a very clear and definite advantage against competitors around the world.”
A stable policy framework has also helped to boost investor confidence, adds Everitt. He explains that, towards the end of the last Labour government, in the aftermath of the financial crisis, policy makers recognised that manufacturing was of strategic importance and that they needed to build stronger relationships with industry. Strengthening ties would ensure that the government created the most competitive conditions for investment, and this notion has been taken forward by the current administration.
Everitt says: “There is no doubt that the Regional Growth Fund, and before that the scrappage incentive, have helped to attract investment but I think the thing that has made the difference is a sense of stability and consistency in approach that developed under one administration and continued under a different one.” Plants now know which models workers will produce over the next 5-10 years, a situation that Everitt says the industry has never been in before.
But Professor Peter Cooke, head of the centre for automotive management at the University of Buckingham, has concerns over where all these British-made cars will be sold. He says that if they are destined for the Far East there could be trouble ahead as various indications of economic slippage have been reported in recent months. In the second quarter of 2012, China grew at its slowest pace since 2009.
“The next 12-24 months are going to be very tough. Beyond that, assuming we can get the financial situation working again, the market might start coming back,” he says.
Cooke adds that the industry needs to watch the growth rate in sales of products coming out of the UK. “I’m concerned that we have far too much excess installed capacity. If you look across Europe we have probably got an installed 25% excess manufacturing capacity.”
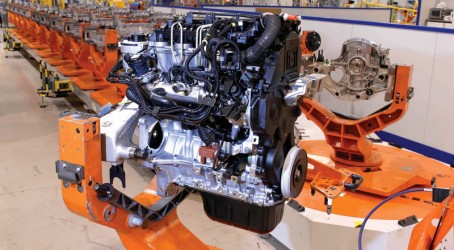
Cooke points to new production facilities coming online in South America, the Far East, Eastern Europe and Russia, as well as existing plants in China and Thailand that are now looking to export.
Cooke explains that BMW and Japanese car companies operating in the UK have “very strong” product line-ups and are likely to know where these vehicles will be sold. In addition, cars coming out of the UK have an advantage in that they tend to have higher specifications, he says. “But the UK manufacturing 2 million cars – at what price and how profitable are these going to be?” he cautions.
Across the Channel in France, PSA Peugeot-Citroën is struggling to compete in the European car market. In July, it announced the closure of the country’s largest car plant at Aulnay-sous-Bois, north of Paris, slashing 8,000 jobs. A further 5,000 jobs will go at its other French sites, including 1,400 at a factory in Rennes, after sales slumped in recession-hit south Europe. Peugeot-Citroën sales plummeted 20% in Europe in the first quarter of this year, and the company has warned that it faces a first-half loss of £553 million this year.
Despite the concerns that such news engenders, Cooke says that UK manufacturers are producing “superb quality” vehicles and have a well-trained and motivated workforce. He sees the headline investments as great news but believes the money is being spent to keep existing products fresh rather than creating any “huge new exciting” ones.
He says that new products are changing faster than ever before, and that there are all sorts of new players coming into the marketplace. Companies such as Kia and Hyundai are offering “amazing value products”. If manufacturers are not changing their products on an increasingly frequent basis, they are going to miss out, he says.
BMW recently announced a £250 million investment for the production of the Mini in the UK. As part of the spend, the company will produce 10 new models of the car. Cooke says: “BMW are trying to keep the iconic brand moving forward. Even a best-selling product like that has got to keep up to date.”
Another UK-based manufacturer that is developing models and updating existing ones is Nissan. Last year its Sunderland plant produced 480,000 cars, up from 330,000 10 years ago. The turning point came in 2007 when Nissan introduced the Qashqai – the company’s highest-selling vehicle in Europe ever. From then on production volumes began rising steadily and continued to climb with the introduction of another model, the Juke, in 2010.
Outputs look set to increase further still. Kevin Fitzpatrick, Nissan’s vice-president for manufacturing in the UK, says that next year the plant hopes to move to three shifts on the assembly line as the replacement for another UK-made model, the Note, is introduced. This will take production to 550,000 units and create jobs.
But all this growth does not come cheap. The company has pledged in excess of £921 million investment in recent years. Fitzpatrick says: “We have done a lot of work to improve our cost performance and efficiency. Also we demonstrated that we are capable of producing high volumes, so investing in us is quite sensible.” The Sunderland factory has upped its game in terms of manufacturing performance, productivity and quality.
