At the Dounreay nuclear facility on Scotland’s north coast, engineers are about to embark on an astonishingly complex decommissioning project that is the unfortunate legacy of ill-advised decisions made many years ago. Back in the 1950s, when Dounreay was home to the UK’s fast-reactor research efforts, a 65m shaft was excavated for the removal of rock spoil from undersea tunnelling related to the site’s effluent discharge pipes. But the government later authorised it to accept intermediate-level nuclear waste. And so, over the course of the next 20 years, the shaft acted as the Dounreay dump, with more than 750 tonnes of radioactive material tipped into the flooded abyss below.
Little thought was given to how the contents of the shaft would ever be cleaned away. And inventory-keeping was sketchy, at best. The result, now, is a tangled mess of waste, covering a broad chemical and radiological spectrum, submerged in a column of filthy sludge.
Steve Efemey, from Dounreay Site Restoration, is one of the engineers charged with cleaning up this mess – work that will cost £100 million. “It’s one of the most technically challenging decommissioning projects in the UK,” he says.
“The waste retrieval, treatment and storage work will all have to take place inside a shielded cell. That will involve the extensive use of remotely operated equipment, working at-depth in what will be an extremely difficult environment. And, to be honest, we’re not 100% sure what we will even find down the shaft.”
The shaft is largely unlined and cylindrical in shape, measuring up to 4.6m across and 65.4m deep. A nearby wet silo was also used until 1998 as a storage facility for intermediate-level waste. This too will need to be decommissioned. The silo – a concrete-lined and roofed box built just beneath the surface – comprises two interconnected compartments and is more than 9m deep, 8.5m wide and 10m long, with a storage capacity of 720m3. Each compartment has a concrete roof more than 1m thick.
The waste consigned to the shaft and silo came from various plants and facilities across the Dounreay site and elsewhere around the UK. The resulting waste is now thought to comprise many solid items such as sealed cans plus sludge from a Dounreay pond clean-up. But, as Efemey admits, no one is really sure what will be found until the clean-up work begins.
“There was an inventory compiled for each disposal, but there is also anecdotal evidence of disposals being carried out on the back shift,” he says. “The description of the waste is also rather sketchy. Some of the entries just say ‘one can of waste’ – which isn’t too helpful. Disposal of the waste was mixed as well – so we are not sure exactly what we will be pulling out, and when.”
A decision was taken in the 1990s to empty the shaft and silo rather than seal and leave them in-situ. The first step was to isolate the shaft from groundwater by grouting the rock fissures around it and creating a grout curtain to reduce ingress, minimising potential contamination.
This work involved the construction of a raised working platform, reinforcing the plug and the horizontal section of liquid effluent discharge tunnel attached to the shaft, and drilling up to 400 boreholes around the shaft to a depth of 80m, in a boot shape. A fine grout was then injected at high pressure into the boreholes, to form a barrier and create a giant containment around the shaft and side tunnel. This considerably reduced the amount of water getting into the shaft. This grout curtain was completed in 2008.
The next stage is the highly challenging removal, treatment and storage of the waste, estimated to total 1,220m3. Recovered waste from the shaft and silo will be processed for long-term interim storage within shielded containers on site.
Work on the shaft will commence with the construction of the waste recovery headworks, comprising a crane and a combination of industrial grabs and robotic mechanisms that can be lowered into the shaft to recover the waste. Petal and clam-shell grabs will be deployed to retrieve waste from the full 65m depth. The crane will have X-Y traverse capability so that, although it is anticipated that the waste will slump down into the shaft as it is recovered, complete coverage of the cross-section of the shaft can be ensured. The crane will also be specified to ensure that it can retrieve any weight of waste that it is likely to encounter.
The challenges are considerable – high radiation levels preventing manned access for routine and remediation operations; the difficulties of retrieval from a vertical shaft at considerable depth; and the need to deploy equipment almost 20m into the side tunnel. Further, there is a requirement for a system to manage any grabs that snag on the waste. This is in addition to the challenges associated with the supply of hydraulic and electrical power, which become greater as the retrieval point gets deeper, with the hose and cable management deployment mechanisms having to increase in size and strength. Equally, the deployment of lighting, camera systems and monitoring equipment also becomes more complex as depth increases. All equipment used also has to be radiation tolerant.
Once the shaft is cleared, a remotely operated vehicle (ROV) will need to be deployed into and along the full length of the side tunnel, along with all the ancillary power and control systems required. The retrieval of waste from the tunnel back to the shaft and then to the surface will also be a complex and time-consuming procedure.

