Attack defence: Tanks could use smoke and manoeuvres to counter a threat
The British military drawdown out of Afghanistan is in full swing. This year, alongside the last 5,200 troops, British forces will return 3,345 vehicles to the UK. The cost of this drawdown is £300 million, says the Ministry of Defence.
As the Mastiffs, Jackals, Foxhounds, Bulldogs and Warthogs roll back onto British soil, there is an opportunity to take stock. The technology in these and other armoured vehicles has evolved radically over the past decade, and what happens to them will reveal key characteristics about the factors influencing their design and where technology will drive them next.
When the first British troops entered Iraq and then later Afghanistan, it soon became apparent that the existing fleet of protected vehicles were ill-equipped to deal with the threats they faced. Too many soldiers were dying in attacks using weapons such as improvised explosive devices. The military had to both ‘armour up’ the existing fleet and quickly develop new base-level vehicles with more suitable protection.
“In the past 10 to 15 years, we’ve been working hand-over-fist to provide the best protection possible for our forces, first in Iraq and then in Afghanistan,” says Professor Bryn James, a senior fellow and technical lead on armour and protection for vehicles, individuals and bases, at the Defence Science and Technology Laboratory (DSTL). Engineers at DSTL support the whole armoured vehicle supply chain, setting programme requirements, working out how to test for them and helping industry to meet them.
“When we started, we used the vehicles we had – some of those were already our most survivable. There is a compromise between mobility and protection you have to make, and for their weight they were the best,” says James.
During the conflicts, engineers strove to improve vehicles’ survivability in response to a range of rapidly changing threats. This process resulted in a fast-moving game of one-upmanship between engineers and the opposition.
James says every resource possible has been poured into efforts to improve British forces’ armoured vehicles recently. “Some of the vehicles have been up-armoured several times,” he says. “The progression has been rapid. We have a fleet of vehicles with better protection than we’ve ever had. We are now rationalising the lessons we’ve learnt about the fitting of armour to come up with solutions that will meet future needs.”
A key part of the Army 2020 programme – an ongoing review and restructuring of the British Army – is working out the best way to make use of the thousands of vehicles returning to the UK. The vehicles are tailored for use in the desert environment. They have to become more flexible and affordable while still giving protection from threats. “When you have invested so much, you have to be able to use them in all sorts of conditions and applications,” says James.
The key to unlocking affordability and flexibility is the armour and the crucial relationship between mobility and weight. The heavier the vehicle, the worse the wear on its chassis and components, plus the greater the running costs. Reductions in the vehicles’ lifetime, reliability and availability need to be avoided.
So engineers at DSTL are developing modular, generic armour and fixings that are as standardised as possible across different vehicles. There is already modular armour on vehicles such as Warrior and Bulldog, but swapping it can take days. The aim is to get this time down to a few hours, make the process as cheap and easy as possible, and extend it to other vehicles.
It isn’t the most exciting engineering, says James, but it is key to survivability and to the future use of the vehicles. “They want the armour lighter, smaller, cheaper, and they want it yesterday. We have to make sure that you can put it on the vehicle and it stays on. It’s more difficult than you’d think to come up with fixings to do that,” he says.
It’s not all about dumb plate metal though, he says. For example, the DSTL is still looking at ‘active integrated protection systems’, also known as ‘hard kill defence aid systems’. These armour systems use a suite of sensors to detect an incoming threat and then deploy a response to counter it. The response could be smoke and manoeuvres, or something more aggressive. The systems are available, but the DSTL says there are “practical issues” to their use in the field, which are being worked on.
Another idea is electric armour, for which the DSTL hopes to have produced an effective prototype in two to three years. Two electrically conducted plates are attached to a power source and arranged so that when a projectile goes through the first plate a massive current causes the projectile to explode, reducing damage and improving survivability.
This work is being conducted in parallel with efforts by US defence scientists and engineers, with whom the DSTL shares all research and has an “exceptionally good relationship”, says James.
An additional area that the DSTL is investigating is novel materials for use in armour, and these could be seen on vehicles in the future. One material that is particularly promising is ultra-high molecule weight polyethylene, a tough material used in several civilian applications, including synthetic ice rinks and hip and knee replacements. James says it is a “wonderful material with incredible properties that we are finding uses for everywhere”.
