Engineers drive the future, accountants don’t. We all know that’s true, but it is nice to hear, especially when it comes from someone as influential as Bob Joyce, group engineering director at Jaguar Land Rover. Those few words go a long way to explaining the stellar success that the company has enjoyed in recent years.
Joyce attributes that performance to one simple factor: Jaguar Land Rover (JLR) has been producing great cars. And to keep achieving that, he recognises that it has to trust its engineers to deliver vehicles that the public wants. “We have let our engineers take a more prominent role in the company,” he says. “JLR really has become engineering-driven.”
That engineering-led ethos has been particularly cultivated at JLR since 2008, when it was acquired by India’s Tata Motors. At the time of the deal, many industry commentators feared that JLR would struggle to retain its independent spirit within a global, diversified group and that, worse, it might be starved of adequate investment. Those concerns have proved unfounded: JLR has thrived under Tata’s ownership and in many regards has grown to become the jewel in the crown of its global business.
Joyce says it has proved to be a healthy relationship, with Tata’s flat management structure providing an agile model when it comes to investment decisions. “Tata runs a very hands-off business style,” he says. “They basically say ‘get on with it’. We’re fortunate in that we don’t have to go through committees. We really don’t have the politics that you usually get within large organisations.”
He also says that being part of a global conglomerate has proved a boon. In recent times, for example, JLR has struggled to find the engineering software skills it requires in the UK. Being part of Tata has enabled it to tap into resources in India to meet any shortfall.
“Tata is a massively impressive business,” he says. “We have good relationships with other firms within the organisation. It has proved to be a very significant brotherhood of companies, and it’s up to each company to best realise how we can all work together.”
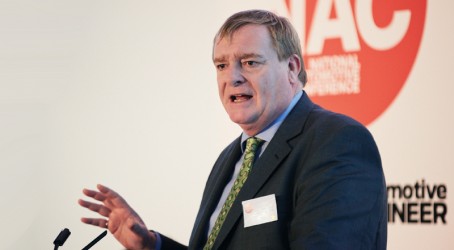
These solid foundations, combined with the engineering-led ethos, have delivered astonishing results, with JLR’s three UK carmaking factories now at bursting point. In 2008, the company was under-capacity, producing around 190,000 cars a year. Now, that figure has risen to an incredible 350,000 cars. The Halewood plant in Merseyside has moved to three-shift, 24-hour production to meet demand for the Evoque and Freelander models. Production at Castle Bromwich in the Midlands has surged to 180,000 vehicles a year, making the new Jaguar XF Sportbrake estate car and other models. And the Solihull facility, meanwhile, is to benefit from a £370 million investment to enable it to keep up with demand for the Range Rover, Range Rover Sport and Land Rover Defender.
It’s a similar tale overseas. “We clearly have to expand in overseas markets,” says Joyce. “We have got a clear interest in China where we have already announced joint venture partnerships, and being part of the Tata Group gives us great opportunities to get into India.”
JLR has also streamlined its manufacturing strategy to improve efficiencies. Joyce admits that when it was owned by Ford in the early 2000s, the firm was guilty of having far too many platforms, including legacy platforms from Honda, BMW and Ford. Now the firm has just three core platforms and two architectures, with greater commonality. The new Range Rover is based on the D7U platform, and Joyce says that more cars will come off of that, including, intriguingly, a smaller vehicle, possibly the next-generation Discovery.
So with its three plants in good shape, meeting demand for record sales, it’s tempting to think that JLR might rest on its laurels. But nothing could be further from the truth. Across all areas of the business, from lightweighting to emissions reduction, vehicle styling to the trend towards greater electrification, JLR’s engineers are working hard to ensure that recent momentum is maintained.
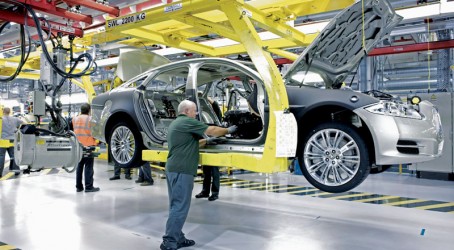
One area of immense research and development effort is how cars might adopt the sorts of interactive communications and entertainment technologies that consumers have grown to expect. Joyce says infotainment has become a crucial area for the company, taking up enormous engineering resources. “Cars have become more connected but, trust me, we are only just on the wave of the next generation. Touchscreens, phones, the cloud, telematics and the connected world are going to transform the cars we drive.
