Bob Joyce has a spring in his step and it’s not hard to see why. As group engineering director at Jaguar Land Rover, Joyce is responsible for driving technology and innovation within a company that, in recent years, hasn’t seemed to put a foot wrong.
New models, such as the Range Rover Evoque, have been launched to international acclaim and are flying off dealers’ forecourts. A huge £365 million low-emissions engine plant is under construction at a site near Wolverhampton. And only last month, the company announced that its Halewood plant on Merseyside would be switching to 24-hour operation, creating 1,000 jobs. This truly is a golden period for Jaguar Land Rover (JLR).
No wonder Joyce seems happy about the way things are going. “Ultimately, it is the products that are put into the marketplace that stimulate engineers who work in the automotive business, and with the Evoque we knew from the start that we had designed and built a very capable car,” he says from his office at JLR’s Whitley engineering centre in Coventry.
“It is most satisfying to see that the Evoque has won more than 80 awards, and to win Truck of the Year in the United States was absolutely fantastic. We have also been really pleased with our model launches within Jaguar, and there have been many technology innovations like the first stop/start on a traditional diesel auto – Jaguar XF,” he adds.
Joyce is a career engineer, who through the first half of the 1990s, held positions as chief engineer of Rover’s K-Series engine family, director of the Gaydon technology centre, and body engineering director of the Rover Group. He then progressed to roles including senior vice-president of BMW front-wheel drive platforms, before being involved with the highly successful new Mini project, which he took through its development process.
More recently at JLR, Joyce has overseen the development of the complete range of vehicles including the Range Rover, Discovery 4, Range Rover Sport, Freelander 2, Jaguar XK, XF and the all-new XJ.
With such an illustrious background, it’s no surprise to find him vocal on the central role that engineers have played in JLR’s recent success story. “We have a very strong engineering backbone in this organisation, and I find that highly motivational,” he says. “We are in the premium car business and to be successful in that sector you’ve got to have engineers to help lead the business.
“The majority of our engineers are working on projects in the four-year horizon and we have a very exciting portfolio of products coming forward over that period. And then there’s another tranche of our engineers who work further into the future in the six- to 15-year horizon. I can’t be specific, but they are working on some very advanced technologies where we have made great progress since we have become a standalone business under Tata.”
The engineering resource within JLR has been expanded of late to meet growing demand. The company now employs 4,000 engineers in the UK, while another 1,000 work under contract, with the same number again employed overseas. JLR typically takes on 200 graduates a year and has reinvigorated its apprenticeship scheme.
Joyce says that, while it is hard to find enough technical talent in areas such as software and advanced computer-aided engineering, he is happy in the main with the diversity and depth of skills within the expanded organisation.
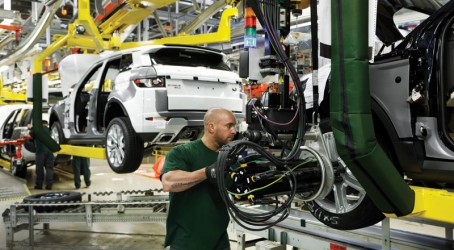
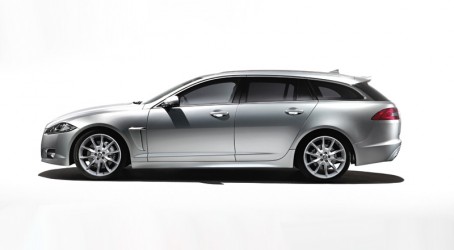
“We have found a lot of very good people out there – far more than we at first thought would be available,” he says. “It isn’t ever easy but you’ll be amazed where there is talent. When we embarked on our growth of capacity, which was nearly 1,000 engineers over the past two years, we found a lot of exceptional people, whether graduates or more experienced candidates.”
In time, that engineering resource will change as sales to emerging markets, such as India and Brazil, continue to grow and the company seeks to get closer to its customers. Joyce is guarded when commenting on future work patterns, insisting that the company is completely committed to the UK as home to its core manufacturing capability. But he says that JLR needs to take a global view, and that will mean creating jobs in other countries.
“We have already announced manufacturing plans in Brazil and India and a joint-venture partnership in China. We will inevitably increase our capacity in these countries, particularly in the joint venture where we share the development of new cars. In India, we have 800 engineers working there as we speak. We will be growing that to over 1,000 as we design and engineer in India.
“There are some areas where we are woefully short of skills in the UK – software being one. JLR is part of the Tata Group and there are certain divisions of Tata which have very high skills in software. It would be crazy for us not to exploit that.”
Joyce points towards JLR’s confirmation of a multi-million pound investment in a new facility to manufacture all-new, advanced technology, low-emission engines at a site near Wolverhampton as proof of the company’s long-term commitment to designing, engineering and manufacturing in the UK. The plant will build a family of four-cylinder engines for future Jaguar and Land Rover models, a development programme that will help the company deliver on a stringent process of vehicle emissions reduction. The engine manufacturing facility will create up to 750 posts at JLR, along with thousands more jobs in the supply chain.
Some industry commentators were surprised that JLR had chosen to build its own range of engines, rather than forming a joint venture with a specialist supplier. But Joyce says the strategy enables the company to be the master of its own destiny when it comes to engine development. “We couldn’t afford to be laggards in the engine-making business,” he says. “We require a very high volume of engines and it would be crazy not to take control of design and manufacturing to protect our future.”
Joyce also thinks that, by having its own engine plant, JLR will be in a position to guarantee product quality and to react more quickly to new trends, such as the move towards increased hybridisation. “It is vital that our engines are totally aligned to the platform architecture strategies that we implement across Jaguar and Land Rover,” he says.
