Every engineer understands the importance of making the correct material selection if the product or application they are creating is to be successful. Material selection also has to take into account the intended manufacturing route for design. So, it probably comes as no surprise that material selection is similarly important when 3D printing is the chosen method of manufacture, regardless of whether the objective is to produce a visual or functional prototype, or a functional end-use part. Ultimaker 3D printers are optimised to use the Ultimaker range of materials, but also third-party materials from the Ultimaker Material Alliance program. Many material manufacturers provide print profiles for their filaments in Ultimaker Cura. When multiple Ultimaker 3D printers are operated in a contained environment, emissions of UFPs and/ or VOCs may vary. Ventilation should be considered when using materials with specific safety requirements. When using print profiles from the Ultimaker Material Alliance and/or other suppliers you should check the safety data sheet of each material for information.
The 3D Printing Materials Landscape
The expanding and changing face of polymer materials that can be used on desktop printers, including some of the latest material developments such as Jabil PA0060, Infinite Systems Caverna and BASF Ultrafuse 316L.
Polymer-based materials that can be used on desktop 3D printers have expanded at an incredible rate in recent years, which has been more than a match for the development of the printers themselves. New and exciting materials are being added to the list of 3D printing options every week.
Ultimaker is a manufacturer of desktop printers who have had an open-source ethos from their inception, and that philosophy has extended into the materials that can be used with the 3D printers they manufacture.
They have not followed the business model of the inkjet printer market where you need to buy branded cartridges locked to their machines. Instead they have adopted an “open-material” approach where they have encouraged third party material providers to develop materials that can be successfully printed on their Ultimaker 3D printers. The benefits of this has been an incredible rate of growth in the materials available for desktop 3D printing and, more importantly, has contributed hugely to the range of applications that can be supported through this branch of additive manufacturing. With Ultimaker's complete, integrated, and open source 3D printing platform, organisations can simplify supply chains, achieve lean manufacturing best practice, and improve the ergonomics and effectiveness of the parts produced.
One of the most significant strengths of FFF printing is the number and variety of materials you can use. Ultimaker 3D printers have been optimised to use the Ultimaker range of materials. Although, the flexibility of the open platform makes it possible to use a range of 2.85mm filaments from other vendors. When it comes to the application possibilities there are many, below are some of the 3D printing applications that demand high-performance materials.
Tools, jigs and fixtures
Tools, Jigs and fixtures are custom parts that make manufacturing easier. Traditionally they would be outsourced, however, this process is costly, results in long lead times and often requires excess storage. With 3D printing you can fabricate parts on demand, for a fraction of the material cost, and can iterate as needed.
Quality assurance tools
L'Oreal is a leading example of an organisation maintaining quality standards by using 3D printers to create precise gauges that allow staff to spot-check product label placement. This is an essential part of any production line and due to their simple design, many devices that check for and prevent defects can be 3D printed. This can include multipurpose measuring tools, shapes, placement gauges, or mistake-proofing devices. For the quality assurance device that L'Oreal manufactured the print requirements were tight tolerance, low friction coefficient, and wear-resistant. For these requirements they used DSM Novamid 1030.
Manufacturing aids
Improvements, however small, in an automotive assembly line can make a huge difference to productivity. Assembling a car involves thousands of separate tasks, in-house 3D printing accelerates the creation of new and optimised tolls, jigs and fixtures.
For example, Volkswagen Autoeuropa improved tool ergonomics by 28% and final product quality by 35%. This saved them £410 over two years. The 3D printed wheel protection jig was previously sourced for £691.03, and can now be printed for £18.14. The material properties required for this part had to be semi-flexible, wear-resistant, and have high dimensional stability. For this they chose to use Ultimaker TPU 95A, Nylon, and Tough PLA.
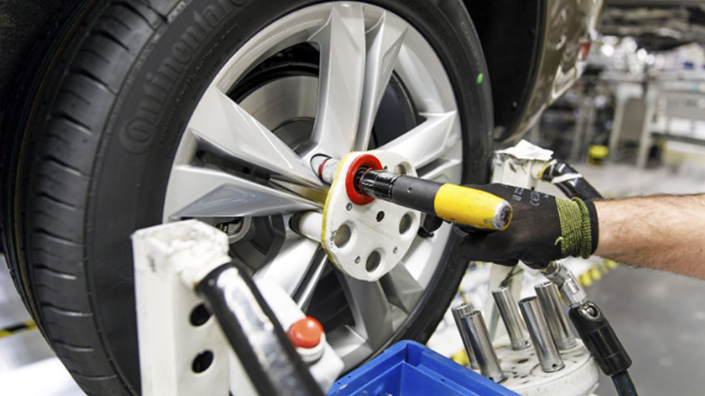
Ultimaker Materials Alliance
The Ultimaker Material Alliance has 220+ materials available providing a wide range of material properties. This makes selecting new materials much easier than before the platform was introduced.