“Within JLR, we have grown our infotainment team from eight people when we were part of Ford to more than 400. The software for the infotainment for our current cars is 10 million lines of code – that’s twice as much as in the engine management system.”
So how might research activity in this area play out? Joyce is understandably coy about that, but, for example, he thinks that consumers increasingly expect their smart phone to interact seamlessly with their vehicle’s infotainment system. “We have very focused route-to-market roadmaps in this area,” he says. “We have to open ourselves up to the cloud, and we will be doing that shortly.”
A second area of intense research and development effort is around lightweighting. JLR is pursuing the trend towards downsizing to meet stringent emissions reduction targets, shifting from V12 to V6 and V4 engines, without any loss in vehicle performance. That magic formula can only be achieved if advancements can be made in several tandem areas of technology, including lightweighting.
Those efforts are overseen by Mark White, head of materials at JLR. He says that, broadly speaking, JLR wants to produce cars that weigh less than 1,500kg and SUVs under 2,000kg. Longer term, those figures need to come down to 1,000kg and 1,500kg respectively.
How might that be done? Well, JLR believes that there is still some weight-saving potential from the development of new steels. “We can probably still get a 10-20% weight reduction potential in the body of a chassis from new high-strength steels,” says White. “For example, we saved 70kg on the Evoque versus the Freelander through the use of next-generation ultra-high strength steels.”
But to make real leaps in weight saving, JLR will continue to pursue the wider use of aluminium and the further introduction of more exotic metals such as magnesium. “We believe that with aluminium we can get at least a 40% weight saving, technically 50%,” he says. “And then there is magnesium, that offers further weight reductions, possibly another 10% over aluminium. But magnesium has some issues with joining and erosion and other challenges. So at the moment magnesium is still restricted to use for bolt-on components such as front-end carriers and cross-car beams.”
Looking further forward, JLR says carbon fibre and reinforced plastics bring real potential for lightweighting on the body and chassis. However, at present, carbon fibre is prohibitively expensive for all but the makers of very top-end supercars. The Aston Martin One 77 coupe, for instance, features a full carbon monocoque chassis that reportedly costs a six-figure sum per vehicle. Other carmakers such as Lamborghini and McLaren have also launched supercars with extensive carbon-fibre content.
White is realistic about the impact that carbon fibre will have on more mainstream markets. “Over time costs will come down,” he says. “But even using the very best roadmap that the car industry has got, we still think a sub-£10,000 carbon-fibre structure for a new premium vehicle is going to be a challenge, and to get down to the low thousands of pounds will require a concerted effort.”
Efforts to increase carbon-fibre content are under way, and will feature on the CX75 hybrid-electric, two-seater prototype. JLR is experimenting with carbon fibre on the tub and frame and on the cross-car beam, undertrays, bumpers, seat-frames and on some of the trim. “The CX75 is our own concept – we are looking at what the weight-saving potential versus the cost might be,” says White. “We want to know what the barriers are to producing something like a future XK with carbon-fibre content in volumes of between 1,000 and 10,000 cars. And going even further into producing maybe a city car somewhere in the future.
“It’s not just about the technologies and fibres – it’s also about finite element analysis, making sure we can create these cars in the virtual world, and also doing lifecycle analysis – it’s got to be recyclable.” Furthermore, JLR is involved in a project with the Technology Strategy Board to produce a carbon-fibre body structure for a Range Rover Evoque. “That might give us a car that looks and drives like an Evoque but with a much lighter body and a smaller engine.”
So, from connectivity to lightweighting through the use of advanced materials, it’s clear that across the business JLR is making huge efforts to ensure it keeps producing great cars that customers want to buy. The final words go to Bob Joyce, who reiterates why this straightforward approach is so important. “Great cars mean great business results. Bad cars mean bad business results. It’s a simple metric but it is the truth,” he says.