As part of the multi-million pound spend, Nissan is gearing up to produce a new electric Leaf model from 2013. The company received money for the project from the government’s Regional Growth Fund. Fitzpatrick says: “In an environment where you are competing against other plants, government support does make a big difference.”
Globally, Nissan is aiming to increase its industry share from 5.4% to 8% by 2016, and its plants will expand to accommodate that growth. Fitzpatrick says: “If you design a car that people want to buy that is at the right cost and quality then you will sell a lot, and that is what we plan to do.”
He adds that carmakers should not get complacent. The industry must continue to challenge costs and quality and to make innovative, attractive products. “If you look at ourselves and the other companies in the UK that are growing, it has predominantly been because the products are desirable and the plants that they are built in strive to improve their competitiveness. There is no magic to it.”
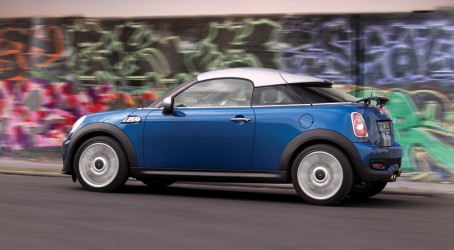
British skills secure Dagenham plant
Ford has been making diesel engines in Dagenham for 80 years. July saw the 40-millionth engine roll off the production line at the Dagenham Diesel Centre, which was opened in 2003 at a cost £400 million.
The centre makes four different engines on two assembly lines that run 24 hours a day, in a three-shift operation. Around 2,000 people work on the premises, which are partly powered by onsite wind turbines.
Ford has pledged to invest £1.5 billion over five years in the UK. Ford of Britain chairman Joe Greenwell explains that one of the reasons for doing this is the skill set that already exists. He says: “The Dagenham plant supplies 50% of Ford’s diesel engine requirements globally. To build that up from scratch is something pretty special. There is a history of design, development and manufacture here. Down the road from Dagenham, our Dunton technical centre has 3,500 engineers. They have developed fantastic expertise in engine design, which we export around the world."
Big spenders: investment by UK-based carmakers in 2011-12
BMW
Factories: Oxford, Swindon, Hams Hall near Birmingham
Model: Mini
Investment: About £750 million spent on facilities and equipment since 2011. The number of Mini models will increase to 10 and, potentially, extra production capacity will be created in Swindon.
Jobs: 5,500 safeguarded
Honda
Factory: Swindon
Models: Civic, CR-V, Jazz
Investment: Production volumes forecast to double to 180,000 units with the addition of a second shift. Mass production of the new Civic has already begun.
Jobs: 500 created
Jaguar Land Rover
Jaguar factory: Castle Bromwich in the West Midlands
Models: XF, XJ, XK
Land Rover factories: Solihull, Halewood
Models: Defender, Discovery, Evoque, Freelander, Range Rover
Investment: About £1 billion will be spent over the next four years in the UK supply chain and a new logistics facility in Ellesmere Port, Cheshire. An all-new sports car – the F-Type – will be produced at Castle Bromwich. At Land Rover’s Solihull plant £490 million is being invested to build the C-X75 all-hybrid supercar. Some £2 billion is being spent at Halewood to create the Range Rover Evoque. Halewood will expand to enable increased production. And £355 million will be invested in a new Midlands facility to manufacture low-emission engines.
Jobs: 300 created at Ellesmere logistics centre, 1,100 created at Castle Bromwich, 1,000 at Solihull, 4,000 at Halewood, 3,000 at Midlands engine plant
Nissan
Factory: Sunderland
Models: Juke, Note, Qashqai
Investment: Some £921 million in recent years, including £410 million for the production of the electric Leaf from 2013, £127 million to produce an as yet unnamed mid-sized model, £125 million to produce the Invitation and £192 million for the new Qashqai.
Jobs: 625 created at the Sunderland plant and 2,375 within the supplier base
Toyota
Factory: Burnaston, Derby
Models: Auris, Avensis
Investment: About £100 million to produce new-generation hatchbacks.
Jobs: 1,500 created
Vauxhall
Factory: Ellesmere Port in Cheshire
Model: Astra
Investment: Investment: Some £125 million to continue manufacturing at Ellesmere Port. Production of the new Astra is set for 2015, with the plant running three shifts.
Jobs: 700 created