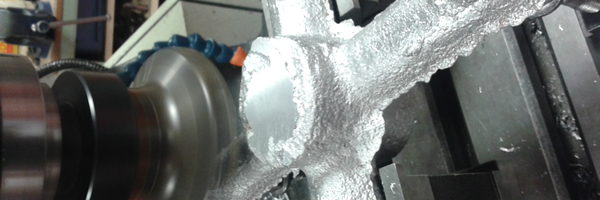
Apprentices and engineers at Delphi Diesel’s Suffolk factory have taken part in the British Pedal Car Racing Championships, organised by the British Federation of Pedal Car Racing (BFPCR).
Delphi entered its first pedal car at the end of the 2012 season. Taking part for the first time was an eye-opening experience, according to apprentice Sam Osborne: “The range of expertise and experience among the teams taking part was immense. We had designed and built a car from scratch, and were proud of what we’d achieved, but we learned a lot from seeing the other models and competitors. After that race we went back to the drawing board.”
Delphi’s team, which is based in the training school and comprised of apprentices and engineers with a range of skills and experience from across the company, re-thought the car. The project forms part of the day-to-day structure of learning, and Sam observed that adaptations were carried out from top to toe: “Our experience at our first race didn’t discourage us, it encouraged us to rethink, adapt and refine the design. Our original car was too heavy, despite being made from aluminium. We had focused too much on strength, which burdened us with weight. We now have a tubular aluminium shell, and we have changed the braking and drive systems, used lightweight wheels, and different steering.”
Sam explained that the shared value behind the project is teamwork. “It’s a company-wide project. It’s literally one team made up of apprentices at different stages of their training, as well as those in the factory with specialisms, such as welding, adding in their expertise.”
“Initially, to scope the requirements of building the car, all the apprentices and others from within the factory came together to brainstorm ideas for design, materials and mechanisms. This was a good base for everyone to start from, after which we began to work up the different elements.”
Roy Engle, training manager at Delphi, found that the pedal car Championships slotted in with many of his students’ interests: “With so many of the students into cycling and cars it was a natural project to bring the apprentices’ ideas together and get them working towards a common goal.”
“Our apprentices have brought different ideas to the project and through planning, designing and building the pedal car the guys have experienced milling, turning, welding and, in one of the details, casting. The occasions when the guys have come up against unexpected issues makes you realise that, although some are relatively inexperienced, they have some very creative ideas. Without projects such as this, many would not have had a chance to try out these processes or show their talents.”
Roy gave an example of the way the project stretches his team: “Luke Bucksey (one of our apprentices) cast the main pedal support and then subsequently machined it in the training school. The experience gained doing this, because of building the pedal car, pushed the boundaries of normal expectations at this stage.”
Lara Mallet, Business Development Manager for the Institution supports Delphi’s engagement with this project. She commented: “It is great to see a team effort from the engineering staff at Delphi Diesel. In particular for the apprentices, this experience helps to meet the Engineering Council competences for Engineering Technician.”
Sam said that a couple of elements have posed the greatest challenges:
“One of the things that has been hard to get right is to do with the drive. There are three different chains, which have to be perfectly aligned. They are sensitive and vulnerable to coming off. Now we have refined the adjusters they are functioning a lot better. Steering was another challenge. As aluminium is such a light metal, it was prone to softening as the steering impacted the car, wearing the aluminium itself. We’ve come up with a few different solutions to address that.”
The races are over for the year (the last one was in August) and the next season starts in March. Between now and then the Delphi team is still testing and adapting the car, and aiming to get another model made, too. Some of the races are 24 hours long, which has a major impact on a vehicle. Sam mentions the aim is to continually progress, both in performance and adaptation of the pedal car.
Crediting the BFPCR with great support and organisation of the races and Championship, Sam argued that the camaraderie at the races is a big part of what makes competing enjoyable: “The atmosphere at the events is competitive, of course, but also very encouraging. People are happy to give a helping hand, impart some advice, sort out any mechanical issues and share tools. It brings everyone together.”
“The support we’ve had from the BFPCR has been great, they organise the events really well and also are in touch if we have questions. In some ways, I thought the race events would be more highly competitive and teams would be secretive, but the ethos is great. It’s about sharing knowledge, not just within our company but also between competitors.”
“Initially we weren’t sure what level of fitness was needed to race the car, but if you do some training it definitely pays off! There are a few keen cyclists in our team, which helps. In some multi-driver races, you need to get drivers in and out of the car at pit-stops. It’s a question of finding a balance between the time lost in a change-over and the exhaustion factor of keeping someone in the driving seat!”
Sam is in the second year of his apprenticeship and explained that he is very much enjoying life at Delphi: “Since my early teens I have been interested in motorbikes and mechanics, and after hearing about the scheme here, I applied and was offered a place. I am delighted to work here. Between years two and four apprentices go on placements around the factory, slowly focusing down the range as the end of your apprenticeship approaches.”
Having just started his first placement in the training school, it’s all ahead of Sam at this point, so he’s keeping an open mind about where he’d like to specialise.
Summing up the value, to him and to others, of taking part in the British Pedal Car Championships, he said: “Ours is a big team, and a great team effort. What the pedal car project has done is bring people together and combine their effort, expertise, knowledge and learning. It boils down to teamwork, which is one of the great skills that engineers need. We’re mucking in together – new apprentices and experienced engineers – a chance for everyone to get to know each other through a shared experience. We’re all on the training floor together with a common goal.”
To find out how the Institution supports company apprentice schemes or individual apprentices 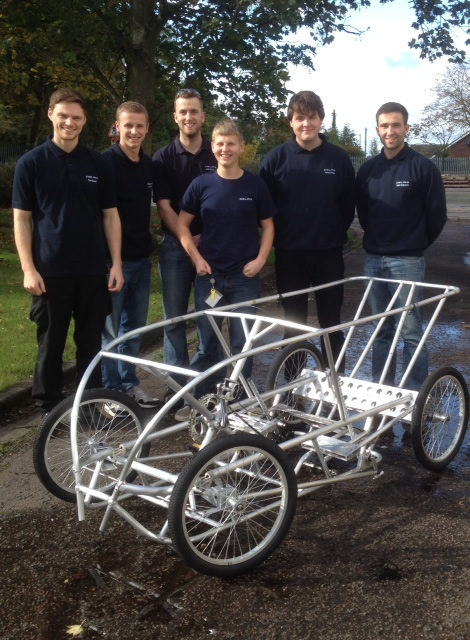
For more information about BFPCR: http://www.pedalcars.info/index.asp