As a result of the open-source approach, and the consequent growth in the materials market, Ultimaker created what they call the Ultimaker Material Alliance. Through creating partnerships with third party material providers Ultimaker can deliver material printing profiles which contain the key parameters for successfully 3D printing. Prior to this alliance it would be down to the individual 3D printing user to fine tune the print parameters for each new material that they used, usually through a time-consuming, trial and error approach.
The Ultimaker Materials Alliance has changed all of that. Now, all of that experimentation, fine tuning, and optimisation of the print parameters is carried out by the material provider and is validated by Ultimaker before that material is signed off for incorporation into the Alliance. As a result, printing with a new material now involves just a couple of mouse clicks in order to be confident that the first print will be a successful one.
To date, there are 228 material profiles available through the Ultimaker Marketplace which cover a large number of different polymer material groups, with a correspondingly wide range of material properties available.
Choosing The Right Material
3D printing is opening up easier manufacturing of parts and this is displacing the use of metals for applications such as jigs and fixtures. The question is where to start in making sure that you’ve selected the right polymer for your application.
One trend that 3DGBIRE is seeing is the adoption of desktop 3D printing as a method of fabrication that can deliver both time and cost savings, especially when it comes to things such as jigs and fixtures. These are often made from metals because of their ease of fabrication and not because they need to have the strength of metal for the application itself. Using polymers for these applications is now a viable option since 3D printing has made fabrication so much easier.
But where do you start when it comes to selecting the right material for your application, especially if the world of polymers is new to you? The Ultimaker Marketplace can search by brand, material group, or more importantly by characteristics. Using the latter allows you to filter in the type of characteristics you are looking for in your application and it will help identify through the 228 materials in the database to give you a more focussed list of materials that will meet your requirements.

Identifying what you intend to 3D print is only the first part of your FFF journey. Next, you need to decide how you will use 3D printing. This can vary depending on the scale of your business, the skills of the workforce, and what you are producing.
By eliminating outsourcing, your development cycles will be faster. Before you start 3D printing in-house you will need to answer a few key questions:
• Which 3D printer is right for me? How many do I need?
• Which materials will I print with? Are they readily available?
• Do we have the necessary CAD skills within the team? And software packages?
• Where will we install the printer (or printers)?
Once you have clarified these questions, you can begin to implement a 3D printing workflow that is optimised for your specific business needs. As an example, the diagram below outlines a typical workflow of a 3D printer such as those from the Ultimaker S-line range.
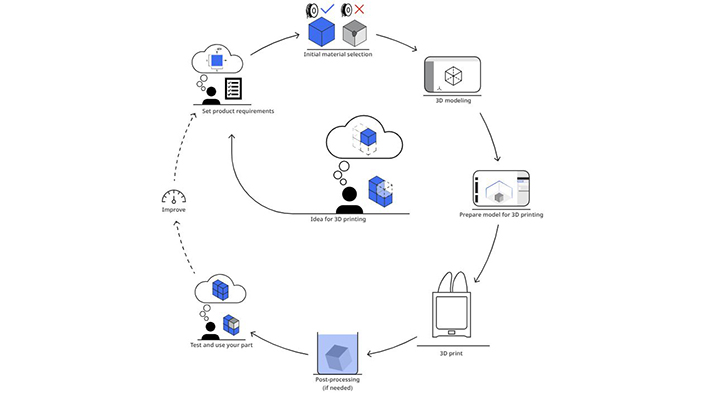
The Alliance in Practice
Installing and using a material profile from the Marketplace.
Once you’ve selected the material that’s ideal for your application and got hold of a reel of it then getting printing with it is exceptionally easy. Inside Ultimaker’s slicing software, which is called Ultimaker Cura, there is a built-in Marketplace link where you can search for the material you have selected. To get started simply install the appropriate material profile to take advantage of the necessary print parameters that have been developed and validated for that material being loaded.
