Every year oil and gas installations burn off 150 billion cubic metres of natural gas, releasing the same amount of CO2 as 77 million cars in the process, according to GE Energy. Flaring gets rid of gas that accumulates underground which can cause a dangerous build-up of pressure during extraction. But as well as wasting valuable resources, flaring releases damaging greenhouse gases and other harmful pollutants into the environment.
While Russia, Nigeria, Iran and Iraq are among the biggest flaring countries in the world, in Europe, the practice is coming under increasingly stringent regulation. Operators of oil or gas installations above a certain size in the UK have to apply for consent to flare waste gases and provide details of how they will work to reduce the volume of flaring. Each flaring installation must be registered under the EU Emissions Trading Scheme and companies must monitor and report total emissions from each flare. Operating permits are free but operators may have to pay for them in the future.
Measuring the amount of gas flared from installations is tricky. TUV NEL senior consultant Lynn Hunter explains there are massive challenges with gas flare measurement as the science is not up to the standard required by regulators.
“Gas flaring is very unpredictable and often happens in a hostile environment,” she says. Offshore installations in particular are open to the elements and space is restricted, which brings additional health and safety hazards and can make accurate measurement difficult.
The nature of the flare itself adds to the challenge. The primary purpose of a flare is to safely dispose of unwanted gas and there are huge variations in the speed of the gas being burnt that can change within minutes. Hunter says: “During background flaring you could have gas velocities as low as 0.05 metres per second. Then you could have it jumping up beyond 100 metres per second in emergency blow-down [when all the gas has to be evacuated from the plant].”
This means that any device installed to measure gas flaring must be accurate at very low and very high levels and according to Hunter many measurement methods struggle to achieve this.
Ultrasonic flare gas meters are the state-of-the-art measurement devices. They comprise two sensors that span the diameter of the flare, with one slightly higher up the flare path than the other. The sensors shoot impulses back and forth to each other and measure the length of time it takes for each impulse to travel across the flare. As one pulse will be travelling in the direction of the gas flow and the other will be opposing it, the time difference between the two impulses gives a measurement of the rate of gas volume. Multi-path meters, which use several pairs of sensors to get a more complete picture, are also available.
Although these meters are the preferred technology they have drawbacks. If the path of the flare bends or there are other disruptions to the flow of gas, measurements can be “seriously inaccurate”, says Hunter. “There is quite often an assumption that the meter is accurate over the full range of flaring. A flare gas meter can be inaccurate at the low end and the high end.”
As UK law does not require meters to be fitted on flare stacks, operators can use mathematical models to calculate gas flare emissions based on readings from meters on lines that contribute to or export from the flare path. This is known as the mass-balance method and relying on it solely to determine the gas flare measurement is “extremely flawed”, says Hunter. It is especially inaccurate when flaring is low. “I’ve seen 100% inaccurate,” she says.
An added challenge to measuring flare emissions directly or indirectly is that the gases expelled from the stack can vary greatly in temperature and composition.
“During blow-down you could quite easily have liquids and solids making their way through the flare line and this can affect the ability of the flow meter to measure accurately,” she adds.
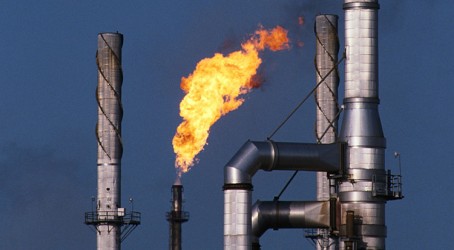
The accuracy of gas flare measurement is important because the figures are used to estimate the carbon emissions from the flare for reporting. Operators are required to report the estimated accuracy of the flare carbon emissions measurement and this must fall within a specific range of uncertainty, which varies depending on the size of the installation.
Hunter explains that although operators’ figures for measurement uncertainty can appear to meet the European Trading Scheme requirements, in reality this is often not the case. “Potentially, the majority of operators are unaware of these underlying issues that could impact measurement uncertainty,” she says. Meters and models are often not calibrated, she adds, and believes it will take up to five years for the science to catch up with the legislation.
Currently, if an operator cannot meet the assigned uncertainly range they must present to regulators a plan outlining how they can improve measurement accuracy in the future. But this leniency might not last forever.
“So far the UK has generally been sympathetic,” explains Hunter. This is because installing sophisticated measuring technology is a major undertaking that requires a costly production shutdown.
“But I suspect that the next stage of the Emissions Trading Scheme will be more stringent as the European Commission takes a greater handle on trying to push forward the requirements,” says Hunter.
The next phase of the scheme is due to start in January 2013. By 2013 the price of carbon is likely to reach 30 euros per tonne, at least double the price currently speculated, and some operators are taking steps to reduce the amount of flare gas they release.
Flaring cannot be eliminated entirely because it is an important safety mechanism. But a number of technologies are available that make use of the gas that is flared.
Which technology to use depends on the location of the installation. Often the excess gas can be re-injected into the well to help maintain the pressure of the reservoir. Offshore, it might be possible to build a pipeline to shore that can transport the gas for use on land. Michael Farina, programme manager at GE Energy, says that often operators can piggyback on established pipeline grids. “You can tie back to an existing platform and they will process it and pipe it out,” he says.
Another option for offshore operators is to use the gas to generate power for the platform itself, adds Farina, which can be done by fitting an air derivative turbine. These relatively small, high-power-density turbines have a lighter footprint and can kick out anywhere between 25 and 60MW of power. But there is only so much power an installation will need and there could still be leftover gas.
The excess can be converted to liquefied natural gas, which is a fairly simple fuel conversion, or other liquids. “The technology for gas to liquid conversions has really come along in the last five years and we are going to see a lot more of it in the future,” says Farina. Pilot projects in Brazil are looking at converting methane into a liquid that can be dropped straight into the crude oil stream.
In an onshore environment, a similar set of options for using waste gas exist. The excess gas can be re-injected, used to run the field operations or it can be piped elsewhere. Without the weight and space issues of an offshore environment, gas engines can be used to generate local power in remote areas onshore.
More innovative uses for waste gas may become available in the future. “People are talking about flare to fertiliser concepts, or direct conversion into methanol,” says Farina.
Most new oil and gas projects have plans to manage flaring in place from the outset, says Farina. But old rigs in some countries may continue to flare until the wells are depleted. Farina estimates that the flaring of waste gas is likely to continue for at least 10-15 years even though technologies to reduce it are available. “Its a political will issue,” he says.