Composites are under constant development, as are aluminium alloys and super bainitic steel. The latter material is cheaper than rolled homogeneous armour steel – which has a high percentage of nickel – while retaining all of armour steel’s properties. Super bainitic steel can also be shaped more easily into different chassis designs.
“The thermomechanical treatment used for conventional armour steel means the production of anything other than flat plate is problematic. But the heat treatment you can use with super bainitic steel means you can bend it, machine it, cut it in a soft state and then temper it. It makes fabrication of components much cheaper,” says James. Other materials engineers are looking at include recycled titanium and ceramics which, although expensive, have a high performance that make their use worthwhile.
The key tool for developing armoured vehicles is increasingly powerful and accurate computer modelling and simulation software, says James. Physical testing can be “extraordinarily expensive”, which limits the number of tests. Computer simulations are cheaper and can recreate a wider number of unavailable enemy weapons and ‘big’ events.
“It’s difficult to put armour onto vehicles that are different shapes and sizes,” he says. “When you’ve worked out the requirements, you have to do complex engineering for shock and blasts. Under impact or blast conditions the strain rate, pressure and temperature can all be very high. We have to know the material properties in that state and its failure characteristics, and to model them,” he says.
Jim McKechnie, principal project engineer for armoured vehicle company Supacat in Devon, agrees that computer simulation has made massive improvements possible in armoured vehicles. “It lets you see what is happening to the structure inside the vehicle: how it is bending and buckling, and how it affects internal components such as the gearbox and drivetrain, as a blast happens. Without it, you would be back in the old days of trial-and-error tests,” he says.
Supacat is best known for developing the Jackal and Coyote vehicles used by British forces in Afghanistan. The company also narrowly missed out on a high-profile contract to supply the British Army with the replacement for the Snatch Land Rover, a vehicle that received much criticism for its lack of protection when forces were first deployed in Afghanistan. In 2010, the MoD selected the Foxhound instead of the Supacat protected vehicle 400 (SPV400) for its light protected patrol vehicle (LPPV). Both vehicles feature the V-shaped hull that improves blast resistance.
In the design of the SPV400, Supacat used its own bespoke version of modelling and simulation software LS Dyna, enabling it to reduce costs and development time. According to Jamie Clarke, marketing manager at Supacat, the company was able to do 16 blast tests compared with the 45 that its competitor performed on the Foxhound – a sizeable saving when each test costs around £250,000.
However, losing out in the UK has not meant the end of the line for the SPV400. Last month, Supacat and Indian automotive manufacturer Tata Motors showed off the results of a technology transfer partnership between the two companies. The light armoured multipurpose vehicle (LAMV) uses the crew protection and suspension technologies from the SPV400, including the V-shaped hull, and an all-composite crew cab. LAMV will be manufactured in India, where hundreds of them could be purchased by the government.
A team of Supacat engineers have been working in India with what McKechnie describes as an “open book” on the “bulk of the work”. “It’s given them a head start in some areas such as the V-shaped hull,” he says. “Once you’ve committed to the V-shape, it becomes an engineering challenge to accommodate it. You have to look at the system as a whole – where the seating is put, the engine, gearbox and transmission. The engine and gearbox are decoupled and connected by a prop shaft, which causes other challenges.”
McKechnie adds that the biggest short-term changes in armour-protected vehicles in general are the trade-off between mobility and armour weight and the progress that new materials are making possible in this relationship. “Composites, ceramics and other materials are getting more available at better prices, bringing costs down,” he says. “On the composite side, it’s helping with ballistics protection.”
Clarke says that as with other commercial companies, the vehicles the company develops are ultimately designed to meet the needs of its customer – the MoD and the armed forces that use and depend on the vehicles every day. “The market for armoured vehicles is evolving. The conflict in Afghanistan has driven a particular set of requirements. But no one knows where the next operation will be. So we have to offer high mobility over a wide range of terrain and future-proofed, modular armour designs.”
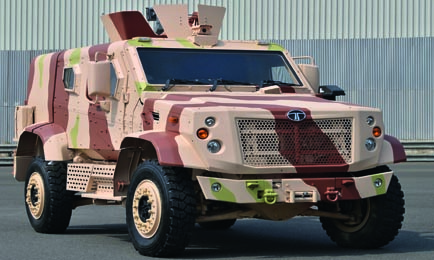
Conquering fresh territory: Supacat has been working with India's Tata to create the LAMV