Engineering news
The Bloodhound team has successfully tested the hybrid rocket engine developed for its land-speed record attempt in South Africa in 2014.
The test took place yesterday at Newquay Aerohub in Cornwall, with a live feed transmitted to an audience of engineers and school children at the site and to thousands of others via the internet.
The rocket was the largest to be tested in the UK for 20 years. Richard Noble, Bloodhound project director, said that the test had “exceeded our expectations” and had represented the project's most significant milestone yet.
The hybrid rocket engine uses a solid rocket fuel in combination with a liquid oxidiser to generate power. The set-up under test comprised a Cosworth F1 engine; a rocket pump; 400kg of concentrated hydrogen peroxide (HTP) to act as the oxidiser; a catalyst pack; the hybrid rocket and a supply of solid rocket fuel.
In total the system measured 4 metres in length and weighed 450kg. It was the first time that engineers had tested all the components of the hybrid rocket engine together.
During the test, the F1 engine powered the rocket pump, which pumped HTP at high-pressure through the catalyst pack. The catalyst pack contained layers of mesh made from silver oxide that broke the HTP down into oxygen, water and heat under pressure. At this stage the inside of the rocket reached temperatures hot enough to burn the rocket fuel, with the combustion producing 14,200lbs of thrust.
Before the test engineers were not sure whether the silver mesh would collapse under the force of the pumped HTP or whether the expected thrust would be generated.
The firing itself took place in a hardened air shelter and saw the rocket burn for around 10 seconds. At the rocket nozzle sound levels reached 185dB.
During the test a pressure of 820 pounds per square inch was reached - 20psi higher than engineers had expected. Just a day before the test, after several successful pre-test runs using water, the Bloodhound rocket team decided to up the pressure levels for the test from the 600psi originally planned.
Commenting on the increase of pressure tested, Noble said: “I was a bit surprised by that. The rocket team decided they would push ahead and try it. It was a slight gamble because if the catalyst pack had failed the rocket run would have failed. But it didn't.”
He added: “From the rocket point of view we got stable combustion, which is great. It's quite clear that the development of the mono rocket using purely the HTP is going to be fine. But we have still a long way to go with the hybrid rocket to get the level of power that we need.”
Noble said that the rocket team would soon meet to discuss how the tests went and decide the way forward.
Eventually, the hybrid rocket will need to run at 1,000 - 1,100psi in order to produce the 27,000lbs of thrust that will be needed to help propel the car to 1,050miles per hour in South Africa. During the record attempts the hybrid rocket will work alongside a Eurofighter Typhoon jet engine.
Daniel Jubb, creator of the hybrid rocket, was pleased with the results of the firing. Speaking directly after the test he said: “It appears to have gone very well. The only real problem was that the motor took longer to extinguish than expected and it took out the CCTV.”
Following the rocket's firing a fire developed in part of the system. Smoke filled the hardened shelter and the live feed between the rocket and the engineers cut out. According to the team the fire was caused by the purging of the HTP tank while a little oxygen remained inside.
Jubb added: “It was not a serious concern. We managed to get a full data set which is bang on the numbers. I'm very pleased. The tests were a big risk to the programme but this is a good first step and we will push on from here.”
Mark Chapman, chief engineer on the project, said: “The atmosphere on the team is electric.”
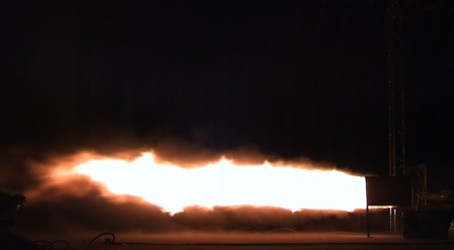