Engine technology is an area of rapid progress at present, and Joyce thinks that makes now a particularly fulfilling time to be working as an automotive engineer. The core trend is downsizing to families of three- and four-cylinder designs that can run at some very high specific outputs. But he says that these days engines are only one link in a longer chain, with more sophisticated drivetrains, automatic gearboxes and more complex electronic controls adding to the mix.
“Torque management of the wheels is becoming very complicated, and we are seeing a lot of torque vectoring systems with ABS. Then when you add hybrid systems – electric and plug-ins – the power pack starts to become a very integrated system. We have done a lot of work to make sure our electronics and the supplier vendor selection gives us the best chance to integrate all these different technologies as one.”
Joyce says the greatest challenge to automotive engineers will be to drive down CO2levels year-on-year. “There is a lot of diverse environmental legislation in all the different markets, but, fundamentally, we see a requirement for year-on-year fuel economy improvements of between 5.5% and 6% across all cars, on average.
“We will get to a tipping point where electric vehicles – plug-ins, hybrids – become sensible. I think they will become sensible in the city car application, but also potentially in the premium car sector where a hybrid range, extended with products like our Range-E, makes quite a lot of customer business sense,” says Joyce.
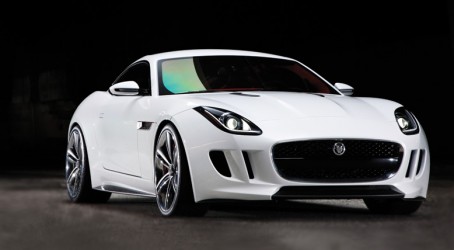
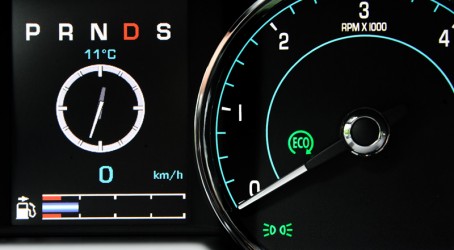
“Also, we have all lived with a massive improvement in infotainment and electronics. In the iPhone and cloud world, where we live, there’s a lot more computing capability, requiring the need to take an awful lot of data, crunch it through, and come up with a result. So how that applies to in-car communications systems is exceedingly challenging. We had more electronics engineers work on our new XJ Jaguar than we had on the whole mechanical hardware of the car,” he adds.
“Just in the infotainment system we have 10 million lines of software code. All of these areas are really exciting and it is clear that the cars of the future will be significantly different to what we see on the roads today.”
That’s not to say that advances will not be made in other areas, such as materials, driven by the need to reduce weight. JLR is a key player in the use of aluminium on Jaguar models.
Joyce says the company will increasingly be looking at using the material on its Land Rover products. “We are very proud that we use aluminium to get our bodies down to a substantially lighter weight than they would traditionally be in steel.
“Beyond that we are also looking at composites for specialist applications – typically smaller vehicle-type programmes but also on very specialist super-car developments, such as the CX75.”
Work is also ongoing in the novel area of micro gas turbines for automotive and industrial applications. JLR has been involved in a collaborative project with small British firm Bladon Jets that has led to the development of two 70kW micro gas turbine engines which have been featured in Jaguar’s CX75 concept electric sports car. Using Bladon Jets’ ultra-lightweight range-extender technology, CX75 has a top speed of more than 200mph, doing 540 miles on a 60-litre tank of fuel. Parent company Tata is also interested in developing micro gas turbines for power generation in emerging economies.
Joyce says that the Bladon Jets project is just one of a number of very exciting motor, battery and range-extended technologies that JLR is evaluating. “There are some great start-up companies in the UK but historically many of them have not found a route to market. We hope to be a route to market in the UK and in the wider world.”
Joyce says Bladon Jets’ technology holds real potential. “The key issue is to come up with a manufacturing business equation to get the economies of scale. It’s a very high-precision, compact unit, and development is going well. But it’s actually about getting it across from the work bench and into an application. However, we have identified a couple of really serious opportunities to get significant economies of scale to launch that technology versus more traditional diesel/petrol auxiliary power unit applications.”
Looking to the future, Joyce has a busy in-tray. JLR is on record as saying that it will develop 40 new products during the next five years, resulting in smaller, sportier Jaguars, such as the C-X16 concept car, while it is still working on the development of the C-X75 supercar. On the Land Rover side, there is expected to be a tranche of new vehicles to replace existing models.
So Joyce will be overseeing the team of several thousand engineers who will deliver these new programmes. But he revels in the pressure that brings. “I love it, I’m having a great time.”
He says that JLR’s current golden period isn’t down to luck – it comes as a reward for investment and commitment, particularly during tough times. “We’ve gone through different ownership but we’ve had a consistent focus on great cars that drive profits and returns,” he says. “We went through a tough recession two or three years ago but we never took our eye off the ball. It’s pleasing now to see the world responding accordingly and liking our cars.”
Jaguar and the IMechE
Jaguar Land Rover has forged close ties with the IMechE over the past couple of years. A memorandum of understanding between the two organisations has seen the automotive company promote the benefits of IMechE membership to its team of engineers, while the institution provides a range of services aimed at supporting technical accreditation.
Jaguar Land Rover also sponsors the Spen King Sustainability Award in memory of Charles Spencer King, the mechanical engineer who was the mastermind behind the Range Rover. The award, in conjunction with the IMechE, is designed to inspire and encourage the next generation of engineers.
Last year, the award was presented to Sophie Wakeford, an undergraduate embarking on her degree in mechanical engineering at Oxford University. Wakeford will receive £1,000 a year while reading for her degree and will take up a summer work placement at the company in her area of interest, hybrids and environmentally sustainable transport.