GKN Aerospace’s Filton plant in Bristol is the epitome of structured calm. Workers move with a swift purpose along lengths of A380 wing structures that stretch far into the distance. In another part of the facility, inner spars are pieced together with care. The place is as tranquil and efficient as a manufacturing facility can be.
This air of serenity belies Filton’s recent past. For many years the plant existed in isolation, producing parts for one company – its parent firm Airbus. But in 2009 the manufacturing operation was acquired by GKN and the business model was rapidly changed.
Filton was expected to compete for and win work from other companies, removing the feeling of uniformity that employees had got used to. Some manufacturing activities ceased, with the work being outsourced. Other tasks were brought in-house, requiring new departments and staff. It has been a long and at times challenging transformation, but one that is now bearing fruit in terms of new business and opportunities.
“Installing a new culture within the plant was a big challenge and it’s fair to say that it has been a hard journey for us,” admits Charles Paterson, GKN’s vice-president of business development for Europe. “People had got used to being comfortable in a large umbrella organisation. The plant goes back a long way – more than 100 years. Moving to a new environment was very different for people.”
The plant had evolved into a crucial manufacturing facility within Airbus, employing 1,700 workers and making major components including leading and trailing edges, wing boxes and machined parts in hard metal and aluminium. A review of operations as part of the Power8 restructuring programme prompted Airbus to sell the plant to GKN for a fee in the region of £130 million.
Filton was a good fit for GKN’s aerospace arm. It offered the chance to get a better balance between civil and military aircraft within its aerospace portfolio, and it gave GKN the opportunity to go from being a tier 1-2 to what is known as a super-tier 1. Almost overnight, GKN became the biggest single supplier to Airbus on wings, and the third biggest aero-structure supplier overall. “It made a huge difference to our positioning in the aerospace sector,” says Paterson.
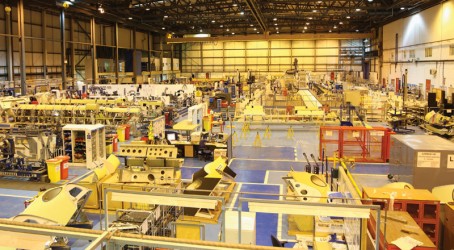
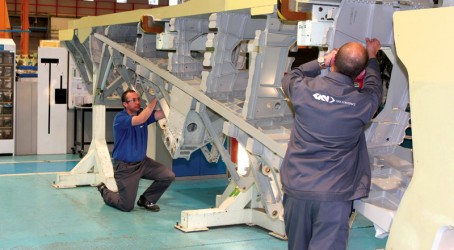
But it’s not easy taking one historic business and fitting it seamlessly inside a larger organisation. GKN operated with a very different business model than the Filton plant had been used to. It operated as a highly distributed model, with each facility structured into a separate, standalone reporting unit issuing its own profit-and-loss statement. That was very different from a manufacturing facility that had got used to being handed down work packages from a parent group and therefore had very little commercial experience.
“Turning it from a manufacturing unit into a standalone business was the first real challenge we faced,” says Paterson. “Each of our reporting units are fully accountable for all aspects of their business, so we needed to add new functions such as sales and marketing, IT, human resources, procurement, finance, and design.
“With that came a reorientation of the people who were already in the organisation. We said this is now a business, we stand on our own two feet as a profit-and-loss organisation. We became the biggest reporting unit in a company that is quoted on the FTSE 100. And with that came a lot of accountability and corporate governance. It was apparent that it had to become a very different place from a manufacturing unit inside a large organisation called Airbus.”
Paterson admits that some painful decisions had to be made. It was felt that it would be better to buy components such as electrical harnesses from the supply chain, rather than making them in-house. That led to some streamlining and reorganisation. There was also the need for some changes to working patterns to improve efficiency.
“People found it a challenge to adjust to some of the things that we had to do but we assured them that the reason we were doing it was to make sure that we were competitive.
“In the old organisation work packages used to be handed down from Airbus – Filton didn’t have to compete for them. Now we have to compete and win all new work packages. It was down to the management to lead the organisation along a road so that it wins business.”
