Skills shortages, emerging markets and the economic climate are well-known potential threats to the British aerospace industry, but there is another threat that has been lurking in the background for the past six years and that many are reluctant to talk about. The threat comes from Brussels in the form of chemical legislation known as REACH.
Under REACH, several substances that are vital to aircraft manufacture could be banned from use in the EU by 2017. Unless the industry finds alternatives in the next two to three years, significant parts of the supply chain, as well as the manufacture and maintenance sectors, could risk closure, at a cost of many thousands of jobs.
REACH was introduced in 2007 and is designed to protect human health and the environment from exposure to chemicals. As part of the new rules, the European Chemicals Agency (ECHA) has created a candidate list of substances of very high concern, which can cause cancer, persist in the environment or build up in the body. The use of all substances on this list could be banned in the EU if specific authorisation is not granted.
Several chrome-based substances used in the aerospace industry are on the list. They include the chemicals used in the hard chrome plating of aircraft components to protect against wear and corrosion, engine coatings, paint primers, sealants and substances used in repair processes such as chromic acid anodising and allochrome.
Companies can apply for authorisation to continue using these substances after 2017, but they must do this now, and there is no guarantee it will be granted. It is not yet clear how many authorisations ECHA will make, or what information is required to convince regulators to grant it. As part of any authorisation application, users must prove there are no alternatives to the substance, and show how potential risks will
be controlled.
With the clock ticking, Tomas Polcar, lecturer in nanotribology and coatings at the University of Southampton, says that the cost of finding alternatives, or of proving that substitutions are not possible, will run into millions of pounds over the next few years.
The issues are manifold, he says. The aerospace industry is conservative, and replacing materials is typically a long-term process. Some of the parts used in the manufacture of an aircraft are designed and produced to function for 30-40 years without needing maintenance. Some chromated parts of aircraft – at the end of the fuselage or fuel tanks, for example – are not accessible to monitor for wear, so the longevity of any new technology needs to be guaranteed.
Hard chrome plating and chromatic surface treatments have been used in the aerospace industry for decades. Because of their success, there has been little development of alternative technologies. In addition, the scientists and engineers who created these processes in the 1960-70s have now retired, taking their knowledge with them.
The nature of modern-day aircraft manufacture is also causing problems, adds Polcar. Manufacturers now rely on suppliers to provide parts that are produced elsewhere. Even if a part does not contain any of the substances that could be banned under REACH, these substances may have been used in the production process, unbeknown to the aircraft manufacturer. Aircraft manufacturers now face the difficult task of working out which components fall into this category and the prospect that component producers might stop making specific parts if they do not apply, or if authorisation or applications are rejected. “The problem now is that they have to address all these issues simultaneously,” he says.
Many companies in the supply chain are not willing to spend years, at considerable cost, developing alternatives without knowing if manufacturers such as Airbus are going to like them, says John Archer, research and development manager at surface engineering firm Poeton Industries. “As a coater, we can only do what the aerospace industry specifies,” he says.
Poeton is one of 17 partners working on a Technology Strategy Board project looking for alternatives. The project is led by Rolls-Royce, and includes Bombardier, GE Aviation, Goodrich, Meggitt and Messier-Dowty, as well as the University of Southampton. The £2 million project will look for alternatives to chromate epoxy primers, chromic acid anodising, the use of allochrome and hard chrome plating. It will also look at new test methods to determine if alternative processes are up to scratch.
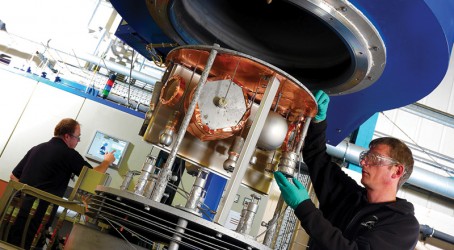
Currently, a salt spray test is used that takes up to 5,000 hours, which is relatively lengthy given the two- to three-year deadline to find replacements.
Polcar says the project should highlight possible replacements for key applications. “They will use this information for negotiations with Europe. We believe that we will be able, in several situations, to replace hard chromium.”
Brian Norton is managing director at Indestructible Paints, one of the companies in the project. It took eight months just to sort out the intellectual property rights to create a contract for the project, he says. He is not hopeful that the initiative will be a success overall. “They won’t have a solution by 2016-17.” Many companies are afraid to discuss the ramifications of not finding suitable replacements, he adds. Boeing and Airbus refused to give a comment for this article.
Norton says that aircraft manufacturers could be tempted to set up plants outside Europe, but he questions the wisdom of this approach, thinking it could lead to more problems. Susan Baker, senior climate and environment policy officer at the manufacturers organisation EEF, says it would be “completely unethical” for activities that the EU deems inappropriate to be exported to other regions. “We need to make sure that doesn’t occur,” she adds.
But the risk that this could happen is real. A letter from the Dutch ministry of infrastructure and environment to the director general of enterprise and industry at the European Commission seen by PE says the measures “may introduce immediate economic damage” for the chrome-plating industry in the Netherlands. Companies that rely heavily on chrome-plated articles will start to move outside the EU as a precautionary measure, because they will not take the risk that in the near future their suppliers are no longer authorised to produce it, the letter states.
Roger Hoodless, senior research engineer and environmental co-ordinator at BAE Systems, says that moving the processes to other countries is not the answer. Similar regulation is being mooted in the US, China, Japan and South Korea. “You will come to a position where those substances aren’t available, so you need to plan,” he says.
But the quest to find replacements is hampered by the fact that the list of substances that could potentially be banned is not yet complete. There are 138 substances on the ECHA’s list, and more are added every six months. Substances that could replace those up for authorisation could also fall foul of the legislation. “You need to plan ahead, but you do need some confidence that those things will not come under the hammer a few years down the road,” says Hoodless.
Typically, the aerospace and defence industry has long time lags between design, manufacture and products entering service, he says. Products that are being designed today might not go into production for another 10 years, and might not enter into service until up to 10 years after that. “The things we are looking at now, we might not be
able to use,” he says. “I see it stifling innovation.”
In addition, any changes to materials will need to be qualified, which takes time and money. Designs will need to be redrawn, and the dimensions rehashed to accommodate changes in the diameter of any new coatings or materials applied to parts.
The legislation also throws up problems for maintenance of the Ministry of Defence’s existing equipment and aircraft for other companies, as materials that could be needed to repair parts might no longer be available. “You can’t just get it out of thin air – you have to do a complete redesign or that equipment is gone”, says Hoodless.
The impact of REACH will be felt in not just the aerospace industry but across British manufacturing, says the EEF’s Baker. “It has the potential for significant competitive impacts. Its scope is only within the EU, which immediately creates an un-level playing field.”
She adds: “Everyone wants REACH to work, but that cannot be at the expense of growth.”
Hardide alternative offers hope
Oxfordshire company Hardide has a potential alternative to the use of hard chrome in some circumstances.
Tests suggest its nano-structured tungsten carbide coating matches the hardness of hard chrome and outperforms it on corrosion and fatigue. Low-temperature, chemical vapour deposition is used to apply a thin layer (see picture, above).
The coating has been used in the Eurofighter Typhoon jet since 2005, and Hardide is working on a testing qualification programme with Airbus.