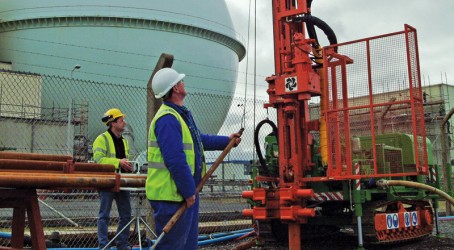
Despite such complexity, Efemey is convinced that the project has been well thought-out and is technically deliverable. “Actually, the grabbing equipment, such as the petal and clam-shell grabs, are fairly commonly used in dredging operations,” he says. “It’s fairly standard kit. It’s the same philosophy for the silo. There will be a crane over the silo. We take the roof off to give us access, and grab the waste.
“If a grab gets snagged up in the waste, then it will be recovered with what we call the shaft intervention platform. This platform will have manipulators on it to cut the waste and free the grabs. We have considered a number of failure scenarios. The intervention platform even gives us the facility to ditch grabs that get snagged and remotely change the tools on the end.
“But there will be tough tasks along the way. We know, for instance, that there is waste in the shaft that is stuck to wire mesh and we know that there is pipework fixed to the shaft wall. Dealing with these sorts of things will require more dextrous manipulations. And when we get to the bottom of the shaft, we then have the stub tunnel to deal with. Here we plan to use a remotely operated vehicle which will be manoeuvred to help carry out the grabbing operations.”
Other technical issues will come into play. For example, as the retrieval depth increases and the water level within the shaft is lowered, the differential pressure between the water table and shaft water level will increase, which will cause an increase in inflow into the shaft, in turn placing a greater burden on the downstream liquid effluent treatment plant. The facility will have to process differing amounts of effluent from the shaft as the water level differential increases during waste removal activities.
A sludge retrieval system will have to be deployed down the shaft, enabling localised pumping into a containment tank, which can then be brought to the surface and connected into the main treatment process. “It would be very difficult to pump sludge from 65m depth to the surface,” says Efemey. “So we have designed a deployable sludge retrieval system that can be suspended off the crane.”
The physical location of the facilities, and proximity to the coast, bring their own challenges. A reinforced-concrete working platform has been built that will provide protection from the encroachment of the sea, and provide a secure base on which to mount the retrieval structure, plant and processing equipment. Selection and design of the overbuilding will take into consideration the harsh weather conditions that prevail at Dounreay.
In line with the programme policy, a limited-life structure will be erected, incorporating shielded areas for waste retrieval, processing and packaging, waste characterisation, and sludge conditioning. This will include an industrial crane, a modularised ventilation extraction system with HEPA (high-efficiency particulate air), and modularised processing plant and equipment.
Waste retrieved from the shaft and brought to the surface will be segregated, characterised and processed for interim storage. This represents another key challenge, with a number of issues to be addressed before consignment for storage.
The waste will be sorted using ROVs with power manipulators and an assortment of end effectors for sizing and handling items. Waste will be segregated into solid and effluent streams, using equipment including a shredder and size-reducing tooling to shred and screen the debris and cut large items.
Waste characterisation at this stage will use gamma and fissile monitoring systems to ensure that all material is processed in accordance with the letter of compliance (LoC) regulatory process. The physical and chemical composition of the processed waste will also have to meet the conditions defined in the LoC, and product trials will be conducted to ensure that the wasteform meets those requirements.
“All work will be carried out in a shielded cell with no man access,” says Efemey. “Any crane failures have to be recovered remotely as well. Once we get the waste to the surface we will then be using remotely operated vehicles to cut and characterise it, while also using an industrial shredder to reduce it down further. Much of this work will be done under water spray to help passivate any residual chemicals in the containers.”
All wastes retrieved will be conditioned and encapsulated or immobilised within self-shielded containers using a cementitious matrix. The containers used will be dependent on the waste type. The containers will then be transported for intermediate storage on-site in full compliance with regulatory requirements.
Recent changes to contractual arrangements at Dounreay mean the project is now the focus of “renewed emphasis”. The work is now at concept design stage. Key milestones following achievement of concept design at the end of 2012 will include commencing construction in the autumn of 2013 and initial operations in mid-2015. The aim is to finish all the works by 2021. Efemey says: “We have done a number of trials with varying bits of equipment in terms of retrieval and waste treatment. The techniques that have been proposed for sludge treatment have all been used before in other decommissioning projects. So we are relatively confident that all the technology is in place.
“The real challenge is interfacing with the large number of contractors that we have and integrating all the different bits of kit together to operate as a whole. There is the intervention platform, the ROV, the crane, the characterisation equipment – we have a number of procurement packages coming out over the next 12 months. The headache will be integrating them all together.”
But Efemey is confident that the 2021 deadline for the shaft and silo project can be achieved. “The end game after the project will be just two or three waste stores left on the site. It’s a very challenging programme and we are on the critical path to completion.
“We are making good progress and are confident that we can deliver on time.”