As engineers grow more comfortable with the concept of accessing services remotely through the cloud, so 3D design companies are looking to build on the range of products delivered in this way. The trend is leading to the creation of “pay-as-you-go” business models that give smaller firms the chance to use the high-end tools that otherwise would be too expensive because of hefty upfront costs.
The approach is working particularly well in simulation, which for years has been viewed as an expensive, time-consuming and complex add-on to the design process. Now, because of more flexible licensing arrangements available by accessing software as a service, combined with the additional computational power that can be delivered through the cloud, engineers are starting to carry out simulation earlier in the design process. This strategy has the potential to save money and enable companies to bring products to market in a shorter timespan.
“The cloud is bringing simulation software to the masses,” says Wasim Younis, a simulation specialist at Symetri, an engineering data management firm. “Eventually, all computer-aided design (CAD) users will be able to access top-spec analysis software. It has already become simpler to use.”
Simulation software is nothing new. For many years, it has been enabling designers or engineers to conduct physics-based simulations to predict the performance of new products and to investigate and remedy the failure of older models. The problem, says Younis, is that it has always been expensive, so only large organisations have been able to afford full-time simulation specialists to develop the right methods for their own particular products.
There have been attempts to introduce simulation skills to mainstream design engineers, but often the tools used could carry out only simple linear analysis on single components. Many manufacturers have, therefore, continued to use specialists and to handle simulation in an inefficient, serial-design-prototype-test-redesign cycle.
At the same time, product complexity has grown and even greater levels of computing power have been needed for multi-physics analyses – often exceeding the scope of the desktops and workstations used by most engineers.
“Simulation has, traditionally, been complicated to use,” says Younis. “You had to be using it all the time to grasp what to do with it.”
Another drawback was the amount of computational power required to carry out even the simplest calculation. On standard desktops or workstations, analysis of a single component could take an inordinate amount of time. “Computers could be clogged up for days or even weeks, at a time,” says Younis.
“What the cloud brings is infinite computer power. So, when engineers or designers come up with a product, they can use the simulation software to go through as many ‘what if?’ scenarios as they like. The cloud gives engineers the ability to design whatever they want.
“Once the file goes to the cloud, you don’t have to worry about it. You can carry on working and, once the calculations have been completed, it is downloaded again and then you are notified.”
But all the factors are now in place to open up the world of simulation to a far wider market, enabling firms of any size to take advantage without a substantial capital investment. The first stage in this process was the growth of digital prototyping: the development of 3D models that not only look like the real thing, but also act like it too, with the utmost accuracy.
The next step has been the integration of simulation tools within mainstream geometry-creation software. For example, the 3D geometry that enables digital prototyping can, in most cases, be used by the automatic meshing tools in finite element analysis software. Further analysis tools, such as computational fluid dynamics, have also been added.
Working with integrated CAD and simulation tools enables associativity – when the design model is changed, the simulation model and analysis are revised accordingly. This opens up the possibility of experimenting with design variants without the need for lengthy updating throughout the design and documentation process.
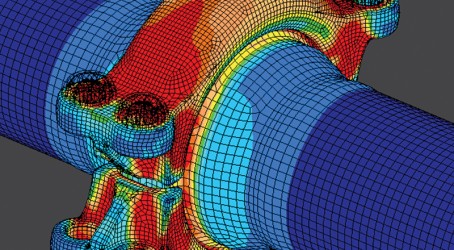
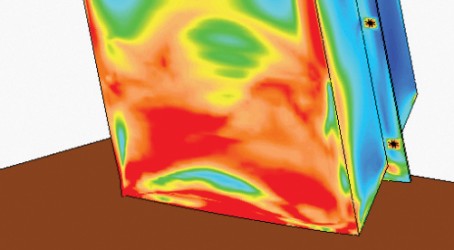
One of the main advantages of these integrated tools is that simulation can be carried out far earlier in the design process than previously. As a result, rather than being a check at the end of the process, when change might need to be kept to a minimum to avoid further cost and delay, analysis results can now be used to influence the design at every stage.
The final piece of the jigsaw is the cloud, which is set to drive the widespread use of engineering simulation more than ever before. Last year, the first “simulation in the cloud” solution was launched. This means that, instead of relying on the conventional server-based set-up, simulation tools can be offered as a service, sitting on someone else’s server.
The advantages of such an approach are clear, says Younis. The cloud offers almost infinite computing power, negating the need for individual firms to buy high-performance hardware. Complex multiple simulation tasks can be carried out in parallel, enabling users to study many design alternatives. This analysis can run on many computers in the cloud. So, in the same time that a single analysis would take on a desktop, the cloud delivers results for all iterations, giving scope for design optimisation.
“Because cloud capacity is bought on a pay-as-you-go basis, using it for simulation is far more affordable than previous methods,” says Younis. “Rather than involving high-level meetings to justify capital expenditure, it can be switched on by the users themselves and paid for as an operating cost.
“There is also no lengthy implementation process, only the need to purchase pre-paid ‘cloud units’ which give access to a range of multi-physics simulation tools without requiring specific licences.”
Of all the 3D design providers, it is, perhaps, Autodesk that has made the biggest strides in the development of simulation through the cloud with the launch of Simulation 360 – a set of tools delivered securely with a pay-as-you-go pricing model. Autodesk believes the cloud will allow complex engineering tests that were once limited to simulation specialists to be performed by mainstream designers and engineers.
For example, Simulation 360 can allow manufacturers to understand the heat generated by electronics devices, enabling them to design in sufficient cooling, avoid overheating and help prevent costly consumer recalls. Engineers can gain deeper insight into how production plants will perform by simulating air flow to help ensure thermal comfort. Architects can use the software to analyse environmental effects on bridges and buildings, and to test the behaviour of structural materials including concrete – all before anything is ever built.
Simulation 360 software already includes a range of cloud-based mechanical, fluid flow, thermal and plastic injection moulding tools on the pay-as-you-go model. Additional benefits include direct geometry exchange; robust meshing tools; extensive materials libraries; and solver technology to improve simulation accuracy in the areas of greatest concern.
One of the greatest worries about software services delivered through the cloud has been security. Autodesk says it views security as paramount, with Simulation 360 built on what it describes as a reliable, protected platform which is continuously tested and monitored. Users are given the tools to control access to their data and monitor assigned permissions at any time. The connection to the cloud is always encrypted, so any data sent, and results reviewed, are protected.
In addition to security practices, there is a characteristic of simulation that makes it particularly well-suited to the cloud, says Autodesk. Because simulation data need not contain as much detail as full CAD files, the software user does not need to transmit all the intelligent product data in design files. This, says the company, allows organisations that do not permit intelligent design files to leave their infrastructure to run simulations in the cloud.
Widespread acceptance of cloud-based simulation is still being hindered by security concerns, says Younis. But he thinks these fears will start to disappear as more engineers begin to access software as a service.
“I would say it is much safer than, say, internet banking. But it remains difficult to convince some customers. However, as time goes by and more and more companies are using it, and we can use reference cases, it will become more comfortable.”