Things such as printing temperatures, build plate temperature, printhead speeds, material flow rates, cooling rates, recommended wall thicknesses, infill patterns, and infill densities to name but a few are then automatically set when the material is selected.
The Power of the Alliance
The advantages of dual material printing and how using materials from two different material suppliers with different characteristics can be successfully combined. Including how the Material Alliance also plays out into other areas such as Teton Simulation’s SmartSlice where third party materials can be analysed for functional performance inside Ultimaker Cura.
The ease of use, and the wide range of available material profiles from a large number of companies, provides interesting opportunities. For instance Ultimaker S-Line printers are capable of dual extrusion printing where two different materials can be extruded on each layer of the part. That means two very different materials, possibly from two completely different companies, can be combined together in a single part.
For instance, in this example there is a structural performance requirement on a part that is fulfilled by using a polyamide material made by Fiberthree that carries chopped carbon fibres. At the same time the application requires certain areas that need low friction, wear-resistant characteristics which can be provided by a so-called “tribo-filament” made by Igus. Two different material providers, two different characteristics, combined successfully in one 3D print, all enabled by the power of the Ultimaker Material Alliance.
The Material Alliance is also playing out into other areas of the 3D printing eco-system. Teton Simulation’s recently launched SmartSlice software allows you to perform stress analysis of your 3D print directly inside Cura. This ensures that you will meet your structural functionality needs and to set the print parameters that you need to specify in addition to the material parameters. SmartSlice has around thirty materials from the Material Alliance in its database that have been experimentally tested for their material properties in order to ensure the highest fidelity of structural analysis is achieved.
.jpg?sfvrsn=3fc9512_0)
Ultimaker Dual Extrusion 3D Printers
If you are interested in saving time and money and are tired of outsourcing and inefficient production processes. Whether you are looking to scale up and unlock demanding applications or looking on a smaller scale a more cost-effective way to adopt in-house 3D printing. The Ultimaker printers offer dual extrusion that integrates with your workflow.
Ultimaker S5 Pro Bundle
![Ultimaker-S5-Pro-Bundle-Studio_41 (1)[1] Ultimaker S5 Pro Bundle](https://imechewebresources.blob.core.windows.net/imeche-web-content/images/default-source/default-album/ultimaker-s5-pro-bundle-studio_41-(1)-1.jpg?sfvrsn=6f269412_0)
A unique production solution gives busy engineers and designers the freedom to focus all day on doing their best work. Transform your office 3D printing workflow with automated material handling, air filtration, and filament humidity control. The Ultimaker S5 Pro Bundle boosts productivity, flexibility, and confidence to unlock demanding applications with an extended range of materials.
Learn More
Ultimaker S3

The Ultimaker S3 features next-generation reliability. Its advanced active leveling, stiffer build platform, heated build plate, and more accurate stepper drivers result in the highest print quality of a machine in this form factor. And dual filament flow sensors notify you if you run out of material.
Learn More
Conclusion
How the Ultimaker Material Alliance is making adoption of new materials easier and, in the process has also opened up amazing application opportunities.
The Ultimaker Material Alliance really is a powerful tool that assists you in selection of the right material for your application and gives the highest possible chance that your first experience with a new material is a successful one. This allows easier integration of materials into multi-material designs to provide targeted characteristics and supports some of the most interesting new developments in the ecosystem supporting successful 3D printing adoption
3DGBIRE Ltd is the premium service & training provider for Additive Manufacturing For Industry within the UK and Ireland. By offering high-quality products and customer-focused service, sales and technical support, we will ensure that all industries have the resources they need to unleash their creative potential while successfully integrating additive manufacturing into their entire business cycle.
If you want to know more about the Ultimaker Materials Alliance, and how we can support you with successful adoption of 3D printing through the full combination of hardware, software, materials and support, then please contact 3DGBIRE.
3DGBIRE offers both physical and digital solutions and treats every employee and customer as a priority. By implementing efficient systems and listening to our community we bring together the world of 3D FFF & DLP printers, premium scanners, filaments, resin, spare parts and service plans that guarantee complete satisfaction.
To join others in driving sustainability and innovation - book a 360 business consultation with one of our AM consultations: 01257 228411 or enquiries@3dgbire.com
Want the best engineering stories delivered straight to your inbox? The Professional Engineering newsletter gives you vital updates on the most cutting-edge engineering and exciting new job opportunities. To sign up, click here.
Content published by Professional Engineering does not necessarily represent the views of the Institution of Mechanical Engineers.