Jaguar Land Rover engine plant takes shape
Jaguar Land Rover’s new i54 engine factory is starting to take shape on a site alongside the M54 in Wolverhampton. The facility, which will be completed in 2014, will build new-generation Hotfire petrol and diesel four-cylinder engines in volumes of around 300,000 units a year. Enough land is available to erect a second facility on the site to double the output.
According to Bob Joyce, group engineering director, the four-cylinder Hotfire engines will become a key feature of the company’s strategy. JLR recently launched the XJ (2-litre gasoline) and XF (2-litre gasoline and 2.2-litre diesel) cars with four-cylinder engines, and Joyce sees this trend continuing across the whole range of vehicle products. The company will retain the V8 engine, but to suit the new lightweight architecture JLR will build a 250bhp four-cylinder engine, linked to a modern transmission.
Joyce says gasoline and diesel technologies are merging. All new JLR engines will have high-pressure injection, accommodating similar loads at their bottom ends. Further evidence of merging technologies comes with news that Ricardo has developed a gasoline engine that even beats the benchmark for a 1.6-litre diesel.
The i54 engine plant will cost £355 million and will be capable of producing an engine every 36 seconds. The plant will employ 750 personnel. And, according to senior purchasing manager Alan Edwards, it will support 3,000 jobs in the supply chain. Last year JLR spent £4.5 billion in its supply chain, with 60% of that in the UK. Some suppliers will locate facilities nearby to supply components “just-in-time”. The engine facility will occupy 828,000ft2. A new £36 million slip road will link the plant with the M54.
Edwards stresses that JLR needs to “take control” of its own engine supply as current suppliers cannot meet the growing demand. Ford is a big engine supplier. “There may be satellite engine facilities in other countries but the engine plant on the i54 site will be the home of our engines,” he says.
The frugal Hotfire engines are the focus of intense research work in universities such as Warwick and Loughborough. Professor Lord Kumar Bhattacharyya, the chairman and founder of Warwick Manufacturing Group, has close links with both JLR and Tata.
JLR expects four-cylinder engines to account for 70% of output, compared with just 20% before the launch of the Range Rover Evoque. According to Joyce, Hotfire is modular with capability to cover all cylinder configurations and “a few more interesting ones between three and six”.
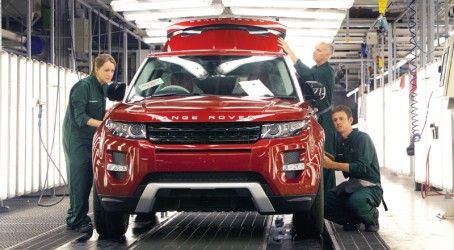
Providing the skills for an expanding empire
Warwick Manufacturing Group at the University of Warwick has entered an agreement with Jaguar Land Rover to teach up to 600 of the carmaker’s employees to degree level.
Up to 100 JLR staff will take up their places as sponsored students in October this year and next, studying either product development engineering or manufacturing engineering degrees.
From 2014, Warwick Manufacturing Group (WMG) will also support the degree provision for the higher apprenticeship programme. This means that there will be up to 600 students studying at various stages over the next three-to-four years.
The teaching will follow two main paths: manufacturing engineering or product development engineering. For the higher apprenticeship programme, modules related to finance, supplier management and other commercially related topics will also be included to support career progression within JLR.
In addition to lectures, seminars and tutorials, students will have access to an internet-based “managed learning environment” and will undertake “activity-based learning” in the laboratory. WMG and Jaguar Land Rover are working together on curriculum development.
WMG chairman Professor Lord Kumar Bhattacharyya said: “WMG researchers have worked for many years transferring the latest technology into the creation of world-beating premium vehicles. We also have long experience in delivering engineering teaching, at a range of levels, to major manufacturers and engineering companies. This new programme will use WMG’s teaching experience to empower a wide range of JLR staff with the skills to make best use of their company’s advantage-building technology.
“The programme will be the first of its kind in the UK.”
Dr Ralf Speth, the chief executive of JLR, said: “Jaguar Land Rover has ambitious growth plans which can only be supported by innovation in products, engines and environmental technologies. We are investing in developing the skills of our engineering teams to ensure they have the knowledge and insight to help drive the business forward.”
Meanwhile, JLR has launched a campaign to recruit more than 150 apprentices to join its 2013 training programme. This includes about 90 advanced and 60 higher apprenticeships.