There were advantages to this approach. GKN Aerospace has invested heavily in engineering and design skills and facilities at the plant. It has also spent large sums on new machine tools to enable it to produce a wider variety of parts. Paterson says that a process of continuous improvement has also been implemented to improve performance and to make Filton globally competitive.
The ultimate aim was to secure additional work to that provided by Airbus, and slowly but surely that ambition is being achieved. The first major new customer was the French firm Dassault Aviation, which provided Filton with a “life of programme” contract to design and build the wing movable surfaces such as flaps and ailerons for its next-generation business jet, with first production deliveries starting in 2013. Paterson says GKN will bring significant performance, weight and cost benefits to the wing of the new airframe and that engineering teams co-located in Filton and France are already working on the programme.
GKN has also won a $200 million contract to make metallic structures for the Joint Strike Fighter (JSF) military jet programme. Specifically, titanium metal structures machining work is being spilt between Filton and the company’s St Louis plant in the United States. Other work includes supply of the canopy transparency and titanium and composite structures for the engine.
He says: “The JSF work package is at the start of the programme and there are some reviews taking place looking at exactly where it is heading in terms of numbers and volumes. But it will certainly ramp up to a high-rate programme.” He is also confident of winning other work packages, saying that Filton has “a number of irons in the fire”.

When GKN Aerospace bought Filton, the ultimate proof of the business’s transformation was said to be winning work with Airbus’s arch foe Boeing. To date this hasn’t happened, but Paterson says talks are ongoing with the US firm. “We already have a massive amount of work with Boeing around our other sites, but that’s mainly on the military side. Dialogue is now taking place with Boeing’s commercial people with a view to work packages coming here,” he says.
Airbus remains by far and away the largest customer for Filton based on work volumes. Paterson says this will be the case for many years looking forward but other customer work is growing. “The outlook is very good – we are going from strength to strength on Airbus programmes and our work to grow the customer base is succeeding.
“For Airbus today, we’ve got a large work statement on the A380, A400m and A330. We’ve also got the A320 family – production rates are going up and we’ve got strong work placements on that programme. With this, our growing orderbook for other manufacturers and our prospects for new business, it looks really good for us for quite a few years,” he says.
Driveline advances
The automotive side of the GKN business continues to excel, with the company using the recent Geneva motor show to exhibit several advances in driveline technologies.
Electronic Torque Vectoring
On the new BMW X6 M50d, this is an active torque management device designed to overcome the tendency of vehicles to understeer under power in corners. The ETV applies an additional yaw rate to the vehicle to improve agility, handling and to stabilise the vehicle under power. This yaw rate is realised by distributing drive torque individually to both wheels of one axle through the ETV.
Electro-Magnetic Control Device
A key component in the driveline of the new Mini JCW Countryman ALL4, the EMCD is an actively controlled coupling in on-demand and full-time all-wheel drive mode controlling the driveline power flow for two- to four-wheel-drive vehicles to provide optimum performance when needed. At extremes, up to 50% of the power can be sent from the primary driven axle to the secondary driven. Most often the EMCD will be working to provide optimum apportionment of power between rear and front wheels in a wide range of driving manoeuvres, for instance when accelerating from a stop, enhancing control in corners, or adapting to icy and snowy roads.
Power Transfer Unit
An integral part of all-wheel-drive systems, the unit helps to optimise traction by transferring drivetrain torque to the rear wheels to improve traction – a vital feature for driving in snowy, icy or wet conditions.
Electronic Torque Manager
Fitted to the new BMW M6 Coupe, the ETM on all M-series vehicles is a rear-axle differential with an integrated active differential that provides greatly enhanced traction and stability through high-speed optimal torque allocation to the powered wheels. Its integrated electronically controlled direct actuation makes it a highly suited module for improving dynamic performance in performance cars in all road conditions. The new M6 Coupe is also fitted with GKN Driveline CVJ systems.
Direct Torque Flow
As fitted to Audi’s third-generation A6 Allroad Quattro and the Audi RS4 Avant. The DTF is a means of connecting the car’s transmission with the rear differential in a way that saves weight, assembly time, space and cost on the longitudinal shaft. With DTF technology, manufacturers can do away with bolts, washers, flanges and one stub shaft, and be assured of conveying the power and torque of the gearbox output to the rear differential in a way that greatly reduces the risk of NVH and shaft imbalance.